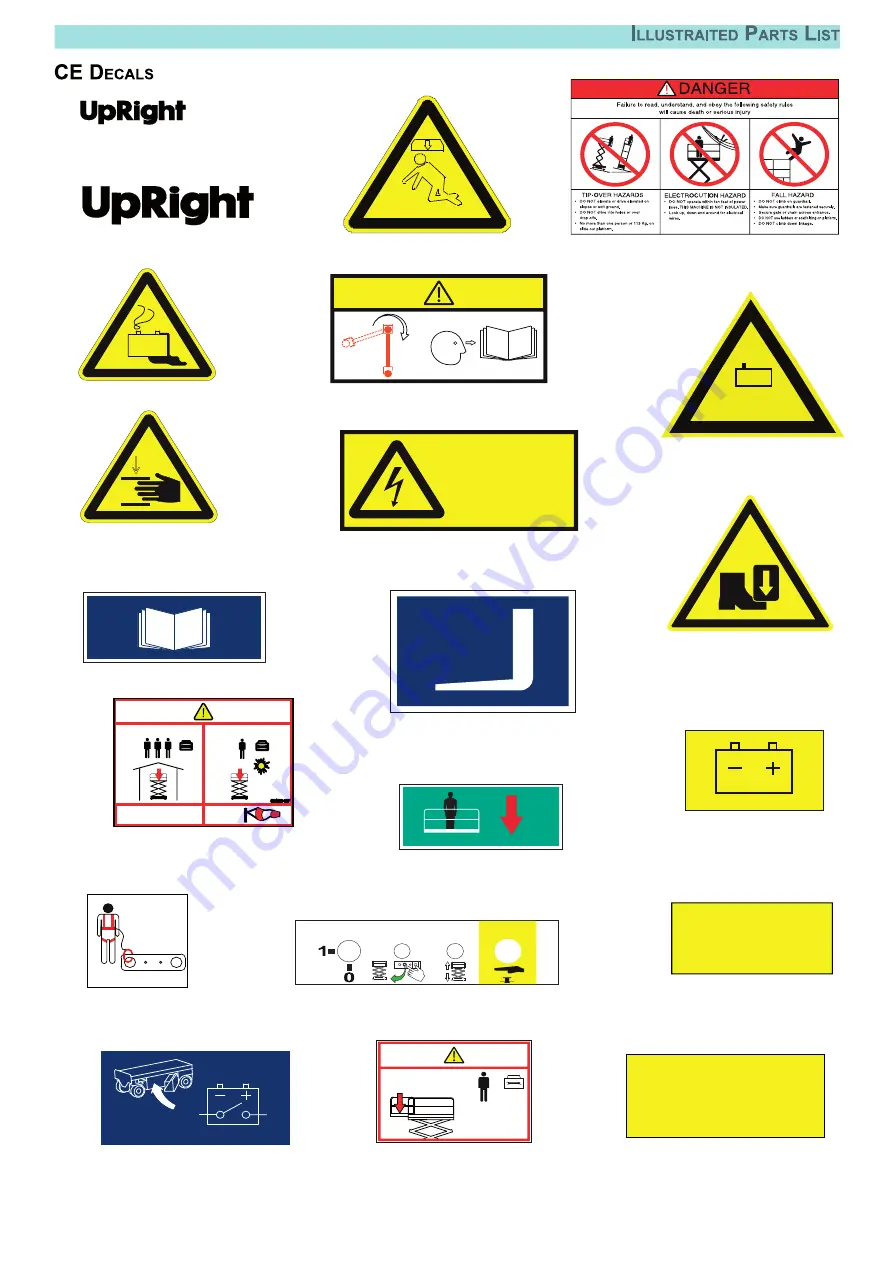
BATTERY
MAINTAIN BATTERY FLUID
AT RECOMENDED LEVEL
005221-000
HYDRAULIC FLUID
HYDRULIKOEL
HUILE HYDRAULIQUE
FLUIDO HIDRAULICO
060197-001
9
100102-900
066561-900
067195-001
068635-001 x2
12
19
503724-000
x2
067195-001
15
101210-000
101210-000
11
2
3
21
20
18
10
13
066561-900
1
4
7
8
5
6
14
16
17
508661-000 x2
X26N
508669-000 x2
010076-901
100076-901
- +
26.3 kg+
062562-951
x4
066556-900
x2
066522-900
066522-900
066551-950
066551-950
MAX = 113 kg =
+
1
100102-900
THIS PLATFORM IS
NOT INSULATED.
DIESE ARBEITSBÜHNE
IST NICHT ISOLIERT.
CETTE PLATEFORME
N'EST PAS ISOLEE.
501453-000
501453-000
x4
502480-000
014222-903
014222-903
x4
503721-000
CUTOUT
CUTOUT
CUTOUT
CUTOUT
503723-000
503723-000
504199-007
Sec6:27
MAX = 340 kg
MAX = 340 kg
+
1
+
3
504199-007
7 m/s
Summary of Contents for X26N
Page 1: ...POWERED ACCESS WORK PLATFORM X26N SERVICE PARTS MANUAL 508244 005 sn 5119 Feb10 ...
Page 2: ......
Page 4: ......
Page 30: ...Page 2 20 11 SPECIFICATIONS ...
Page 49: ...Section 3 Service Repair 508244 002 Page3 19 ...
Page 52: ...Section 3 Service Repair Page 3 22 508244 002 ...
Page 60: ...Page 4 8 4 7 Hydraulic Notes ...
Page 62: ...Page 5 2 Schematics 508244 002 5 2 ELECTRIC Hydraulic Schematic ...
Page 63: ...Page 5 3 Schematics 508244 002 5 3 CABLE ASSEMBLY ...
Page 64: ...Page 5 4 Schematics 508244 002 5 4 J1 CABLE SCHEMATIC ...
Page 65: ...Page 5 5 Schematics 508244 002 5 5 OVERLOAD SCHEMATIC ...
Page 67: ...Page 5 7 Schematics 508244 002 ...
Page 68: ......
Page 71: ...Sec6 3 ...
Page 75: ...Sec6 7 ...
Page 77: ...Sec6 9 41 39 38 38 38 42 32 32 39 40 8 38 ...
Page 78: ...Sec6 10 3 4 8 7 9 10 11 12 13 11 14 1 15 16 ...
Page 88: ...Sec6 20 ...
Page 90: ...Sec6 22 ...
Page 93: ...Sec6 25 ...
Page 98: ...Sec6 30 ...
Page 99: ......