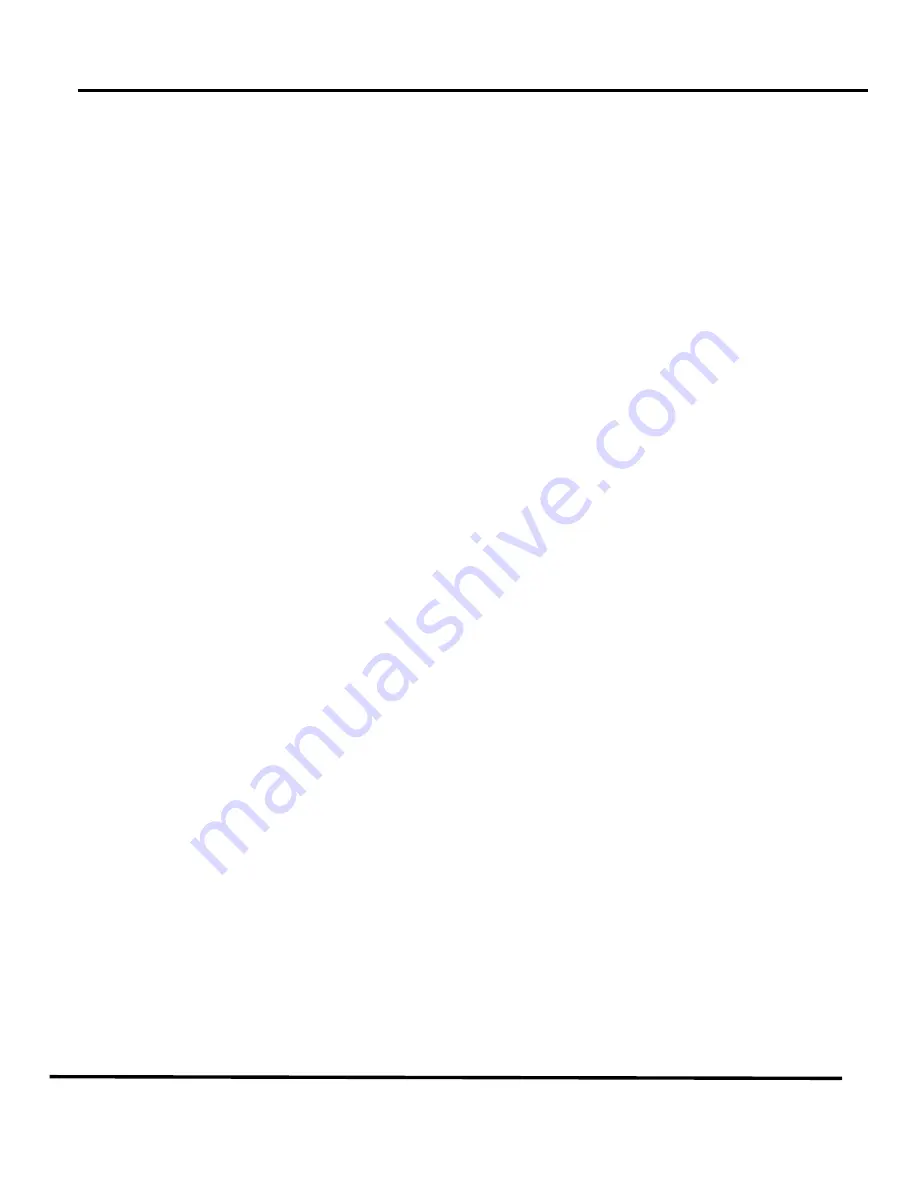
CHAPTER 3: OPERATING INSTRUCTIONS
MICROPULL
®
IV WIRE BOND PULL TESTER
990-180
3-7
signaling that the hook should be lowered. However, the hook will remain under the wire applying 2 gf
until the Control Lever is lowered.
5 Lower the hook and press the footswitch to signal the start of a new test.
6 Repeat this test with the MODE switch set to NON-DESTRUCT, the HOOK RETURN switch set to
AUTO, and the ZERO switch (on the rear panel) pushed in (AUTO). Note that the hook automatically
returns to the Downstop as soon as the actual force equals or exceeds the PRESET FORCE. With the
PULL RATE control (on the rear panel) set to MAX, you are applying the force at the maximum rate
which is 50% of the full scale force per second. Any overshoot is a result of inertia and can usually be
eliminated by adjusting the PULL RATE control CW (toward MIN).
7 When switching the ZERO switch from MANUAL to AUTO, it is considered good practice to reset by
pressing the FT SW ENABLE switch followed by the footswitch. The purpose of this procedure is to
insure that the tare is subtracted from the ensuing test result.
8 Turn the HOLD TIME control (on the rear panel) to its maximum (fully CW) position and repeat the
previous test. The PRESET FORCE will now be applied to the wire bond for 3 seconds before the hook
is automatically lowered to the Downstop. This feature is useful in performing peel tests. The setting of
the HOLD TIME control has no meaning when the HOOK RETURN switch is set to MANUAL.
9 Repeat the previous test. While the hook is applying force to the wire bond, hit the table with your fist.
This will give you some indication of the force that can be transmitted to the wire bond as a result of
excessive shock transmitted to the wire bond through the table. Notice that this excessive force is
recorded by the MP4 as required by the MIL-STD.
10 Set the MODE switch to NON-DESTRUCT and the HOOK RETURN switch to MANUAL. On the
rear panel, set the UNITS switch to the N position (out). Notice the position of the decimal point in the
PEAK FORCE display changes. Both the reading and the Preset Force are now in millinewtons
(newtons for the 1000 gf beam). One newton, in the MP4 is 101.97 grams force. In this mode, all
forces will be applied and displayed in terms of millinewtons.
11 Repeat the test with the PRESET FORCE set to 000. Notice that the MP4 does not operate.
NOTE:
Setting the PRESET FORCE to 000 has no meaning and therefore further operation of the MP4 is
inhibited when the MODE switch is set to NON-DESTRUCT.
12 Set the PRESET FORCE to 020 (200 on the 1000 gf beam).
13 With the Control Lever in the up position, turn the UPSTOP control CCW until the red Test Status
Indicator just blinks. The Upstop is now set to the position that corresponds to the highest position of
the beam arm as determined by the beam travel adjustment. This should be between 1/4-inch and 3/4-
inch above the device substrate. Record the setting.
14 Repeat the pull test with the UPSTOP control set at 000. The red Test Status Indicator should blink
continuously and the footswitch will appear to be inoperative.
NOTE:
Setting the Upstop below the Downstop inhibits operation in both the Non-Destruct and Destruct
Modes.
Summary of Contents for 6-099-04
Page 8: ......
Page 28: ......
Page 58: ......
Page 59: ......
Page 60: ......
Page 61: ......
Page 62: ......
Page 63: ......
Page 64: ......
Page 65: ......
Page 66: ......
Page 70: ......
Page 71: ......
Page 72: ......
Page 73: ......
Page 74: ......
Page 75: ......
Page 76: ......
Page 77: ......
Page 78: ......
Page 79: ......
Page 80: ......
Page 81: ......
Page 82: ......
Page 84: ......