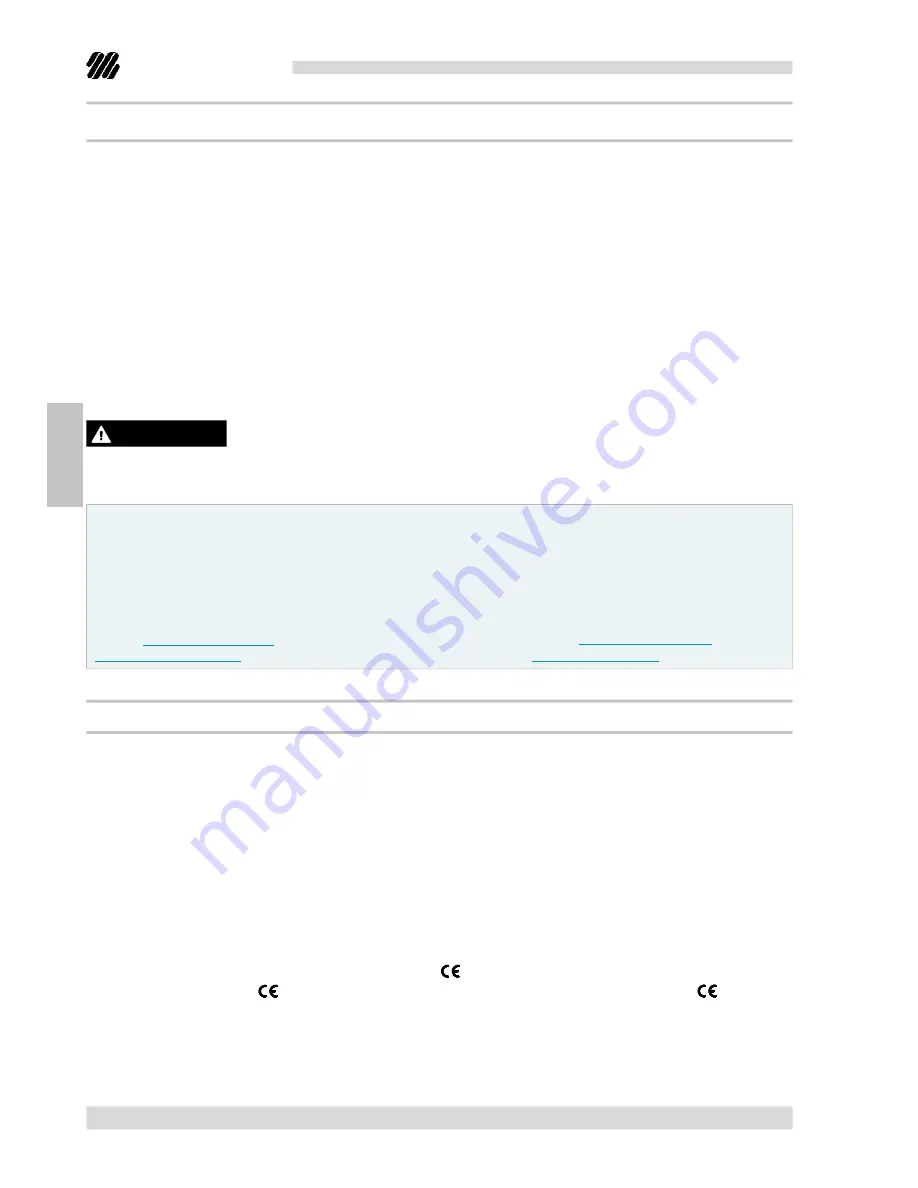
Owner's manual
ULTRAFLEX
page 6
of 36-
POWER A MK2
E
NG
L
ISH
WARRANTY
TECHNICAL ASSISTANCE SERVICE
INFORMATIVE LETTER
UFLEX S.r.l.
Via Milite Ignoto,8A
16012 Busalla (GE)-Italy
Ph.: +39.010.962.0239 (Italy)
Ph.: +39.010.962.0244 (abroad)
Fax: +39.010.962.0333
Email: [email protected]
www.ultraflexgroup.it
North - South - Central America:
UFLEX
USA
6442 Parkland Drive
Sarasota, FL 34243
Ph.: +1.941.351.2628
Fax: +1.941.360.9171
Email: [email protected]
www.uflexusa.com
This installation and maintenance manual is an integrant part of the product and should be easily available
to staff in charge of use and maintenance.
The user must know the content of this manual.
ULTRAFLEX
declines all responsibility for possible mistakes in this manual due to printing errors.
Although the main features of the type of product described are not subject to change,
ULTRAFLEX
Company
reserves the right to modify any parts, details and accessories it deems necessary to improve the product
or for manufacturing or commercial requirements, at any time and without being obliged to update this
manual immediately.
ALL RIGHTS ARE RESERVED. Publishing rights, trademarks, part numbers and photographs of
ULTRAFLEX
products contained in this manual are
ULTRAFLEX
property. Great care has been taken in collecting and
checking the documentation contained in this manual to make it as complete and comprehensible as
possible. Nothing contained in this manual can be interpreted as warranty either expressed or implied -
including, not in a restricted way, the suitability warranty for any special purpose. Nothing contained in this
manual can be interpreted as a modification or confirmation of the terms of any purchase contract.
To ensure the correct product and component working, the product must be installed by qualified staff.
In the event of part damage or malfunction, please contact the qualified staff or our Technical Assistance
Service.
WARNING
ULTRAFLEX
guarantees that its products are well designed and free from manufacturing and material defects,
for a period of two years from the date of manufacturing.
For the products which are installed and used on working or commercial boats the warranty is limited to
one year from the date of manufacturing.
If during this period the product proves to be defective due to improper materials and/or manufacture, the
manufacturer will repair or replace the defective parts free of charge.
Direct or indirect damage is not covered by this warranty. In particular the company is not responsible and this
warranty will not cover the damage resulting from incorrect installation or use of the product (except for
replacement or repair of defective parts according to the conditions and terms above).
This warranty does not cover the products installed on race boats or boats used in competitions.
The descriptions and illustrations contained in this manual should be used as general reference only.
For any further information please contact our Technical Assistance Service.
ULTRAFLEX
steering system components are marked according to the Directive 2013/53/EU.
We remind you that only
marked steering systems must be used on the boats marked
.