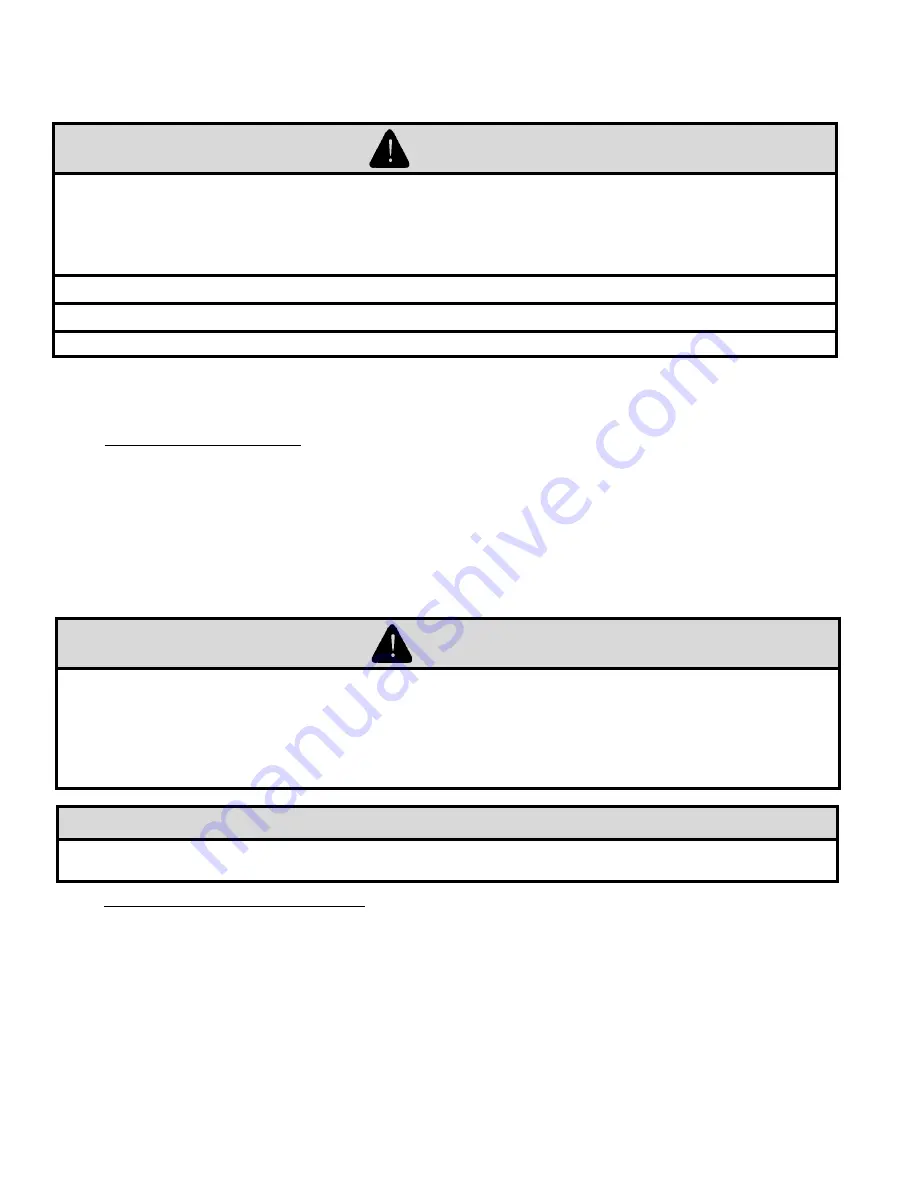
64
107672-01 - 7/17
VII. Venting
I. Assembly of Stainless Steel Vent Systems
1.
This boiler has been listed for use with Duravent FasNSeal Flex Stainless Steel vent systems to be provided by the in-
staller.
Warning
Asphyxiation Hazard. Follow these instructions and the installation instructions included by the original
stainless steel venting component manufacturer DuraVent. Failure to do so could cause products of
combustion to enter the building, resulting in severe property damage, personal injury or death. Where a
conflict arises between DuraVent or instruction and these instructions, the more restrictive instructions
shall govern.
Do not mix vent components from listed manufacturers.
Examine all components from listed manufacturers.
All condensate that forms in the vent must be able to drain back to the boiler.
2.
The vent adaptor has three different inside diameters. The smaller, lower diameter accepts 3” Stainless steel (Figure 7.27).
A locking band clamp in the adaptor prevents the vent pipe from coming out of the adaptor once it is installed and tight-
ened. Lubricate the upper gaskets in the vent adaptor with water and insert the first piece of 3” stainless into the adaptor
until it bottoms out. Tighten locking band clamp to secure vent pipe.
3.
Installation of Air Intake System - Start assembly of the PVC air intake system at the boiler. Assembly of the air intake
system is done in the same manner as the vent system except as follows:
a. Drill a 7/32” clearance hole into the front side of the air intake ada
ptor. Insert the first piece of PVC air intake
pipe into the air intake connection and drill a 1/8” tap hole into the PVC which lines up with the 7/32” clearance
hole and secure them together with a #10 x 1” sheet metal screw. Seal the joint between the intake pipe and the
adaptor with RTV.
b. All intake piping may be PVC.
c. There is a 0” minimum clearance between the air intake piping and all types of construction.
d. To the extent possible, pitch horizontal air intake piping towards the outside.
Warning
Asphyxiation Hazard. Vent systems made by Duravent rely on gaskets for proper sealing. When these vents
systems are used, take the following precautions:
• Make sure that gasket is in position and undamaged in the female end of the pipe
• Make sure that both male and female pipes are free of damage prior to assembly.
• Only cut vent pipe as permitted by the vent manufacturer in accordance with their instructions.
When pipe is cut, the cut end must be square and carefully de-burred prior to assembly.
4.
Installation using DuraVent FasNSeal Flex (Option 39)
Refer to manufacturer’s instructions for assembly of all flex components including the chimney cap and adaptor to rigid
pipe at base of masonry chimney. In addition, observe the following requirements:
a. Refer to the appropriate Vent option in table 7.21
for a list of the principle flex components required. Rigid
vent pipe by the same manufacturer will also be required for the run from the boiler to the base of chimney.
b. Masonry chimneys cannot be used for an air chase.
c. Flexible stainless steel vent shall be installed in an UNUSED masonry chimney and supplying combustion air through a
separate wall or roof combustion air terminal. The unused chimney flue must be structurally sound and in good repair. A
chimney is considered UNUSED when it is not being used for any appliance venting. If chimney is a multiple flue type
where one of the multiple flues is being used for an appliance venting, the flexible stainless vent installation is permitted
through an adjacent, unused flue providing a local authority having jurisdiction approves such installation. (Figure 7.25b)
nOTiCE
The venting system must be free to expand and contract and supported in accordance with the
installation instructions included by the original stainless steel venting component manufacturer.
Summary of Contents for K2WT-080B
Page 83: ...83 107672 01 7 17 PAGE LEFT INTENTIONALLY BLANK...
Page 89: ...89 107672 01 7 17 X Wiring continued Figure 10 5 Internal Ladder Diagram...
Page 90: ...90 107672 01 7 17 X Wiring continued...
Page 91: ...91 107672 01 7 17 Figure 10 6 Internal Wiring Connections Diagram X Wiring continued...
Page 102: ...102 107672 01 7 17 Lighting and Operating Instructions XI Start Up and Checkout continued...
Page 147: ...147 107672 01 7 17 XV Service Parts continued...
Page 151: ...151 107672 01 7 17 XV Service Parts continued...
Page 153: ...153 107672 01 7 17 XV Service Parts continued 85 86 91 95...
Page 162: ...162 107672 01 7 17...
Page 163: ...163 107672 01 7 17...
Page 164: ...164 107672 01 7 17...
Page 165: ...165 107672 01 7 17...
Page 166: ...166 107672 01 7 17...
Page 167: ...167 107672 01 7 17...