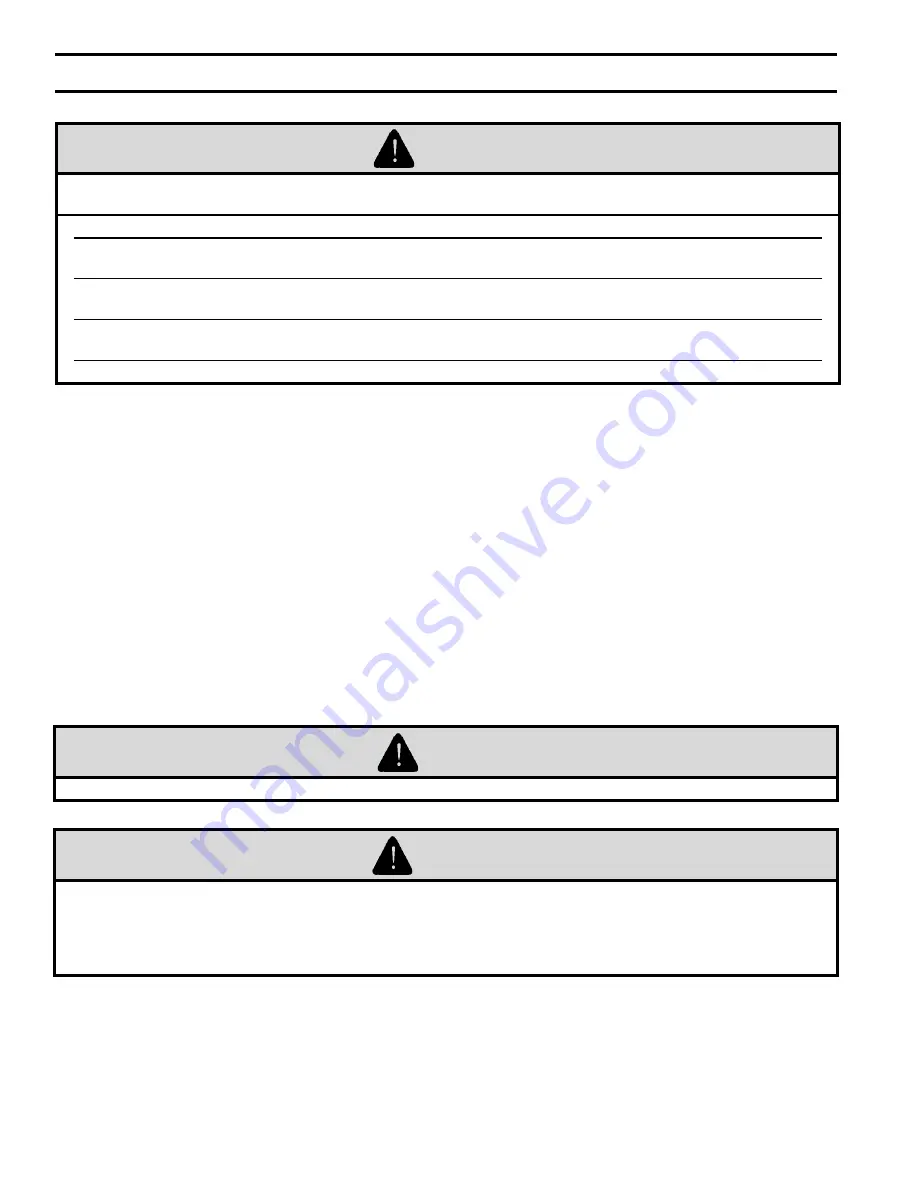
68
107672-01 - 7/17
Gas piping to the boiler must be sized to deliver adequate gas for the boiler to fire at the nameplate input at an inlet
pressure between the minimum and maximum values shown in Table 8.2. When sizing, also consider other existing
and expected future gas utilization equipment (i.e. water heater, cooking equipment). For more information on gas line
sizing, consult the utility or the
National Fuel Gas Code,
NFPA54/ANSI Z223.1, and/or CAN/CSA B149.1
Natural
Gas and Propane Installation Code.
Figure 8.1 shows typical gas piping connection to the boiler. A sediment trap must be installed upstream of all gas
controls. Install the factory provided manual shut-off valve outside the jacket with a ground joint union as shown.
All above ground gas piping upstream from manual shut-off valve must be electrically continuous and bonded to a
grounding electrode. Refer to
National Electrical Code,
NFPA 70.
The boiler and its gas connection must be leak tested before placing the boiler in operation. When doing this, the boiler
and its individual shut-off must be disconnected from the rest of the system during any pressure testing of that system
at pressures in excess of 1/2 psi (3.5kPa). When pressure testing the gas system at pressures of 1/2 psi (3.5kPa) or less,
isolate the boiler from the gas supply system by closing its individual manual shut-off valve. Locate leaks using an
appropriate combustible gas non-corrosive leak detector solution.
VIII. Gas Piping
Warning
Explosion Hazard. Failure to properly pipe gas supply to boiler may result in improper operation or leaks of
flammable gas.
Gas supply to boiler and system must be absolutely shut off prior to installing or servicing boiler gas piping.
Always assure gas piping is absolutely leak free and of the proper size and type for the connected
load.
Use a thread compound compatible with liquefied petroleum gas. Failure to use proper thread
compounds on all gas connectors may result in leaks of flammable gas.
If inlet pressure is above 1/2 psig (3.4 kPa) an additional gas pressure regulator is required. Consult
gas supplier.
Size corrugated stainless steel tubing (CSST) to ensure proper capacity and minimize flow restrictions.
DANGER
Explosion Hazard. Do not use matches, candles, open flames or other ignition source to check for leaks.
Warning
If gas pressure in the building is above ½ psig (3.4 kPa), an additional gas pressure regulator is required.
Using one additional regulator for multiple gas appliances may result in unsafe boiler operation. The
additional regulator must be able to properly regulate gas pressure at the input of the smallest appliance.
If the regulator can not do this, two or more additional regulators are required. Consult regulator
manufacturer and/or local gas supplier for instructions and equipment ratings.
Summary of Contents for K2WT-080B
Page 83: ...83 107672 01 7 17 PAGE LEFT INTENTIONALLY BLANK...
Page 89: ...89 107672 01 7 17 X Wiring continued Figure 10 5 Internal Ladder Diagram...
Page 90: ...90 107672 01 7 17 X Wiring continued...
Page 91: ...91 107672 01 7 17 Figure 10 6 Internal Wiring Connections Diagram X Wiring continued...
Page 102: ...102 107672 01 7 17 Lighting and Operating Instructions XI Start Up and Checkout continued...
Page 147: ...147 107672 01 7 17 XV Service Parts continued...
Page 151: ...151 107672 01 7 17 XV Service Parts continued...
Page 153: ...153 107672 01 7 17 XV Service Parts continued 85 86 91 95...
Page 162: ...162 107672 01 7 17...
Page 163: ...163 107672 01 7 17...
Page 164: ...164 107672 01 7 17...
Page 165: ...165 107672 01 7 17...
Page 166: ...166 107672 01 7 17...
Page 167: ...167 107672 01 7 17...