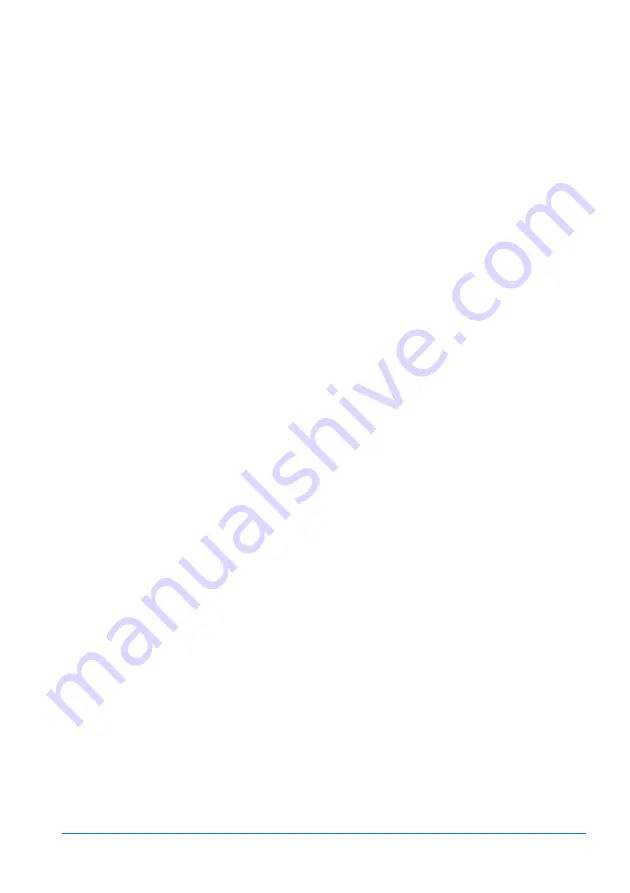
8
valve. Align the rubber seal, metal valve, and over extension stop accurately
over one another and 0.25mm from the edge. Tighten the screw and confirm
their position.
OBSERVE HEALTH AND SAFETY PRECAUTIONS WHEN HANDLING
CHEMICALS.
Remove the
piston assembly
, complete with
spring
and
spring seat
. Clean out
the inside of the compressor body by blowing with compressed air.
If the piston can not be removed then the compressor may be out of
alignment. The compressor should be replaced with a new item, or removed
from the controller and returned to the Kendall Service Center for a
compressor exchange, alternatively the complete controller can be returned
to Kendall for repair.
Compressor disassembly if it is out of alignment
With access to a
compressor alignment tool
the compressor may be re-
aligned on site.
Remove the compressor from the controller (see Section 4.6).
Undo the two screws holding the rear cover to the compressor body and
lift the cover off the wiring grommet.
Slacken the two screws holding the
rear cylinder housing
to the compressor
body and carefully withdraw the piston assembly, complete with spring and
spring seat.
Remove the two screws holding the rear cylinder housing to the
compressor body, separate the parts and work the housing out from
between the coils.
Inspect the
rear cylinder housing bearing insert
for wear. The insert must
be hemispherical in shape. If the insert is worn, remove the old bearing
and press in a replacement. If the rear bearing is serviceable wipe off all
grease residue with an Isopropyl Alcohol (IPA) swab.
Remove the laminations and coils from the compressor body.
Compressor re-alignment
Clean off all residual adhesive from the rear cylinder housing,
laminations and compressor body. Blow all compressor parts and the
compressor body with low pressure compressed air
Stand the compressor alignment tool upright on a flat surface, with the
small diameter upwards.
Place the compressor body over the alignment tool with the rear end
uppermost and the feet toward you, ensuring that it locates correctly in
the front cylinder housing recess.
Apply Loctite 454 (or 410) evenly around the lamination mating surface
Summary of Contents for KENDALL 6060 Novamedix A-V Impulse System
Page 1: ...SERVICE MANUAL MODEL 6060...