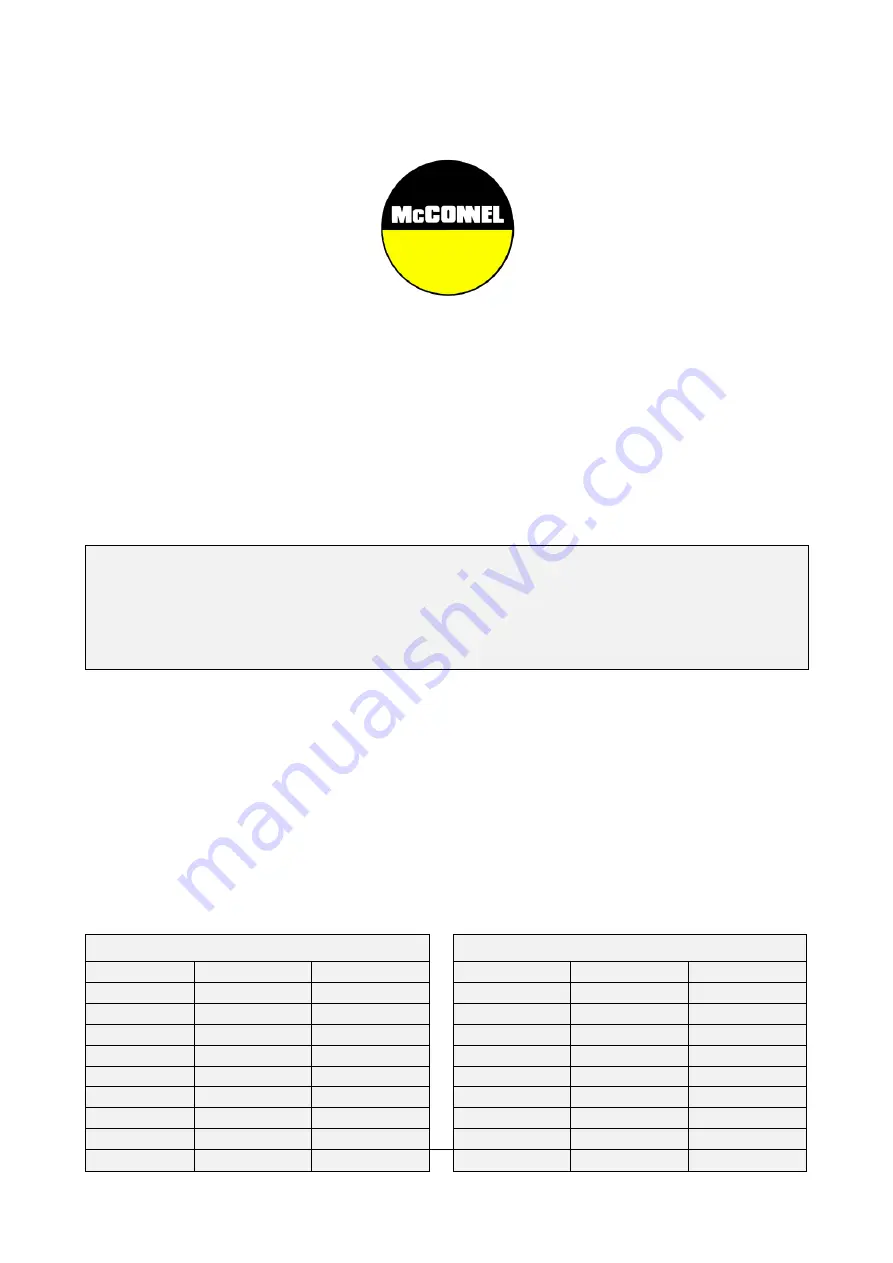
IMPORTANT
VERIFICATION OF WARRANTY REGISTRATION
DEALER WARRANTY INFORMATION & REGISTRATION VERIFICATION
It is imperative that the selling dealer registers this machine with McConnel Limited before
delivery to the end user
– failure to do so may affect the validity of the machine warranty.
To register machines go to the McConnel Limited web site at
www.mcconnel.com
, log
on
to ‘
Dealer Inside
’ and select the ‘
Machine Registration button
’
which can be found in
the Service Section of the site. Confirm to the customer that the machine has been
registered in the section below.
Should you experience any problems registering a machine in this manner please contact
the McConnel Service Department on 01584 875848.
Registration Verification
Dealer Name:
……………………..…………………………………………………………….
Dealer Address:
…….………………………………………………………………………….
Customer Name:
……………………..…………………………………………………………
Date of Warranty Registration:
……/……/...…… Dealer Signature: ………………..……
NOTE TO CUSTOMER / OWNER
Please ensure that the above section above has been completed and signed by the selling
dealer to verify that your machine has been registered with McConnel Limited.
IMPORTANT: During the initial ‘bedding in’ period of a new machine it is the customer’s responsibility
to regularly inspect all nuts, bolts and hose connections for tightness and re-tighten if required. New
hydraulic connections occasionally weep small amounts of oil as the seals and joints settle in – where
this occurs it can be cured by re-tightening the connection – refer to torque settings chart below. The
tasks stated above should be performed on an hourly basis during the first day of work and at least
daily thereafter as part of the machines general maintenance procedure.
CAUTION: DO NOT OVER TORQUE HYDRAULIC FITTINGS AND HOSES
TORQUE SETTINGS FOR HYDRAULIC FITTINGS
HYDRAULIC HOSE ENDS
PORT ADAPTORS WITH BONDED SEALS
BSP
Setting
Metric
BSP
Setting
Metric
1/4”
18 Nm
19 mm
1/4”
34 Nm
19 mm
3/8”
31 Nm
22 mm
3/8”
47 Nm
22 mm
1/2”
49 Nm
27 mm
1/2”
102 Nm
27 mm
5/8”
60 Nm
30 mm
5/8”
122 Nm
30 mm
3/4”
80 Nm
32 mm
3/4”
149 Nm
32 mm
1”
125 Nm
41 mm
1”
203 Nm
41 mm
1.1/4”
190 Nm
50 mm
1.1/4”
305 Nm
50 mm
1.1/2”
250 Nm
55 mm
1.1/2”
305 Nm
55 mm
2”
420 Nm
70 mm
2”
400 Nm
70 mm
Summary of Contents for MAXICUT 280
Page 1: ...MAXICUT 280 Rotary Topper Operator Manual Publication 986 September 2020...
Page 3: ......
Page 9: ......
Page 14: ......
Page 17: ......
Page 53: ...36 FOR NOTES...