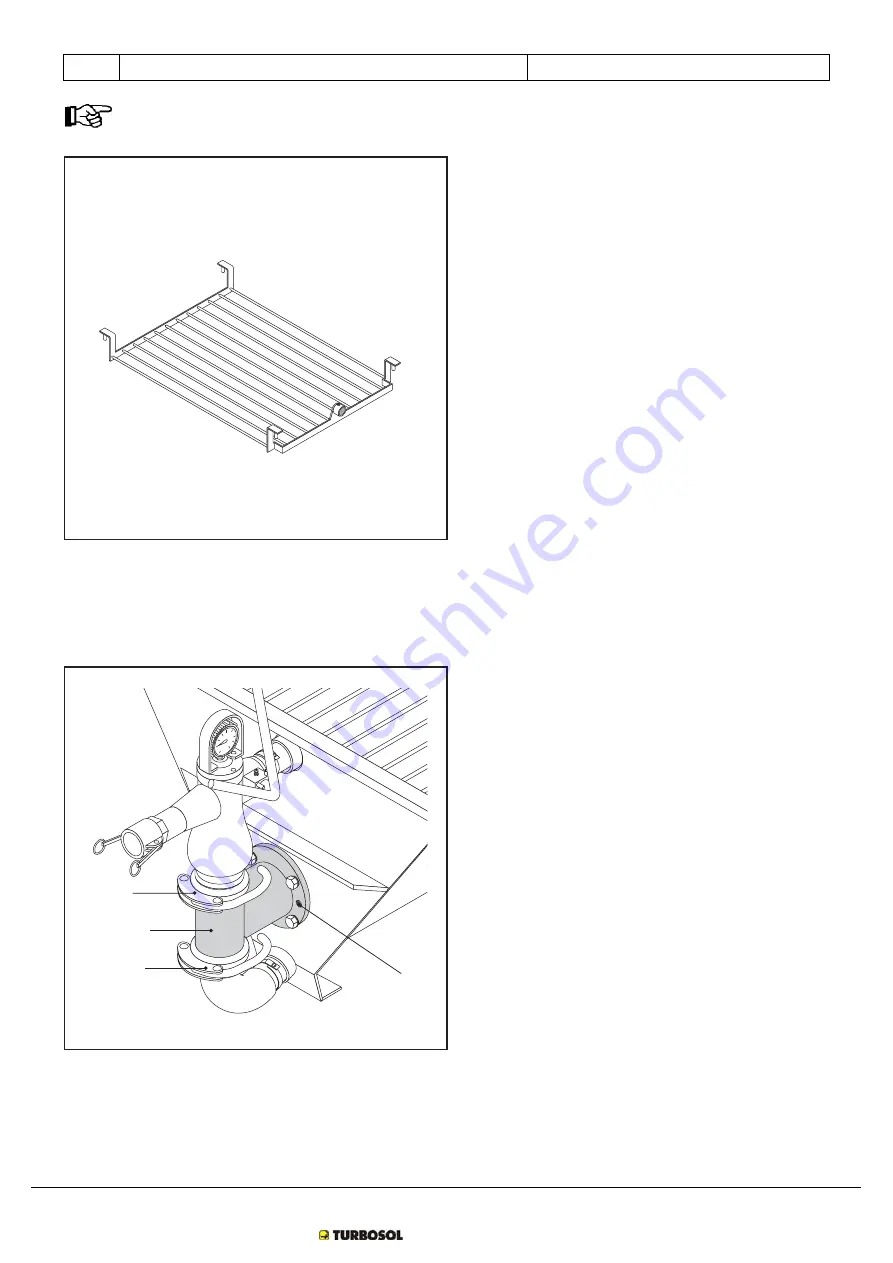
EN
MINI AVANT
IS11/11 - 561185
7 - USE AND OPERATION
7
-
Pag. 2/10
THIS MANUAL IS PROPERTY OF
-
ANY TOTAL OR PARTIAL REPRODUCTION IS STRICTLY FORBIDDEN
Cap.
To use the ready-mixed product kit the vibrating sieve must be replaced with the protection grill (FIG.21).
FIG.21
- Replace the intake valve body (optional):
• Release the two joints (FIG.22-REF.1).
• Loosen the 4 screw fasteners at the hopper and replace the valve body: to ease replacement, tighten two screws into
the additional threaded holes (FIG.22-REF.2).
• Mount the dedicated valve body (FIG.22-REF.3).
2
1
1
3
FIG.22
- Replace the rubber ball valves with the steel ball valves in the kit (FIG.23-REF.1).
- Replace the supplied valve seats with those for the kit (FIG.23-REF.2/3).