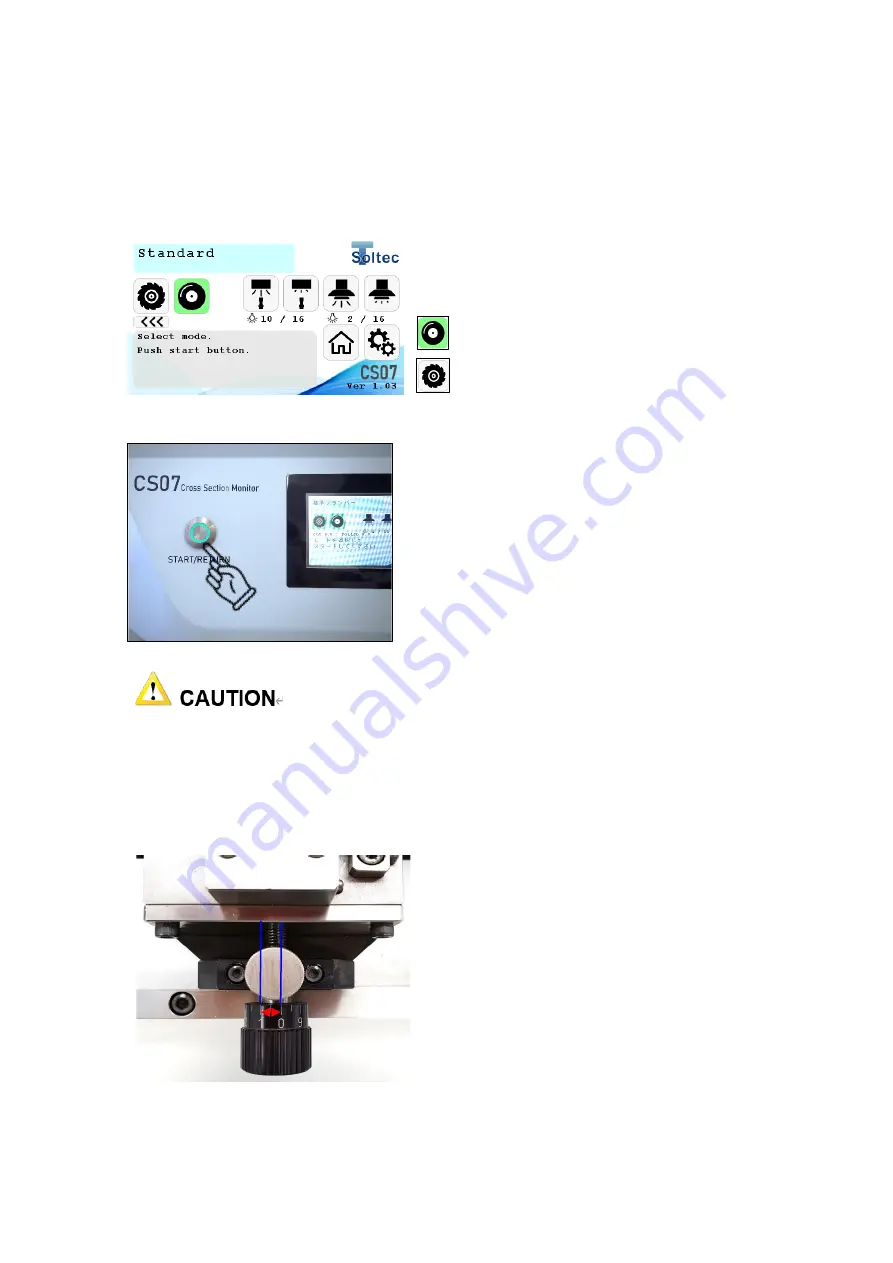
15
4.4 GRINDING THE TERMINALS
The following procedures describe the grinding operation, applied when only the grinding
mode is activated.
1. Place the clamp on the tranfer unit. Close the
safety cover.
On operation screen, only activate the grinding
mode.
: Activated
: Deactivated
Touch the buttons to activate/ deactivate them.
Press
START
button
→ CS07 will move the terminal to the right and
grind the terminal surface.
When it is complete, the transfer unit will
automatically return to its home position.
※
While grinding the terminal, if you want the
transfer unit to return to its home position
immediately, press
START
button.
● Do not grind the terminal if it has not been cut yet. It may cause serious damage to the
device.
● When grinding the sample surface again, only move the clamp to the front
0.2mm or
less each time
.
Moving the terminal more than 0.2mm upward each time may cause damage to the device.
Each step = 0.1mm
e.g: 0~1 = + 0.1mm
0~2 = + 0.2mm
0~3 = + 0.3mm