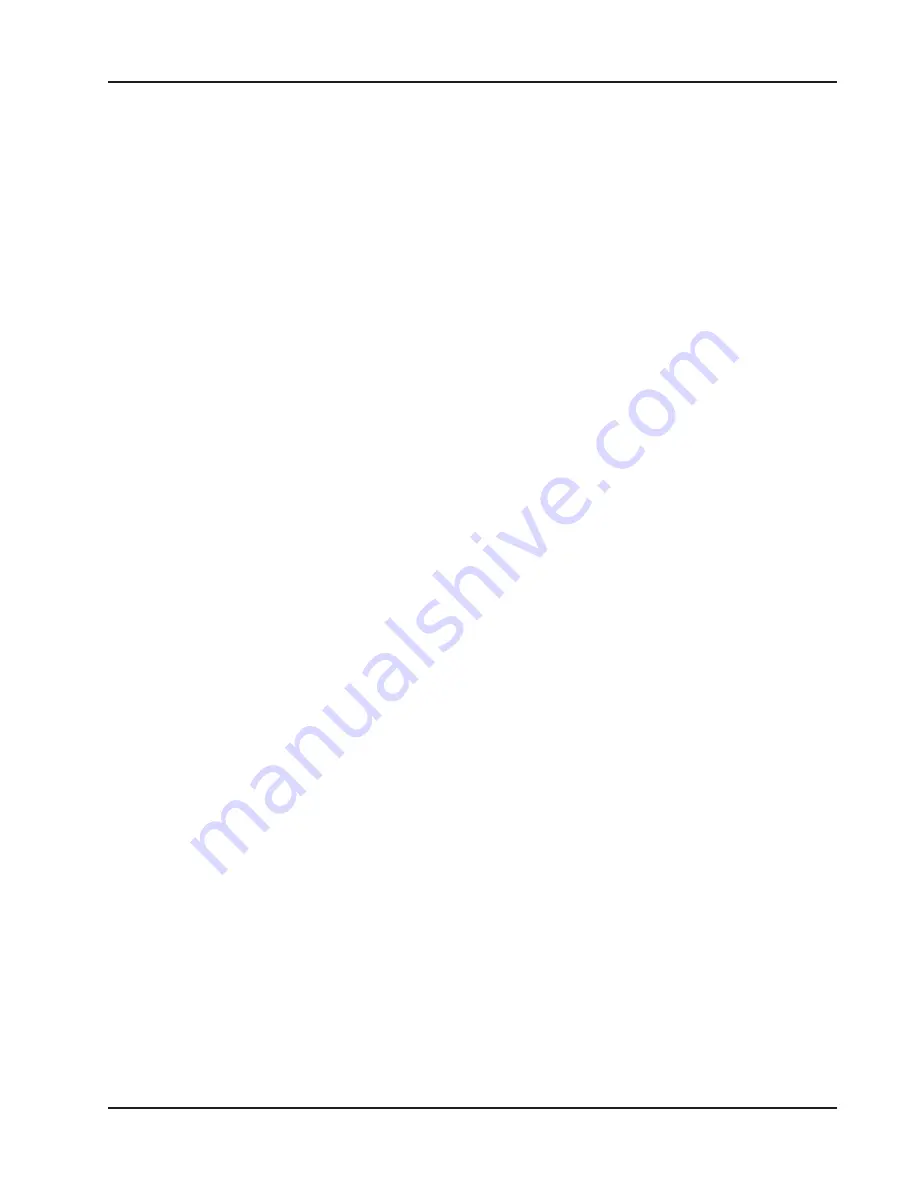
5
Model PFM 1632 PIPEMASTER®
92-1456 Rev. 180531
2.5 AREA EQUIPMENT
•
Secure the pipe with clamps, vises, chains or straps.
•
Ensure that both sides of the pipe at the cut site is fully supported so that the
pipe will not move after the cut is completed. Long lengths of pipe may be
under load and the separation of the pipe can release pressure. This pressure
can cause both sides of the pipe to move.
2.6 TOOL CARE
•
Keep tools in good operating condition. Sharp tool bits perform better and are
safer than dull tool bits.
•
Do not use damaged tools. Always check your tools for damage especially if a
tool has malfunctioned, been dropped or hit, check it for damage.
•
Before you start operating the equipment, do no-load tests and feed function
checks.
Summary of Contents for 180531
Page 1: ...Operation Manual 92 1456 Rev 180531 Model PFM 1632 PIPEMASTER ...
Page 14: ...This Page is Intentionally Left Blank ...
Page 58: ...56 TRI TOOL INC 92 1456 Rev 180531 MODEL PFM 1632 P N 01 1929 75 76 H Hose Locations VIEW H ...
Page 64: ...This Page is Intentionally Left Blank ...
Page 72: ...70 TRI TOOL INC 92 1456 Rev 180531 VALVE ASSEMBLY P N 07 0075 1 2 3 4 5 6 7 8 9 10 11 12 11 ...