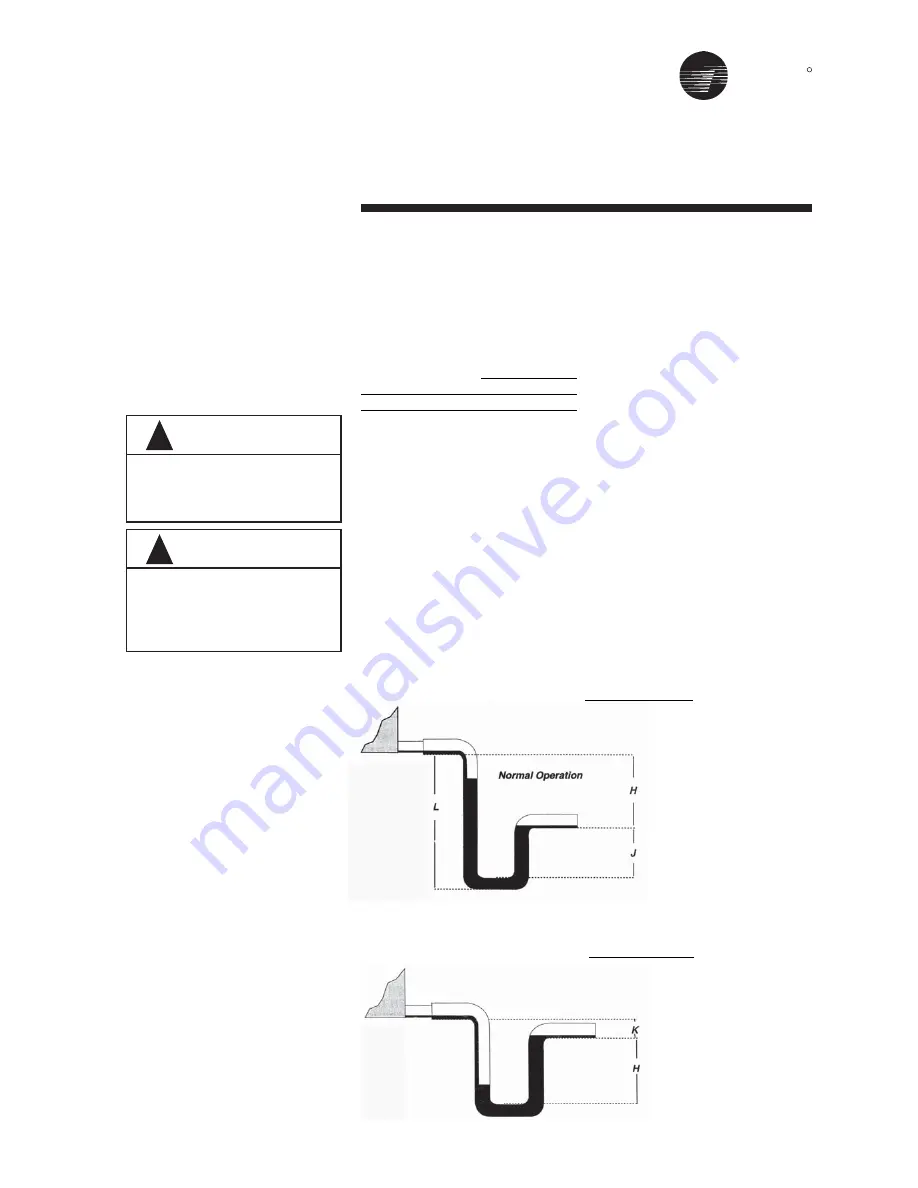
TRANE
R
19
Assembly & Installation
Piping - Condensate Drain
Pan Connections
On cooling section(s) the drain pan
should always be connected directly
to a trap to ensure proper drainage of
condensate.
Male-threaded, 1-1/2" BSPT conden-
sate drain connection is provided on
one side of the coil section. The main
drain lines and trap must be the same
size as the drain connection.
Pitch the connection line horizontal or
downward toward an open drain and
install a plugged tee to facilitate
cleaning. Condensate lines should not
be connected to a closed drain. This
is to avoid the possibility of drawing
sewer gasses into the unit.
Drain traps must be primed. lf they
are not, the trap is essentially non-
existent and the drain pan will likely
overflow.
CAUTION
!
Units With More Than One
Drain Pan
With the Trane Quantum
TM
Air Handler,
each module can be ordered with or
without a drain pan. When more than
one module has a drain pan, you must
trap each module individually.
Connecting all drains to a common line
with only one trap will result in
condensate retention, and possible
water damage to the air handler or
adjoining space.
If a module has a drain pan for cleaning
purposes only, it does not need a trap;
however a cap or shut off valve should
be installed on the drain connection.
Only modules handling condensate,
such as a cooling coil module or
eliminator module, require a trap.
Figure 9 through Figure 10 are
examples of typical installations.
IMPORTANT
!
Figure 9
Drain Pan Trapping for module under Negative Pressure
H = (1” for each 1” of
maximum negative
pressure) + 1”
J = 1/2 H
L = H + J + Pipe di
Insulation
Figure 10
Drain Pan Trapping for module under Positive Pressure
K = min. 1/2”
H = 1/2” plus maximum
total static pressure
Failure to provide adequate
condensate piping may result in
water damage to the equipment or
building.
The applicable "rule of thumb" for
amount of condensate may as high
as 6 lbs/hr/ton for units serving areas
with high latent heat.
Summary of Contents for TRANE Quantum CLCPEuro
Page 2: ...TRANE R...
Page 6: ...TRANE R 2 CLCPXP Model Nomenclature...
Page 7: ...TRANE R CLCPEURO Model Nomenclature 3...
Page 13: ...TRANE R Assembly Installation CLCPEuro CLCPXP External connection 9...
Page 14: ...TRANE R Assembly Installation CLCPEuro Break Point 25mm Frame to Frame 10...
Page 15: ...TRANE R 11 Assembly Installation CLCPEuro Break Point 25mm Panel to Frame...
Page 16: ...TRANE R 12 Assembly Installation CLCPEuro Break Point 2 50mm Frame to Frame...
Page 17: ...TRANE R Assembly Installation CLCPEuro Break Point 2 50mm Panel to Frame 13...
Page 18: ...TRANE R Assembly Installation CLCPEuro Paneling 14...
Page 19: ...TRANE R Assembly Installation CLCP XP Break Point 15...
Page 20: ...TRANE R Assembly Installation CLCP XP Break Point 16...
Page 21: ...TRANE R 17 Assembly Installation CLCP...
Page 22: ...TRANE R Assembly Installation CLCP 18...
Page 36: ...TRANE R Maintenance 32 Figure 18 Belt Tension Measurement...
Page 39: ...TRANE R 35 Trouble Analysis Pulley and Belt...
Page 45: ...TRANE R Appendix B HDT Unit Weight CLCPXP 41...
Page 46: ...TRANE R Appendix B HDT Unit Weight CLCPXP 42...
Page 47: ...TRANE R Appendix B HDT Unit Weight CLCPXP 43...
Page 48: ...TRANE R Appendix B VDT Unit Weight CLCPXP 44...
Page 53: ...TRANE R Appendix D Filter and Quantity 49 Filter Dimension and Arrangement Final Filter HEPA...
Page 57: ...TRANE R Typical Wiring Diagram Starter Star Delta 380 420V 3Phase 4Wires ELCB Standard 53...
Page 58: ...TRANE R 54 Typical Wiring Diagram Starter Dol 380 420V 3Phase 4Wires ELCB Standard...
Page 59: ...TRANE R 55 Typical Wiring Diagram Starter Dol 380 420V 3Phase 4Wires Standard...
Page 62: ...TRANE R 58 Typical Wiring Diagram Starter Dol 380 420V 3Phase 4Wires Standard...
Page 65: ...TRANE R 61 Typical Wiring Diagram Starter Star Delta 380 420V 3Phase 4Wires Standard...
Page 68: ...TRANE R 64...
Page 70: ...TRANE R 66...
Page 71: ...TRANE R...