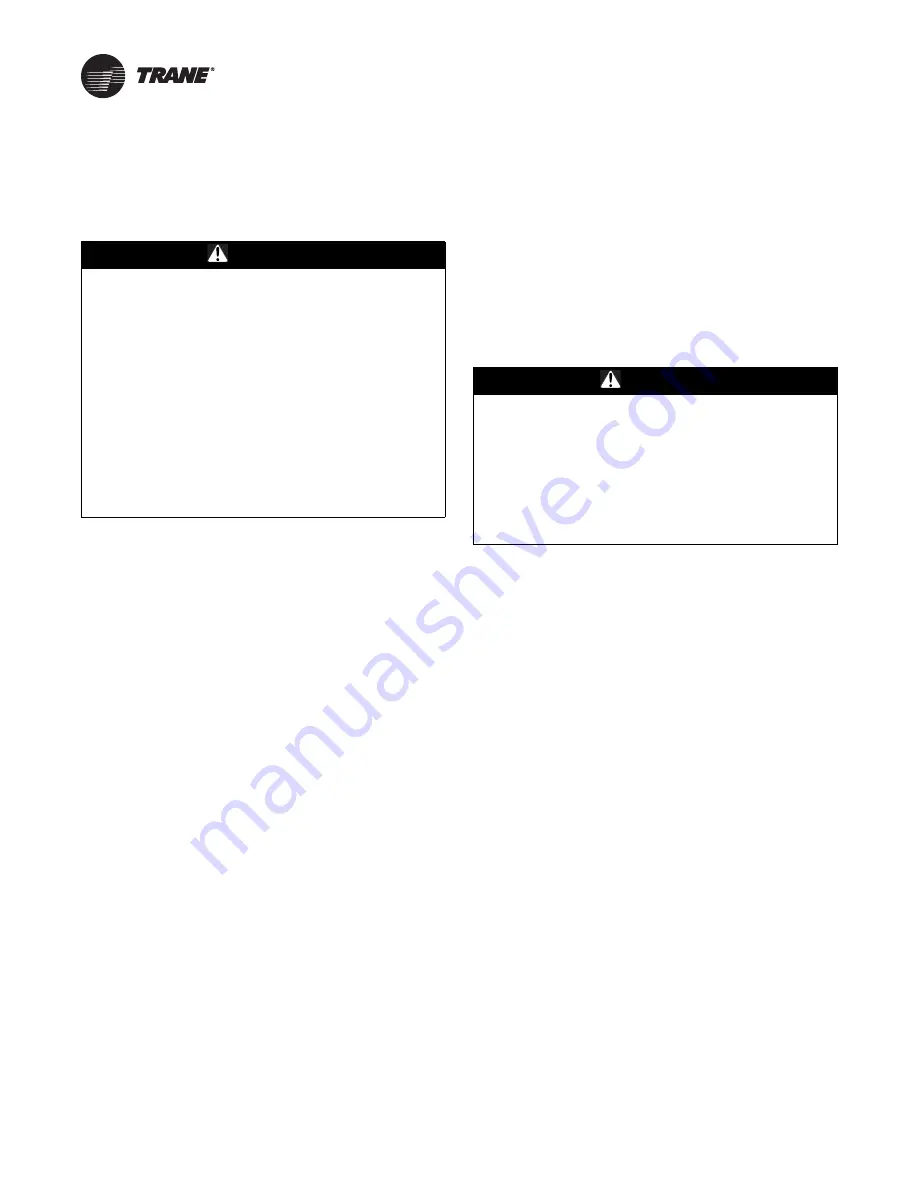
AFDK-SVU01C-EN
57
Recommended Periodic Maintenance and Inspection
Visual Inspection—Power
Removed
1.
On refrigerant-cooled drives:
Check the refrigerant
coolant lines and two-bolt flange drive connections to
ensure they are tight and do not leak.
On water-cooled drives:
Verify cooling circuit is free of
leaks and the heat exchanger system is operating
properly.
2. Ensure the door interlocks are present and working.
3. Verify the safety ground connections to the door
panels are securely connected.
4. Inspect power wire cables and devices to assure no
abrasion is occurring from vibrations against chassis
of cabinets, or other edges.
5. Ensure the drive interior and exterior is clear of any
dust or debris. Fans, circuit boards, vents etc. must be
clean. Only use a vacuum for cleaning. Do NOT use
compressed air.
6. Inspect the interior of the drive for any signs of
moisture entry or leakage.
7. Visually inspect all drive components and wiring. Look
for signs of heat or failure (look for swelled or leaking
capacitors, discolored reactors or inductors, broken
pre-charge resistors, smoke or arc trails on MOVs and
capacitors, etc.).
8. Closely inspect the motor terminal board for any signs
of leakage, arcing, etc.
9. Check ALL cable/lug/terminal connections inside the
drive enclosure. Ensure all are clean and tight, and not
rubbing against each other anywhere.
10. Check any bypass or pre-charge contactors. Confirm
the contacts are in serviceable condition and that the
contactor operates smoothly.
11. Re-seat all ribbon cable or control wire plugs to ensure
all are snug and tight.
12. Verify 2A6 filter cap assembly fuses 2F6, 2F5, and 2F4
are not swelled or leaking.
13. Check the magnetic choke for physical damage (e.g.,
cracks).
Operational Inspection—Power
Applied
1. Verify the drive cabinet cooling fans are operating.
This should be done from outside the enclosure, by
looking into the cabinet at door and cabinet vents, to
avoid electrical hazards.
Note:
The power module fan comes on with power.
Other fans cycle with drive operation.
2. Check historic fault codes using OIM connected to the
AFD.
3. Check configuration settings and confirm all proper
settings are still present in the controls.
4. Review the diagnostic history.
5. Make Chiller Service report to document all setpoints.
6. Check the UC800 or DynaView™ alarm histories for
any indications of operational problems.
Do this every 1–12 months depending on
operating environment
To properly diagnose service issues for Adaptive
Frequency™ Drives for centrifugal chillers equipped with
LF 2.0 (AFDK) starters, and Operator Interface Module
(OIM) and special cable are required. All UC800 or
DynaView™ chillers will be equipped with the OIM as
standard on the drive power module. This is for service
only and NEVER for machine operation. These items are
available from Trane with the following part numbers:
OIM (Operator Interface Module): MOD01352
Cable for OIM: CAB01034
Do as needed.
Replace any parts that show signs of physical damage.
WARNING
Hazardous Voltage w/Capacitors!
Disconnect all electric power, including remote
disconnects and discharge all motor start/run
capacitors before servicing. Follow proper lockout/
tagout procedures to ensure the power cannot be
inadvertently energized. For variable frequency drives
or other energy storing components provided by Trane
or others, refer to the appropriate manufacturer’s
literature for allowable waiting periods for discharge of
capacitors. Verify with an appropriate voltmeter that all
capacitors have discharged. Failure to disconnect
power and discharge capacitors before servicing could
result in death or serious injury.
For additional information regarding the safe discharge of
capacitors, see PROD-SVB06A-EN
WARNING
Live Electrical Components!
During installation, testing, servicing and
troubleshooting of this product, it may be necessary to
work with live electrical components. Have a qualified
licensed electrician or other individual who has been
properly trained in handling live electrical components
perform these tasks. Failure to follow all electrical
safety precautions when exposed to live electrical
components could result in death or serious injury.