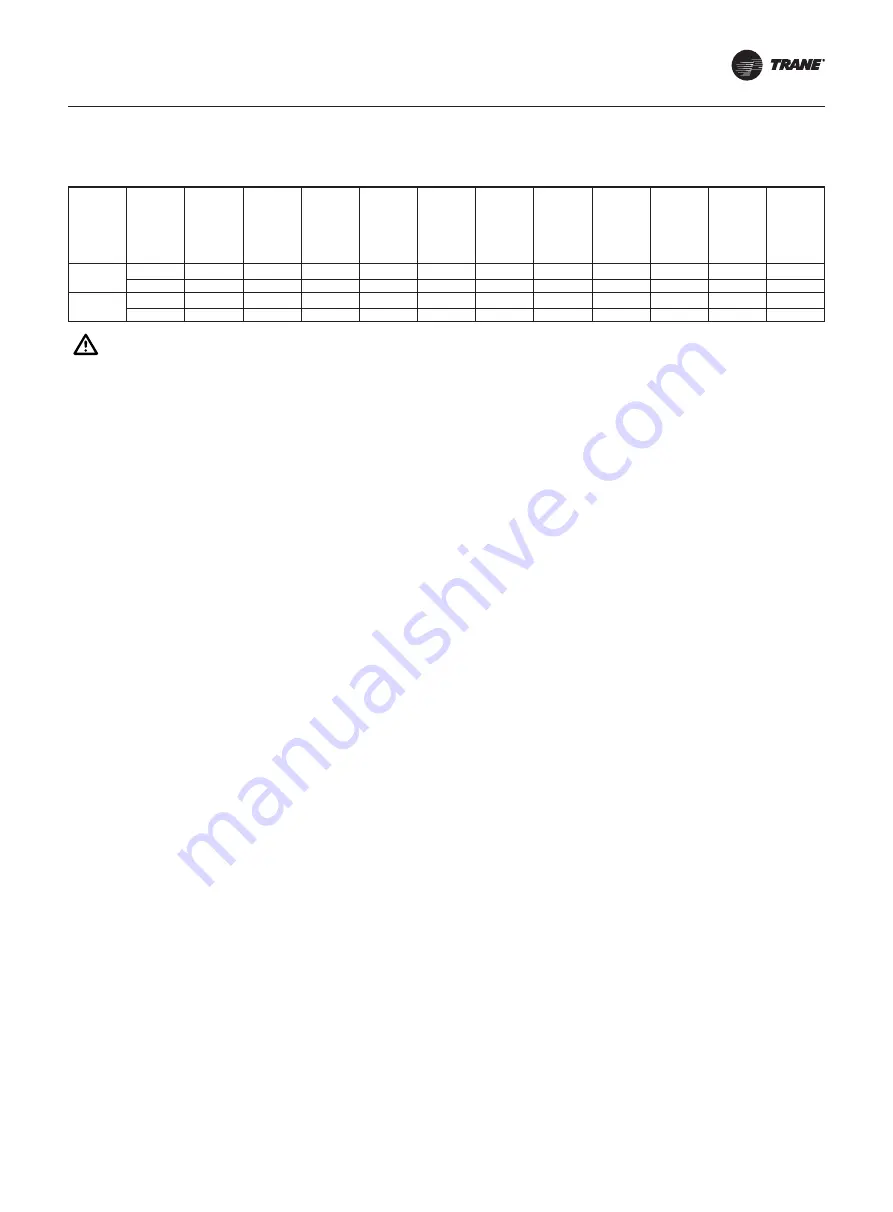
27
Electrical Installation
5-3. Electrical System Wiring
• No additional control element (such as relay) is needed inside the electric control box. It is not allowed to let the power supplies and control
lines that do not connect with the electric control box to go through the electric control box. Otherwise, the unit and control elements can break
down or being damaged due to electromagnetic interference and the protection will become invalid.
• All the cables connected with the electric control box should be supported independently instead of being supported by the electric control box.
• Usually, there is strong current lines going through the electric control box, and 220V AC current going through the control panel, therefore
the connections for strong current and weak current should be separated. The distance between power line and control line should be at least
100mm.
• Only 380V, 3N-50Hz rated power supply can be used for the unit, the maximum voltage fluctuation range is 342V-418V.
• All the electrical lines must comply with local wiring specifications. An appropriate cable should be used to connect the power terminal from
the bottom wiring hole of the electric control box. According to the standards in China, user has the responsibility to provide voltage and current
protections for the input power supply of the unit. To prevent cable from loosening, please use closed end terminals for wiring.
• All the power supplies connected to the unit must have a manual switch to make sure that the voltages on all the circuit nodes can be released
when the switch is disconnected.
• User must use cables with proper specifications to supply power to the unit. Independent power supply should be used for the unit. It is pro
hibited to share power supply with other appliances to avoid overload risks. The fuse and manual switch of the power supply should match
with the operating voltage and current of the unit. If multiple modules are connected in parallel, please refer to the figure below for the wiring
method and parameter setup of the unit.
• The internal interface of the electric control box is switching signal which needs power supply provided by user, with rated voltage of 220VAC.
User must make sure that all the provided power supplies must be equipped with circuit breaker (provided by user) to make sure that the
voltages on all the power circuit nodes can be released when the circuit breaker is disconnected.
5-4. Installation of Modular Controller
• There are four mounting holes at the back of the modular controller, which can be conveniently connected to the standard 86 box.
• A 4-core wiring terminal is arranged on the circuit board at the back of the modular controller. Seen from the back of the board, they are 485
signal B, 485 signal A, DC power supply ground (gnd) and DC power supply positive pole (+V). The DC power supply is connected with the
communication line through the terminal.
• The modular controller is provided with a 220VAC/12VDC, 500mA DC power accessory.
• Optimal operating temperature of modular controller: 0-45
℃
5-2. Electrical Specification
Please refer to the following table for the minimum current, the fuse specification and the electrical specification of motor.
The unit shall be energized for inspection before starting. If the green light is on, it will indicate that the unit is normal; if the red light is on, it
will indicate that the phases are reverse and any two phases shall be exchanged in the three-phase power supply. If the yellow light is on,
it will indicate that the power supply is lack of phase and shall be powered off for inspection. In the case of reverse phase or lack of phase,
the unit will be automatically prohibited from running or starting. The phase loss protection is only for the input power supply of the unit.
20
PKGP-SVX18B-EN
Electrical Installation
Electr
ical Specification
Please refer to the following table for the minimum current, the fuse specification and the electrical specification of
motor.
Type
Model
Power
Supply
(V/Hz/ph)
Max. current
of No.1
compressor
MOC (A)
Max. current
of No.2
compressor
MOC (A)
Max. current
of No.3
compressor
MOC (A)
Max. current
of No.4
compressor
MOC (A)
Rated
current of
No.1 fan
FLA (A)
Rated
current of
No.2 fan
FLA (A)
Max.
operating
current of unit
MOC (A)
Recommended
fuse
specification
REC(A)
Recommended
circuit breaker
specification
In (A)
Min. specification
of the power supply
copper core wire
diameter
mm
2
Standard
CX(G)AJ0655 380/50/3
24
24
2.1
2.1
55
91
69
16
CX(G)AJ1305 380/50/3
56
56
3.96
3.96
120
207
154
50
High
Efficiency
CX(G)AJ065 380/50/3
24
24
2.1
2.1
55
91
69
16
CX(G)AJ130 380/50/3
24
24
24
24
2.1
2.1
98.2
143
133
50
Notice
The unit shall be energized for inspection before starting. If the green light is on, it will indicate that the unit is
normal; if the red light is on, it will indicate that the phases are reverse and any two phases shall be exchanged in the
three-phase power supply. If the yellow light is on, it will indicate that the power supply is lack of phase and shall
be powered off for inspection. In the case of reverse phase or lack of phase, the unit will be automatically prohibited
from running or starting. The phase loss protection is only for the input power supply of the unit.
Type
Model
Power
Supply (V/
Hz/ph)
Max. current
of No.1
compressor
MOC (A)
Max. current
of No.2
compressor
MOC (A)
Max. current
of No.3
compressor
MOC (A)
Max. current
of No.4
compressor
MOC (A)
Rated
current of
No.1 fan
FLA (A)
Rated
current of
No.2 fan
FLA (A)
Max.
operating
current of
unit
MOC (A)
Recommended
fuse specifica
-
tion REC(A)
Recommended
circuit breaker
specification
In (A)
Min. specifi
-
cation of the
power supply
copper core
wire diameter
mm
2
Standard
CX(G)AJ0655
380/50/3
24
24
2.1
2.1
55
91
69
16
CX(G)AJ01305
380/50/3
56
56
3.96
3.96
120
207
154
50
High
Efficiency
CX(G)AJ065
380/50/3
24
24
2.1
2.1
55
91
69
16
CX(G)AJ0130
380/50/3
24
24
24
24
2.1
2.1
98.2
143
133
50