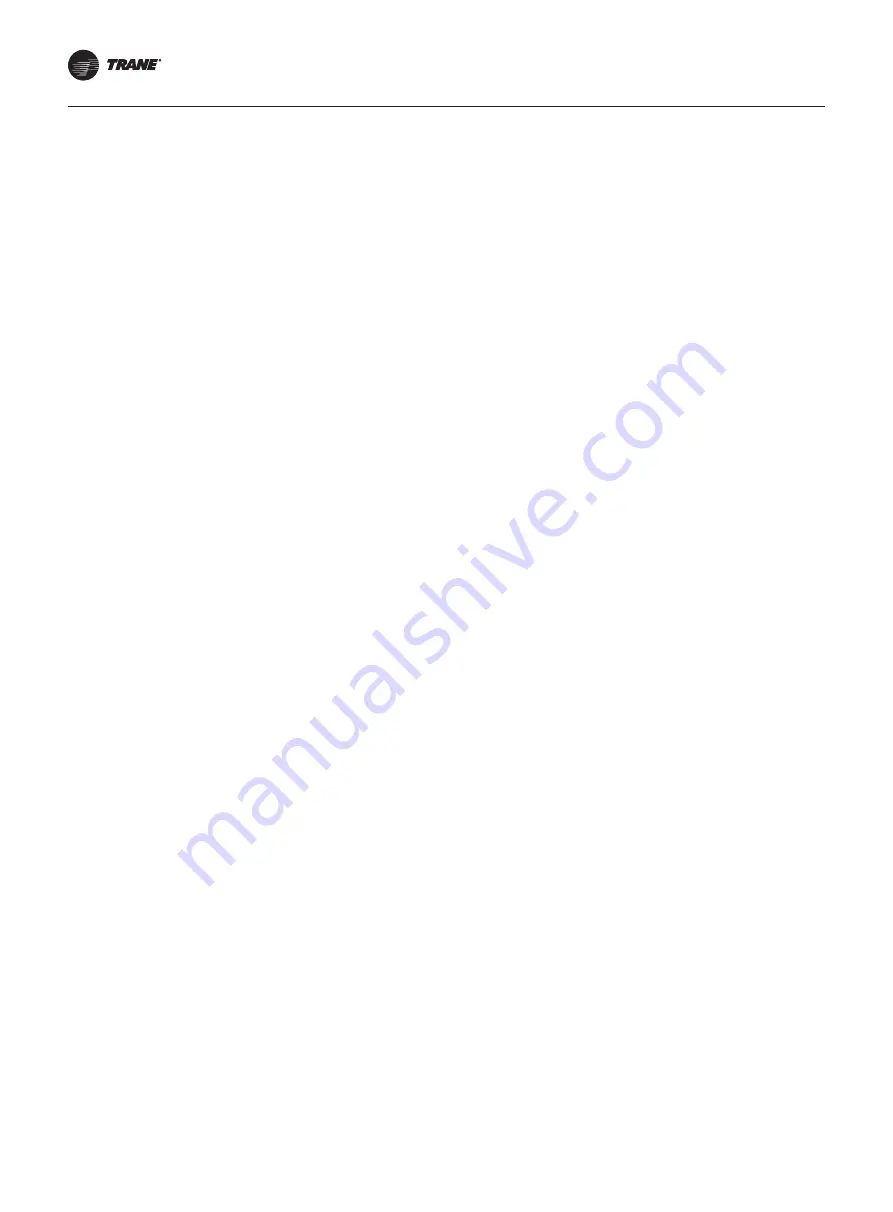
24
Unit Installation Requirements
• Water filter: Y-shaped water filter must be installed within 50cm of the water inlet pipe of the air conditioning unit to prevent impurities in
the pipe from blocking the water-side heat exchanger and causing unit failure. The number of meshes for the filter shall be 40. If there
is an external pump, the water filter must also be installed at the water inlet of the pump. The number of meshes for the filter shall be 40
to avoid pump damage.
• Water flow switch: the water flow switch must be installed at the water outlet of the unit. The straight distance at least 5 times of the pipe
diameter shall be reserved at the front and rear ends. If there is an internal water flow switch, the switch will not be installed again.
• Exhaust valve: the automatic exhaust valve shall be arranged at the top of the main outlet pipeline and the main return pipeline for the
water system to exhaust the air in the cold water system, ensure that the water flow of the unit meets the requirements of the product and
avoid cavitation noise and damage to the water pump. The exhaust valve of the water system is generally installed at the top of the
junction between the vertical pipe and the horizontal pipe for the water system and is 0.5 meters higher than the upper horizontal plane
of the fan coil at the highest position of the water system. When the exhaust valve is installed in the horizontal manifold, it shall be
installed on a pipe section with 2 to 3specifications larger than the manifold, and straight pipes at least 4 times the pipe diameter are
arranged on both sides, so that water and air are discharged through the exhaust valve after separation.
• Leakage prevention of exhaust valve: for the exhaust device, it is necessary to consider the cut-off measures for easy replacement
when it is damaged or fails. All exhaust pipes shall be connected to the sink and the floor drain in order to discharge water and prevent
the exhaust device from damage, failure or leakage to destroy the household environment.
• Expansion tank: the expansion tank shall be arranged in the water system to adapt to the water pressure fluctuation caused by the
water temperature change in the water supply system. The gravity expansion tank shall be installed on the top of the main water return
riser of the pump for the unit, the make-up pipe is connected to the water return pipe of the pump, and the overflow device is provided;
or the pressure type expansion tanks installed on the main water return pipe, and the automatic make-up valve and the automatic pres
sure relief valve are provided. The size of expansion tank can be selected by 3% of the total water volume of the water system for the air
conditioning unit.
• Operating water pressure: the water pressure of the water side heat exchanger for the air conditioning unit shall not exceed 0.5MPa(i.e.
the maximum operating pressure), so as to avoid damage to the parts on the cold water side of the unit.
• Two-way/three-way valve installation: the two-way valve or three-way solenoid valve shall be installed at the outlet of the fan coil to avoid
complaints of waterway vibration and noise.
• Two-way valve installation: the water system cannot completely use two-way solenoid valves. If the two-way valve is used, it can be
mixed with the three-way valve. The quantity ratio can be 1/3 of two-way valves and 2/3 of three-way valves. The two-way valve can be
installed on the fan coil near the air conditioning unit, and the threeway valve can be installed in the far end. If only two-way valves are
installed, the pressure differential bypass valve can be added between the main water supply and return pipes of the air conditioning unit
at the same time.
• Differential pressure bypass valve: if the differential pressure bypass valve is used in the system, it is necessary to ensure that the short
circulation loop of the bypass valve contains an energy storage tank and also meets the water volume requirements, that is, 10 liters of
water per kilowatt of cooling capacity. When all fan coils are turned off and the two-way valve is closed, the opening size of the differential
pressure bypass valve and the bypass valve flow must ensure that the inlet and outlet water temperature difference is controlled between
4-6
℃
to ensure the water flow requirements of the unit.
•
Parallel units: when two or more units are used in parallel, it is recommended that a manifold should be installed on the main water
return pipe to ensure the return water supply and correct flow distribution of the unit. When water chilling units with different cooling
capacities are connected in parallel in a water system (not recommended), a hydraulic balance valve must be installed to ensure different
water flow requirements of the water-side heat exchangers for the water chilling units with different cooling capacities. It is recommended
that the water pipes for the parallel water chilling units be installed in the same way as the reversed return pipes.
• Check valve: if the unit is located at the lower position of the whole water system, the check valve shall be installed on the outlet pipe of
the unit to prevent the impact of water hammer on the water system parts of the unit.
• Bypass pipeline: the bypass pipelines and the bypass valves must be installed at the inlet and outlet of the water system for the unit.
All external water supply pipeline systems shall be thoroughly flushed prior to the final connection of the unit. It is strictly prohibited to
mix sundries in the water system, otherwise serious consequences may be caused. The bypass valves shall be used to bypass the unit
and the terminal heat exchanger for flushing. After flushing, the bypass valves shall be closed, and the drain valves on the inlet and outlet
pipes shall be opened.
• Drainage: drainage pipes and drainage valves shall be installed at the lowest point of the water system and the lower part of the equip
ment to be drained, and the floor drain or funnel shall be connected to facilitate the cleaning and maintenance of the water system.