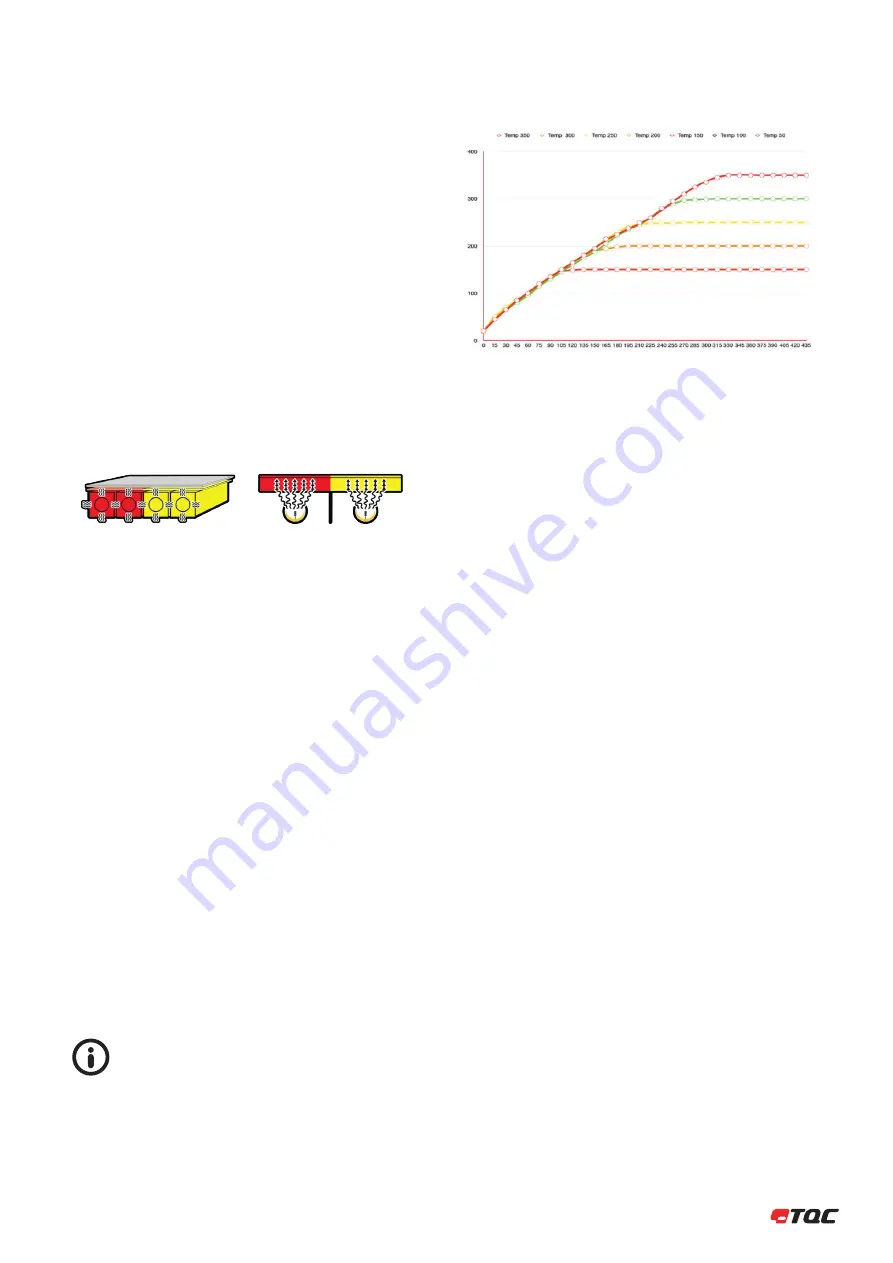
15 |
11.1 General
Even though the CureView is designed to the highest specifications possible
the CureView has limitations. We simply are not able to go beyond the laws
of physics. In order to explain some of the limitations of the TQC CureView
the following chapter will include some of the intricacies of thermal
dynamics involved with using the CureView.
11.2 Basics of Gradient Ovens:
The TQC CureView is a new generation of Gradient-ovens that allows for
significantly more advanced tests and doesn’t require preheating. The
implementation of the latest heating techniques in the TQC CureView
provide a different heat transfer compared to that of older systems with
conventional heating. The direct IR-irradiation by the TQC CureView allows
for a significantly more efficient heating than traditional gradient oven
systems. Due to this new heating system multiple components and
procedures had to be changed in the machine. Below is a simplified image
highlighting the difference in build of conventional systems and the new
TQC CureView.
Due to the difference in construction the heat transfer is significantly
different. Where the older systems work based on conduction of heat the
TQC CureView is based on transmittance of energy by IR-radiation. Older
Gradient ovens often suffer from loss in efficiency by improper contact
between the heating element, glass-bed and/or test panel. Because older
models have the thermocouple installed directly at the heater, they have
been compensated for the offset that occurs due to the different contacts
required to transfer the heat. Any small misalignment or other problem will
result in a loss of efficiency. This will cause significant differences in the
temperature of the test-panel. The TQC CureView is created such that it
regulates the heaters based on the temperature probe that is positioned on
top of the panel, thus at the actual spot where the temperature is relevant.
When comparing old and new systems side by side there might be a
temperature offset that has to be accounted for. This off-set is due to
deviation from older machines. Where test were set to be performed at
180˚C / 356˚F they could actually have been performed at 150˚C / 302˚F.
This off-set varies depending on the condition of the old machines.
To determine this off-set it is recommended to measure the actual
temperature obtained on the surface of the test panel.
Due to the new and improved heating systems no preheating is required.
This eliminates an irregular heating of the panel and allows for a repeatable
ramping of the temperature on the panel. The ramping is controlled and will
follow the same slope for all temperatures. The ramping for the heating can
be programmed in the Gradient oven. Below graph shows a default slope
being equal for all set point temperatures.
All following examples of ramping and heating graphs are
generalized and not correlated to a specific substrate or
ramp speed unless otherwise stated.
In the following graph the vertical axis shows the temperature in ˚C and the
horizontal axis displays the time (s). All set temperatures follow the same
ramp. Adjusting the ramp value can control the ramp slope.
11.3 Substrate material
The main influence for differences between tests is the substrate that tests
are performed on. Different substrates react differently to heat. Some
substrate function as an isolator and others as an excellent conductor of
heat. This ability or it’s lack to conduct heat determine the maximal
temperature difference between 2 heaters. On a well conducting material
the difference between 2 elements is lower than on a less conducting
substrate. The property of metals to conduct heat is a temperature
dependent function. If a gradient from 25˚C to 125˚C / 77˚F to 257˚F
is obtainable this doesn’t mean that 125°C to 225°C / 257˚F to 437˚F is
possible as well or vice versa. In order to test for the suitability of a program
and/or substrate it is advised to run a test-run on uncoated substrate prior
to performing the real test.
Full thermal properties of a substrate can be calculated. Full calculations
and factors can be found in the “ Handbook of Chemistry and physics.”
Calculating the thermal response of panels is however tricky due to the
large number of variables.
11.4 Surrounding / environmental conditions.
The TQC CureView has been designed such that it will keep draft away
from the panel but still allow the panel to be visible. Though the Cureview
is designed to eliminate as many influences as possible. Small fluctuations
in the heating behavior can be caused by changes in temperature and
humidity of the surrounding air. These parameters not only influence
the heating capabilities of the CureView but in more significant manner
the evaporation of samples as tested according the ISO 2812-5 or curing
of powder coatings. Stable laboratory conditions are required to create
reproducible results. Please consult internal guidelines or international
standards for the required climatic conditions required for the performed
test.
11.5 Ramping
The TQC CureView can be set for custom ramping speeds. A Ramping
indicates the speed in degree per second the CureView will heat a panel.
The selected ramping will influence the amount of heat generated by the
lamps. The generated heat needs to flow from the bottom of the panel to
the top prior to being detected by the probes. This process depends on
the thermal properties of the test panel. Thickness, material type, surface
finishing and set end temperature all influence the thermal response. If the
ramping is set to high there might be an overshoot of the set temperature.
11 THERMAL DYNAMICS
Conventional heating
IR-heating
Summary of Contents for CureView AB8000
Page 2: ......
Page 28: ......
Page 30: ...30 Date Name Signature Signature Instructed by Operator list...