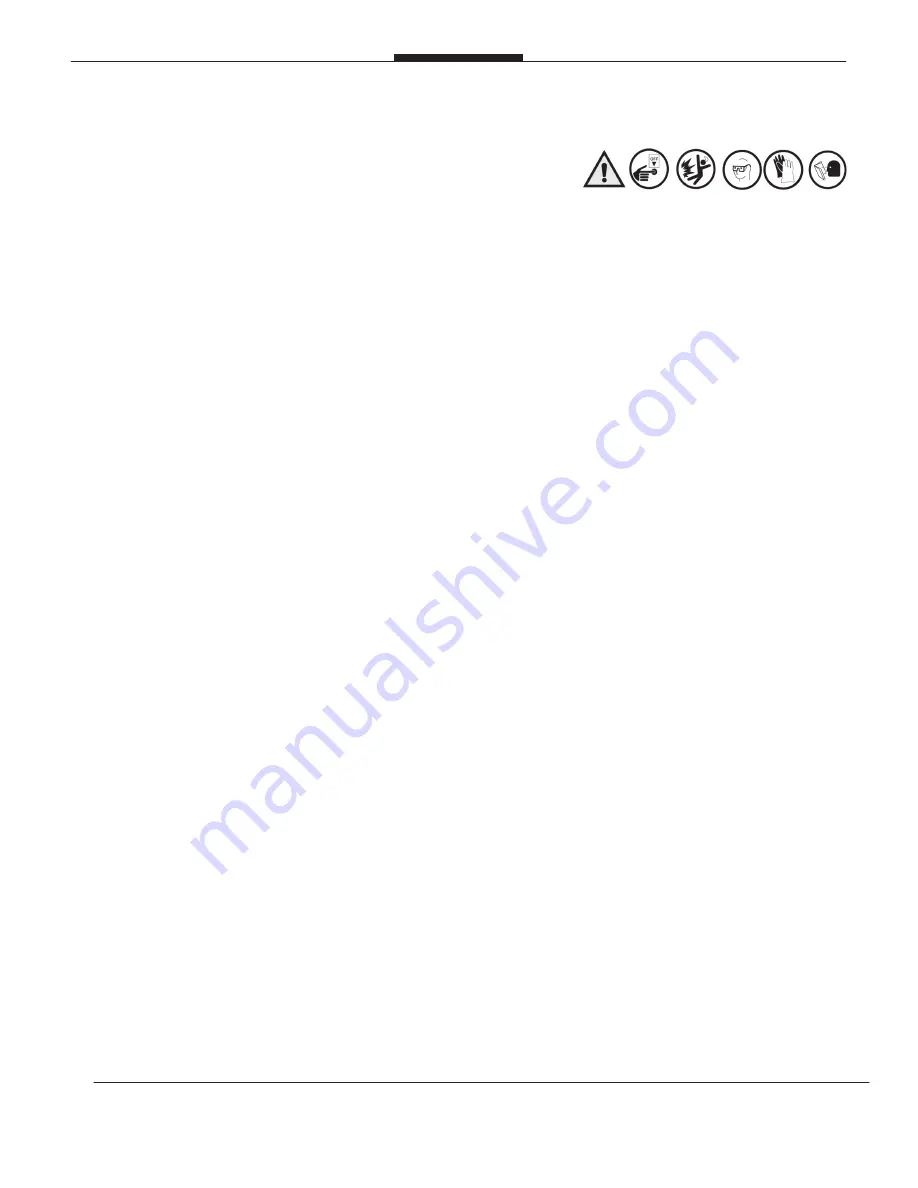
Page 39
Meter Trouble Shooting
PROBLEM: Leaking packing gland and/or housing
Two common causes of packing gland leakage are thermal expansion and hydraulic shock. If two valves in a pip-
ing system (on either side of the meter) are closed at one time, and if the temperature rises as little as 1ºF in the
system, it could result in a rise in pressure within the system that would exceed the working pressure rating of the
meter. To avoid this hazard caused by thermal expansion, a pressure-relief valve of some kind must be installed in
the system.
Hydraulic shock occurs when a large volume (mass) of liquid is moving through a pipe line at a high velocity and a
valve is suddenly closed. When the flow is stopped, the entire mass of the liquid in the piping system acts as a bat-
tering ram, causing a shock effect within the meter. Since the valve is usually located at the meter outlet, the meter
housing, packing gland and the meter internal members receive the full impact of such hydraulic shock. To prevent
this hazard a slow closing two-stage valve should be used with the meter. On those systems where a two-stage
slow closing valve cannot be used, an impact-absorbing air cushioning device should be used.
PROBLEM: Product flows through meter but register does not operate.
A) Gear train motion interrupted by non-functioning gear due to broken pin or key. Replace pin or key.
B) If all meter parts are moving then problem is in register.
C) Remove register from meter. If all meter parts are moving but output shaft of adjuster assembly is not,
adjuster is worn and must be replaced.
D) If totalizer numerals (small numbers) on register are recording, but the big numerals are not moving,
register needs repair.
PROBLEM: Product flows through meter but register does not record correctly.
A) Adjuster assembly not properly calibrated, See METER CALIBRATION on page 11 for more instructions.
B) The factory installed gear train may have incorrect gearing ratio.
C) Check register for defects.
PROBLEM: No flow through meter.
A) Faulty non-functioning pump.
B) Foreign matter within the system, meter or components.
C) Meter has a broken rotor or rotor shaft.
D) Excessive wear on timing gears or bearings.
E) Meter ―frozen‖ due to build-up of chemical ―salts‖ inside metering chamber.
F) Valve not open or not functioning.
PROBLEM: Meter runs too slow.
A) There is a flow restriction within the system. (i.e.: tees, elbows, valves, strainer, etc.)
B) Foreign matter in system, meter or components.
C) Meter gears or rotors partially ―salted‖ enough to slow up rotation of parts.
E) Valve internal mechanism faulty. Valve does not open fully.
Summary of Contents for 700-LP Series
Page 10: ...Page 10 Meter Dimensions in Inches Millimeters...
Page 14: ...Page 14 700 20 LP Meter Assembly...
Page 16: ...Page 16 730 20 LP Vapor Eliminator Assembly...
Page 18: ...Page 18 720 20 LP Strainer Assembly...
Page 20: ...Page 20 757 20 LP Differential Valve Assembly...
Page 22: ...Page 22 782 20 LP In Line Check Assembly...
Page 45: ...Page 45 Page 45 NOTES...
Page 46: ...Page 46 Page 46 NOTES...