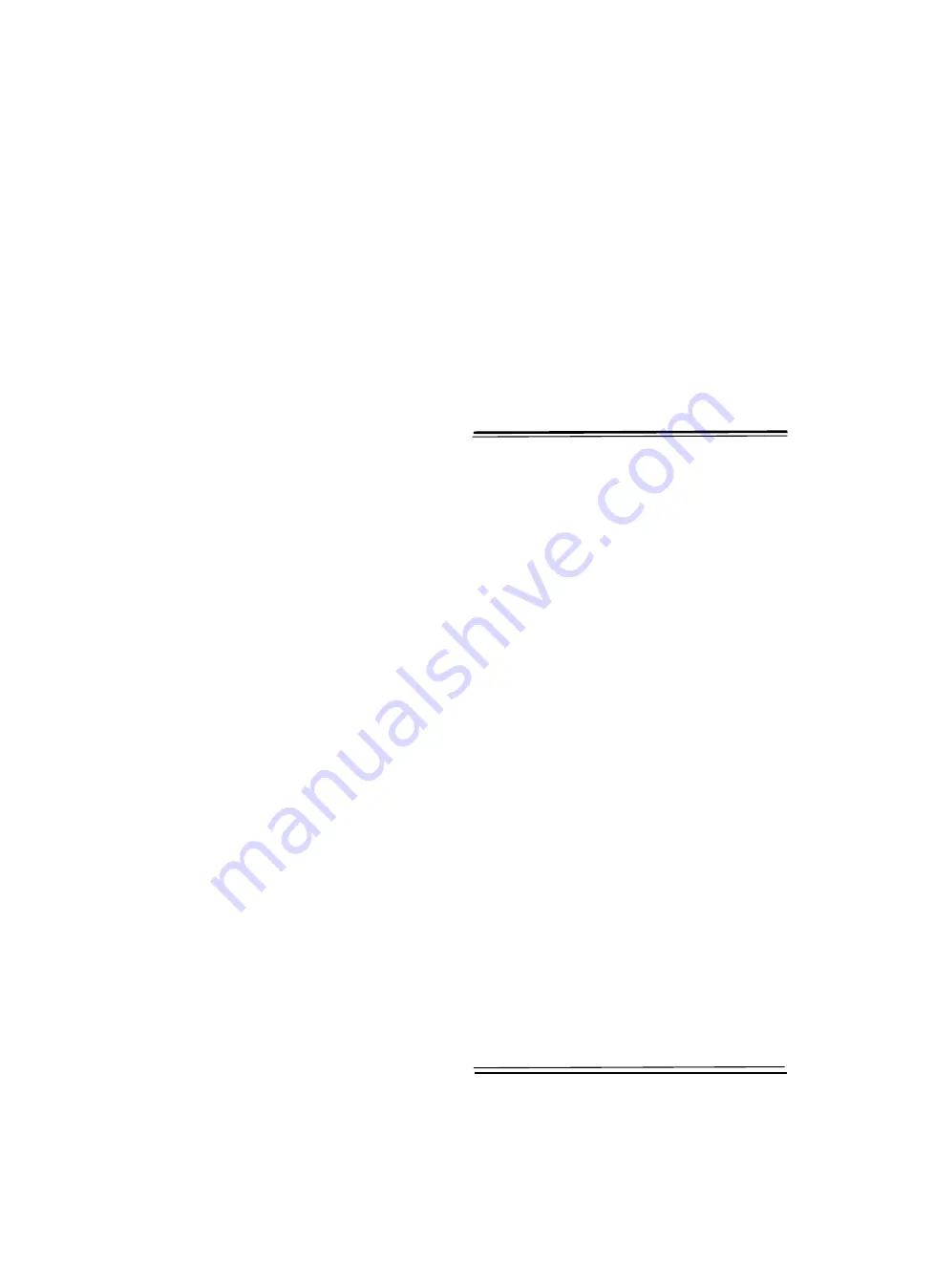
6-
13
.
General safety precautions for using R32 refrigerant
6-
13
-1
.
Recovery
6-
13
-2
.
Decommissioning
•
Before carrying out this procedure, it is essential that
the technician is completely familiar with the
equipment and all its details. Only a qualified installer
(
*
1) or qualified service person (
*
1)
is allowed to do this work.
•
It is recommended good practice that all refrigerants
are recovered safely.
•
Prior to the task being carried out, an oil and
refrigerant sample shall be taken in case
analysis is required prior to re-use of reclaimed
refrigerant.
•
It is essential that electrical power is available before
the task is commenced.
a) Become familiar with the equipment and its
operation.
b) Isolate system electrically.
c) Before attempting the procedure ensure that
:
•
mechanical handling equipment is available, if
required, for handling refrigerant cylinders;
•
all personal protective equipment is available
and being used correctly;
•
the recovery process is supervised at all times by
a competent person;
•
recovery equipment and cylinders conform to the
appropriate standards.
•
When removing refrigerant from a system, either
for servicing or decommissioning,
it is recommended
good practice that all refrigerants are removed safely.
•
When transferring refrigerant into cylinders, ensure that
only appropriate refrigerant recovery cylinders are
employed.
•
Ensure that the correct number of cylinders for holding
the total system charge are available.
•
All cylinders to be used are designated for the
recovered refrigerant and labelled for that refrigerant
(i.e. special cylinders for the recovery of refrigerant).
•
Cylinders shall be complete with pressure relief valve
and associated shut-off valves in good working order.
•
Empty recovery cylinders are evacuated and, if
possible, cooled before recovery occurs.
•
The recovery equipment shall be in good working order
with a set of instructions concerning the equipment that
is at hand and shall be suitable
for the recovery of flammable refrigerants.
•
In addition, a set of calibrated weighing scales shall be
available and in good working order.
•
Hoses shall be complete with leak-free disconnect
couplings and in good condition.
•
Before using recovery machine check that it is
satisfactory working order, has been properly
maintained and that any associated electrical
components are sealed to prevent ignition in the event
of a refrigerant release.
•
Consult manufacturer if in doubt.
•
The recovered refrigerant shall be returned to the
refrigerant supplier in the correct recovery cylinder, and
the relevant Waste Transfer Note arranged.
•
Do not mix refrigerants in recovery units and especially
not in cylinders.
•
If compressors or compressor oils are to be removed,
ensure that they have been evacuated to an acceptable
level to make certain that flammable refrigerant does
not remain within the lubricant.
•
The evacuation process shall be carried out prior to
returning the compressor to the suppliers.
•
Only electric heating to the compressor body
shall be
employed to accelerate this process.
•
When oil is drained from a system, it shall be carried
out safely.
d) Pump down refrigerant system, if possible.
e) If a vacuum is not possible, make a manifold so
that refrigerant can be removed from the various
parts of the system.
f) Make sure that cylinder is situated on the scales
before recovery takes place.
g) Start the recovery machine and operate in
accordance with manufacturers instructions.
h) Do not overfill cylinders (No more than
80%volume liquid change).
i) Do not exceed the maximum working pressure of
the cylinder, even temporarily.
j) When the cylinders have been filled correctly and
the process complete, make sure that cylinders
and the equipment are removed from site
promptly and all isolation valves on the
equipment are closed off.
k) Recovered refrigerant shall not be changed into
another refrigerant system unless it has been
cleaned and checked.
6-
13
-3
.
Labelling
•
Equipment shall be labelled stating that it has been de-commissioned and emptied of refrigerant.
•
The label shall be dated and signed.
•
Ensure that are labels on the equipment stating the equipment contains flammable refrigerant.
- 46 -