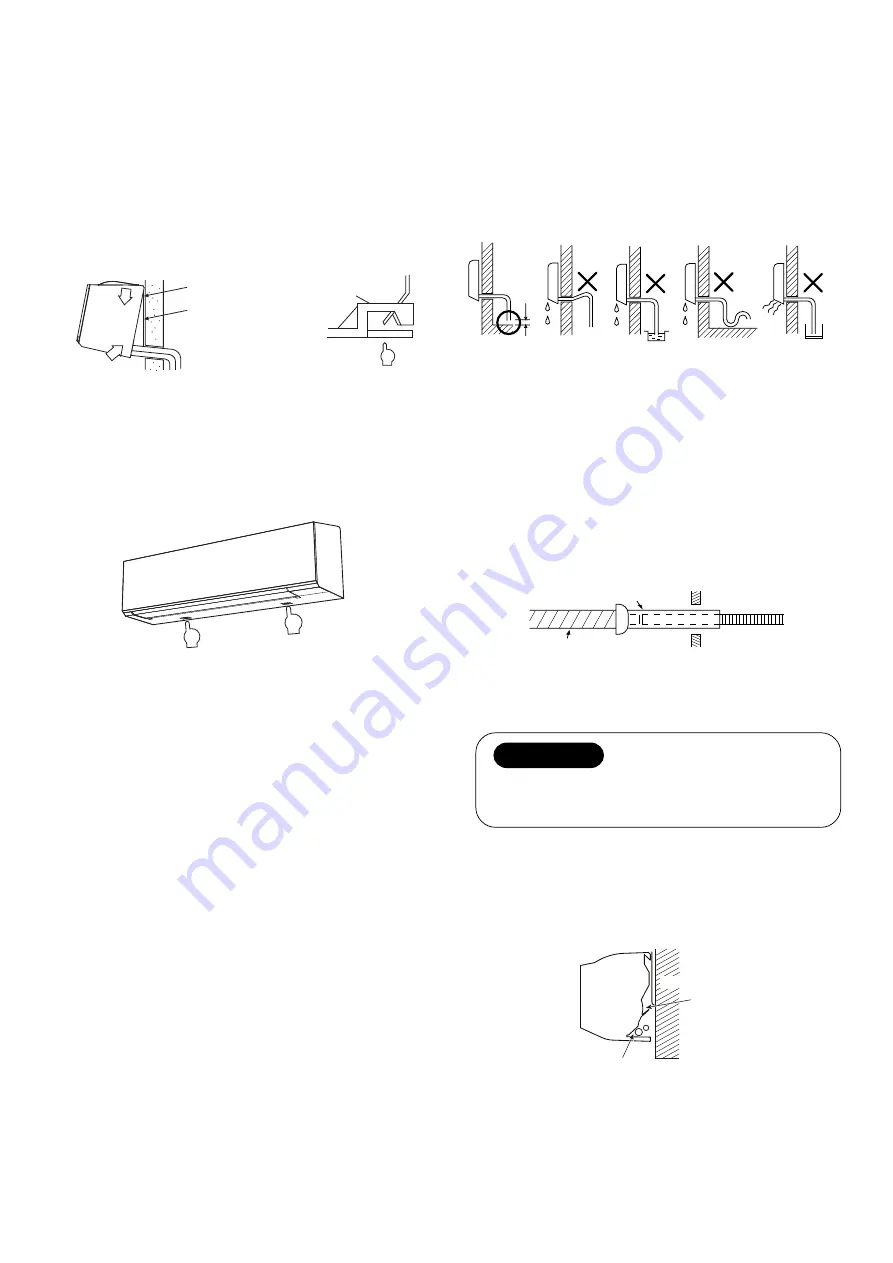
10-3-5. Indoor unit fixing
1. Pass the pipe through the hole in the wall, and hook
the indoor unit on the installation plate at the upper
hooks.
2. Swing the indoor unit to right and left to confirm that
it is firmly hooked up on the installation plate.
3. While pressing the indoor unit onto the wall, hook it
at the lower part on the installation plate. Pull the
indoor unit toward you to confirm that it is firmly
hooked up on the installation plate.
Fig. 10-3-1
4
•
For detaching the indoor unit from the installation
plate, pull the indoor unit toward you while pushing
its bottom up at the specified parts.
10-3-
6
. Drainage
1. Run the drain hose sloped downwards.
NOTE
•
Hole should be made at a slight downward slant on
the outdoor side.
Fig. 10-3-1
6
2. Put water in the drain pan and make sure that the
water is drained out of doors.
3. When connecting extension drain hose, insulate the
connecting part of extension drain hose with shield
pipe.
Fig. 10-3-1
7
CAUTION
Arrange the drain pipe for proper drainage from the
unit. Improper drainage can result in dew-dropping.
This air conditioner has the structure designed to drain
water collected from dew, which forms on the back of
the indoor unit, to the drain pan.
Therefore, do not store the power cord and other parts
at a height above the drain guide.
Fig. 10-3-1
8
Drain hose
Inside the room
Shield pipe
Extension drain hose
Do not put
the drain
hose end in
the drainage
ditch.
Do not form the
drain hose into
a wavy shape.
Do not put
the drain
hose end
into water.
Do not rise the
drain hose.
50 mm
or more
Drain
guide
Space for pipes
Wall
Fig. 10-3-1
5
1
2
1
Hook here.
Installation plate
Hook
Press
(unhook)
Push
Push
- 73 -