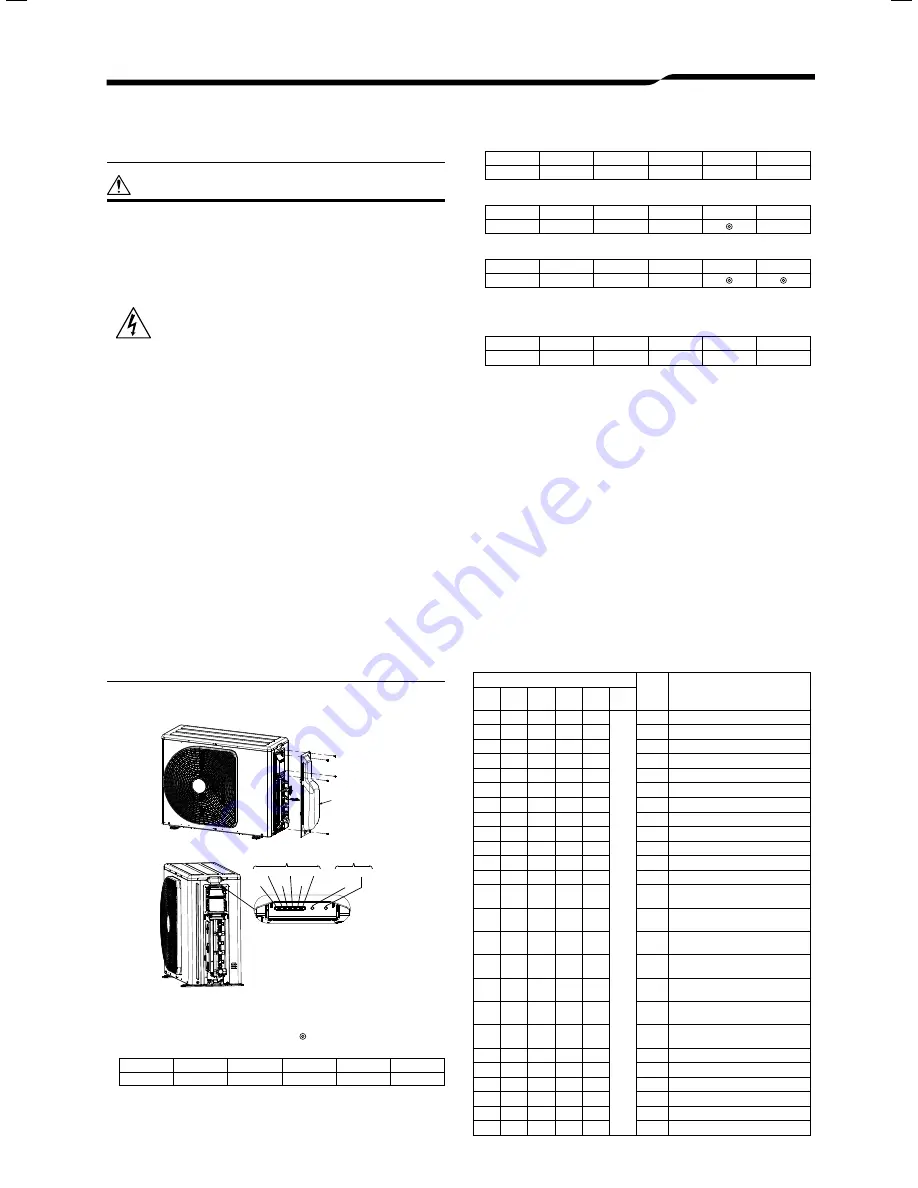
12
Installation Manual
Outdoor Unit
10
Pump-down Operation
■
Pump-down Operation (Recovering refrigerant)
CAUTION
Since the forcible running for collecting
refrigerant stops automatically after 10
minutes,
fi
nish collecting refrigerant within
10 minutes.
Electric current is applied on the
control board. Beware of electric
shock.
• The following must be certainly done
during pump down.
• Do not incorporate air into the
refrigeration cycle.
• Close the service valves. Stop the
compressor and remove the refrigerant
pipe.
If the refrigerant pipe is removed when
the compressor is operating and service
valves are opened, the refrigerant cycle
will inhale unwanted matter such as air
and the pressure in the cycle becomes
abnormally elevated. It may cause a
burst or injury.
1. Remove the valve cover screws.
2. Pull the valve cover in the direction of arrow, and remove it.
Valve cover
LED
Service switches
SW01
SW02
D800
D801
D802
D803
D804
D805
3. Turn on the circuit breaker to supply electricity.
In the initial LED display status, D805 is lighted as below.
: ON,
: OFF, : Rapid Flashing (5 times/sec.),
: Slow Flashing (1 time/sec.)
D800
D801
D802
D803
D804
D805
Start running all the indoor units connected to the outdoor unit in the
cooling mode.
The checking procedure cannot be completed if the cooling mode is not
operated in every indoor units.
4. Hold down SW01 for at least 5 seconds, and check that D800 is lighted
and D804 light is
fl
ashing ( 1 time/sec.).
D800
D801
D802
D803
D804
D805
5. Press SW01 for 1 time. Then D804 light is
fl
ashing (5 times/sec.).
D800
D801
D802
D803
D804
D805
6. Press SW02 for 1 time. Then D805 light is
fl
ashing (5 times/sec.).
D800
D801
D802
D803
D804
D805
7. Hold down SW02 for at least 5 seconds. Then outdoor unit start cooling
mode.
(The display is kept during the refrigerants collection operation.)
D800
D801
D802
D803
D804
D805
8. Close the valve stem of the service valve at the liquid end.
9. Make sure that the compound pressure gauge reading is –101 kPa
(–76 cmHg)
10. Close the valve stem of the service valve at the gas end.
11. The refrigerants collection operation is
fi
nished in maximum 10 minutes.
After the collection is
fi
nished, promptly stop the operation of all the
indoor unit.
(There are cases that the compressor restarts.)
12. When you want to start over the operation of the SW01 and SW02, press
the SW01 and SW02 at the same time for 5 sec. (It back to the initial
condition of 3.)
However, do not execute the operation during the refrigerants collection.
If by any chance the collection is stopped by the operation, start over the
refrigerants collection operation.
11
Troubleshooting
You can perform fault diagnosis of the outdoor unit with the LEDs on the P.C.
board of the outdoor unit in addition to using the check codes displayed on
the remote controller of the indoor unit.
Use the LEDs and check codes for various checks. Details of the check
codes displayed on the remote controller of the indoor unit are described in
the Installation Manual of the indoor unit.
LED displays and check codes
: ON (
* : 3 sec ON/0.5 sec OFF),
: OFF
Display
Indoor
check
code
Description
D800
(YL)
D801
(YL)
D802
(YL)
D803
(YL)
D804
(YL)
D805
(GN)
-
Normal operation (no error)
*
1C
Compressor case thermostat error
*
21
High pressure switch error
*
*
1C
Compressor system error
*
1D
Compressor lock
*
*
1F
Compressor breakdown
*
*
14
Driving element short circuit
*
*
*
16
Position detection circuit error
*
17
Current detection circuit error
*
*
1C
Communication error between MCU
*
*
1A
Fan system error
*
*
*
1E
Discharge temperature error
*
*
19
Discharge temperature sensor
(TD) error
*
*
*
1B
Outdoor air temperature sensor
(TO) error
*
*
*
18
Suction temperature sensor (TS)
error
*
*
*
*
18
Heat exchanger temperature
sensor (TE) error
*
1C
Gas pipe (unit A) temperature
sensor (TGa) error
*
*
1C
Gas pipe (unit B) temperature
sensor (TGb) error
*
*
1C
Gas pipe (unit C) temperature
sensor (TGc) error
*
*
*
-
PMV error (SH
≥
20)
*
*
*
-
PMV error (SH
≤
–8)
*
*
20
PMV leakage error (unit A)
*
*
*
20
PMV leakage error (unit B)
*
*
*
20
PMV leakage error (unit C)
*
*
*
*
-
Miswiring (mispiping) check error
1116691099_(01) EN.indd 12
1116691099_(01) EN.indd 12
9/22/15 5:59 PM
9/22/15 5:59 PM