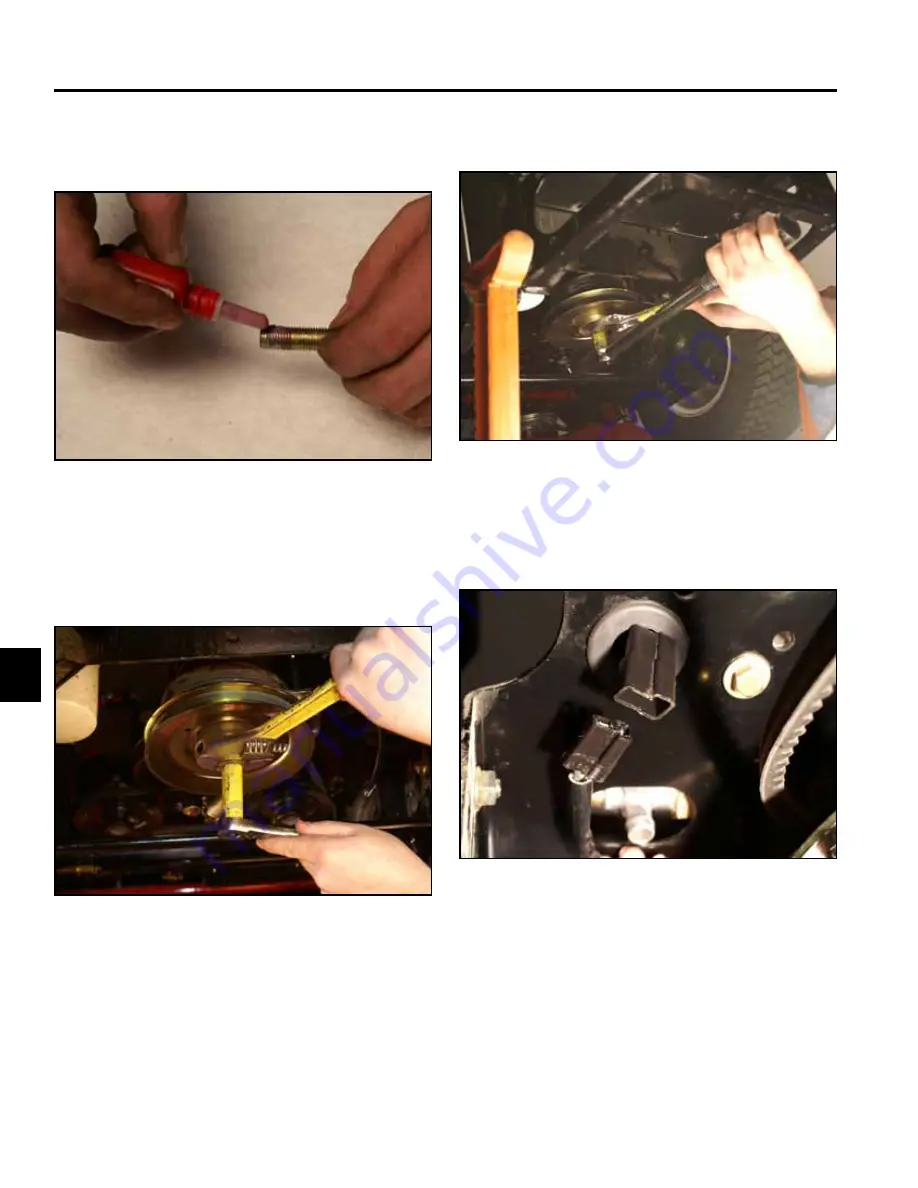
5-30
Z Master Z400 Service Manual
5
ENGINE
8. Install the center bolt and two spring washers that
hold the electric PTO clutch to the engine crankshaft
(Fig. 320).
Fig 320
PICT-0014c
Fig 322
PICT-0100a
10. Plug the clutch pigtail harness into the main harness
(Fig. 322).
Fig 321
PICT-0027c
9. Torque the center bolt to 55 ft-lbs. (Fig. 321).
7. Apply a thread locking compound to the clutch
retainer bolt (Fig. 319).
Fig 319
PICT-0026c
Summary of Contents for Z 440 Pro Value Series
Page 1: ...Z Master Z400 Series Service Manual LCE Products...
Page 3: ...THIS PAGE INTENTIONALLY LEFT BLANK...
Page 7: ...iv Z Master Z400 Service Manual THIS PAGE INTENTIONALLY LEFT BLANK TABLE OF CONTENTS...
Page 31: ...2 22 Z Master Z400 Service Manual 2 SPECIFICATIONS THIS PAGE INTENTIONALLY LEFT BLANK...
Page 65: ...3 34 Z Master Z400 Service Manual 3 CHASSIS THIS PAGE INTENTIONALLY LEFT BLANK...
Page 87: ...4 22 Z Master Z400 Service Manual 4 HYDRAULIC SYSTEM THIS PAGE INTENTIONALLY LEFT BLANK...
Page 133: ...5 46 Z Master Z400 Service Manual 5 ENGINE THIS PAGE INTENTIONALLY LEFT BLANK...
Page 149: ...6 16 Z Master Z400 Service Manual 6 ELECTRICAL 74412 Schematics Wire Diagram Rev A...
Page 150: ...6 17 Z Master Z400 Service Manual 6 74410 ELECTRICAL Schematics Wire Diagram Rev A...
Page 151: ...6 18 Z Master Z400 Service Manual 6 ELECTRICAL 74411 Schematics Wire Diagram Rev A...
Page 152: ...6 19 Z Master Z400 Service Manual 6 ELECTRICAL 74413 and 74415 Schematics Wire Diagram Rev A...
Page 153: ...6 20 Z Master Z400 Service Manual 6 ELECTRICAL 74414 Schematics Wire Diagram Rev A...
Page 154: ...6 21 Z Master Z400 Service Manual 6 ELECTRICAL 74416 and 74417 Schematics Wire Diagram Rev A...
Page 157: ...6 24 Z Master Z400 Service Manual 6 ELECTRICAL THIS PAGE INTENTIONALLY LEFT BLANK...
Page 189: ...7 32 Z Master Z400 Service Manual 7 MOWER DECKS PTO THIS PAGE INTENTIONALLY LEFT BLANK...
Page 190: ...Z Master Z400 Series Service Manual Form No 492 9166...