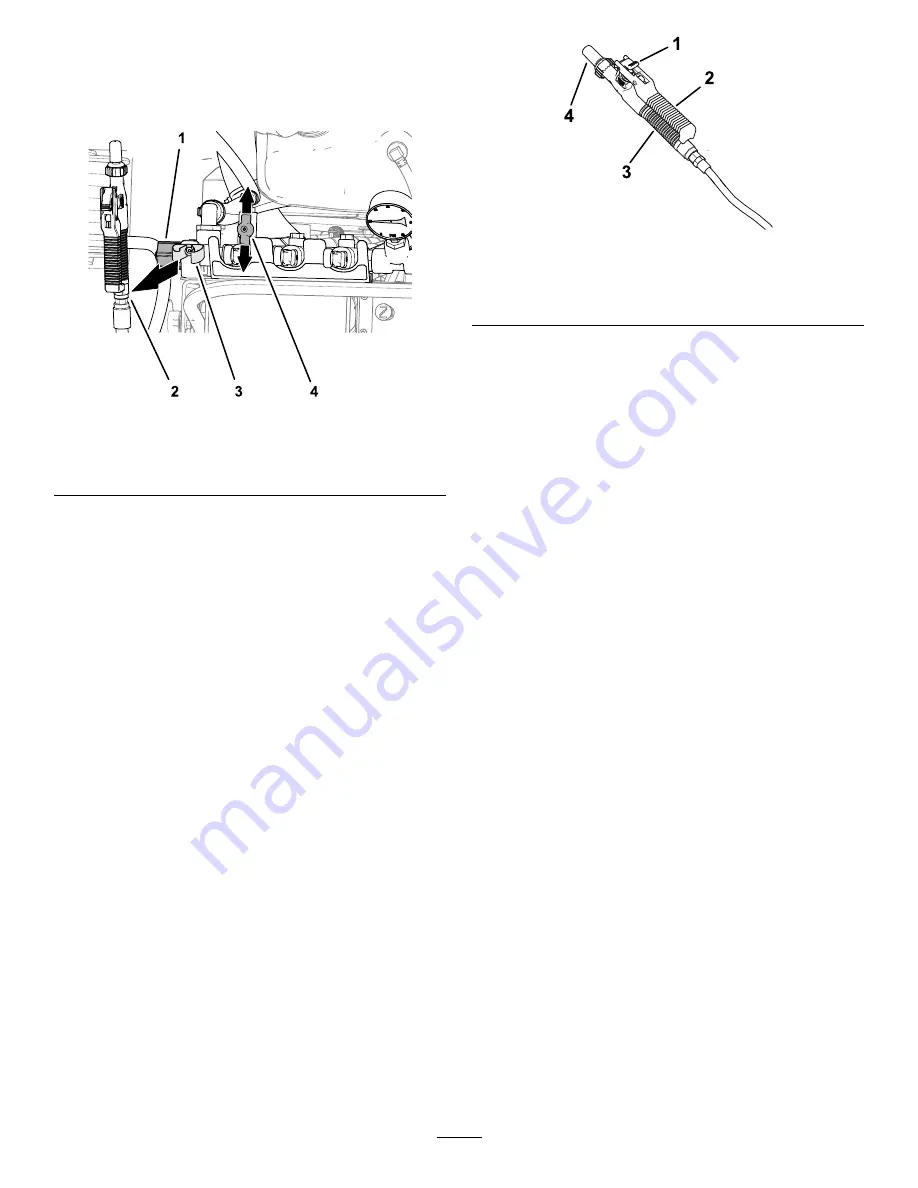
2.
Ensure that the 3 boom sprayer-control valves
are in the O
FF
position.
3.
Remove the spray wand from the tool clip at the
left side of the machine (
g312652
Figure 47
1.
Throttle-valve knob
3.
Tool clip
2.
Spray wand
4.
Spray wand-shutoff valve
4.
Firmly grip the spray wand and point it in the
direction that you will spray.
Note:
The wand may recoil; ensure that you
hold it securely.
5.
Open spray wand-shutoff valve (
6.
Use the throttle valve (
) to adjust the
spray-system pressure as follows:
•
To increase the spray-system pressure to the
wand, rotate the throttle valve clockwise.
•
To decrease the spray-system pressure
to the wand, rotate the throttle valve
counterclockwise.
7.
Squeeze the trigger to the spray-wand handle
to begin spraying; lock the trigger in place if
desired (
).
g312653
Figure 48
1.
Trigger lock
3.
Spray wand handle
2.
Spray wand trigger
4.
Spray tip
8.
When finished spraying, if you locked the trigger
of the spray-wand—unlock it, and release the
trigger (
9.
Close the spray wand-shutoff valve, shut off the
spray pump, and insert the spay wand into the
tool clip (
).
After Operation
After Operation Safety
General Safety
•
Park the machine on level ground and allow it to
cool. Never allow untrained personnel to service
the machine.
•
Disengage the spray or close the spreader gate,
set the parking brake, shut off the engine, and
remove the key or disconnect the spark-plug wire.
Wait for all movement to stop before adjusting,
cleaning or repairing the machine.
•
Clean the machine as stated in
and
(page 43)
•
Frequently check for worn or deteriorating
components that could create a hazard. Tighten
loose hardware.
•
Shut off the fuel when storing or transporting the
machine. Do not store fuel near flames or drain
fuel indoors.
41
Summary of Contents for Spray Master
Page 48: ...g313490 Figure 60 52 inch machine shown 1 Rear tie down points 48...
Page 84: ...g317991 Machine Model 34237 Electrical Schematic 135 6146 Rev B 84...
Page 85: ...Notes...
Page 86: ...Notes...
Page 87: ...Notes...
Page 88: ......