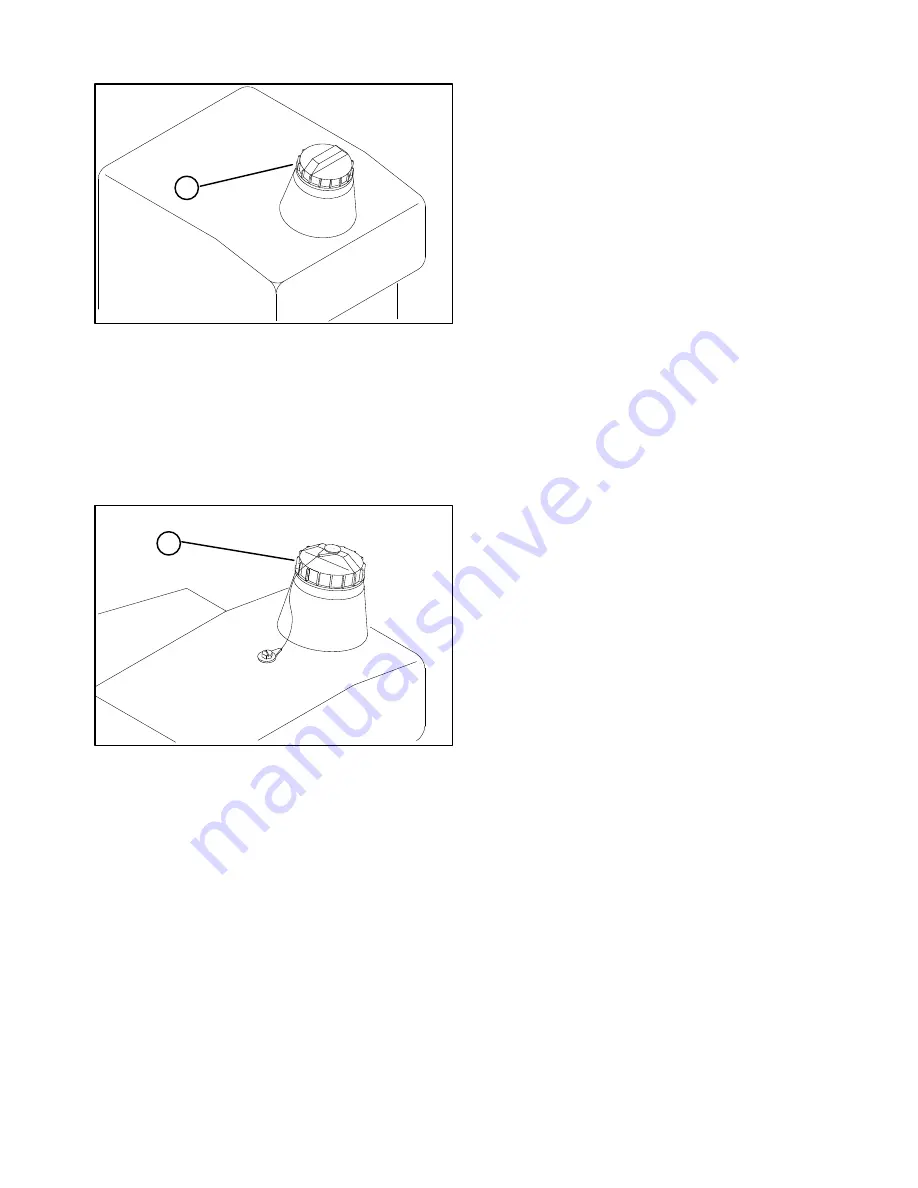
!
-+74)
7)/ 6%1. '%3
$" $ !
-+
The hydraulic system is designed to operate on Mobil
424 hydraulic oil. The machine's 3 gallon reservoir is
filled at the factory with oil. However, check level of oil
before engine is first started and daily thereafter.
Remove cap from hydraulic oil reservoir.
-+74)
-/ 4)5)482-4 '%3
Check level of oil in reservoir. Oil level should be up
to top of cone point on tank screen.
If fluid level is low, slowly fill reservoir with
appropriate hydraulic fluid until level reaches bottom of
screen.
! #
4273 :(4%7/-' /7-( )'200)1()( *24
%0&-)16 6)03)4%674)5 '215-56)16/: &)/29 ;
6:3) %16-9)%4 ,:(4%7/-' */7-(
Mobil
Mobil Fluid 424
Amoc
Amoco 1000
International Harvester
Hy-Tran
Texaco
TDH
Shell
Donax TD
Union OIl
Hydraulic/Tractor Fluid
Chevron
Tractor Hydraulic Fluid
BP Oil
BP HYD TF
Boron OIl
Eldoran UTH
Exxon
Torque Fluid
Conoco
Power-Tran 3
Kendall
Hyken 052
Phillips
HG Fluid
26)
The fluids within this group are interchangeable.
Install reservoir cap.
!!
To prevent system contamination, clean
top of hydraulic oil containers before puncturing.
Assure pour spout and funnel are clean.
! "
Check tire pressure before operating machine. Correct
air pressure in front and rear tires is 4-6 psi.
Summary of Contents for Sand Pro 3020
Page 26: ... ...