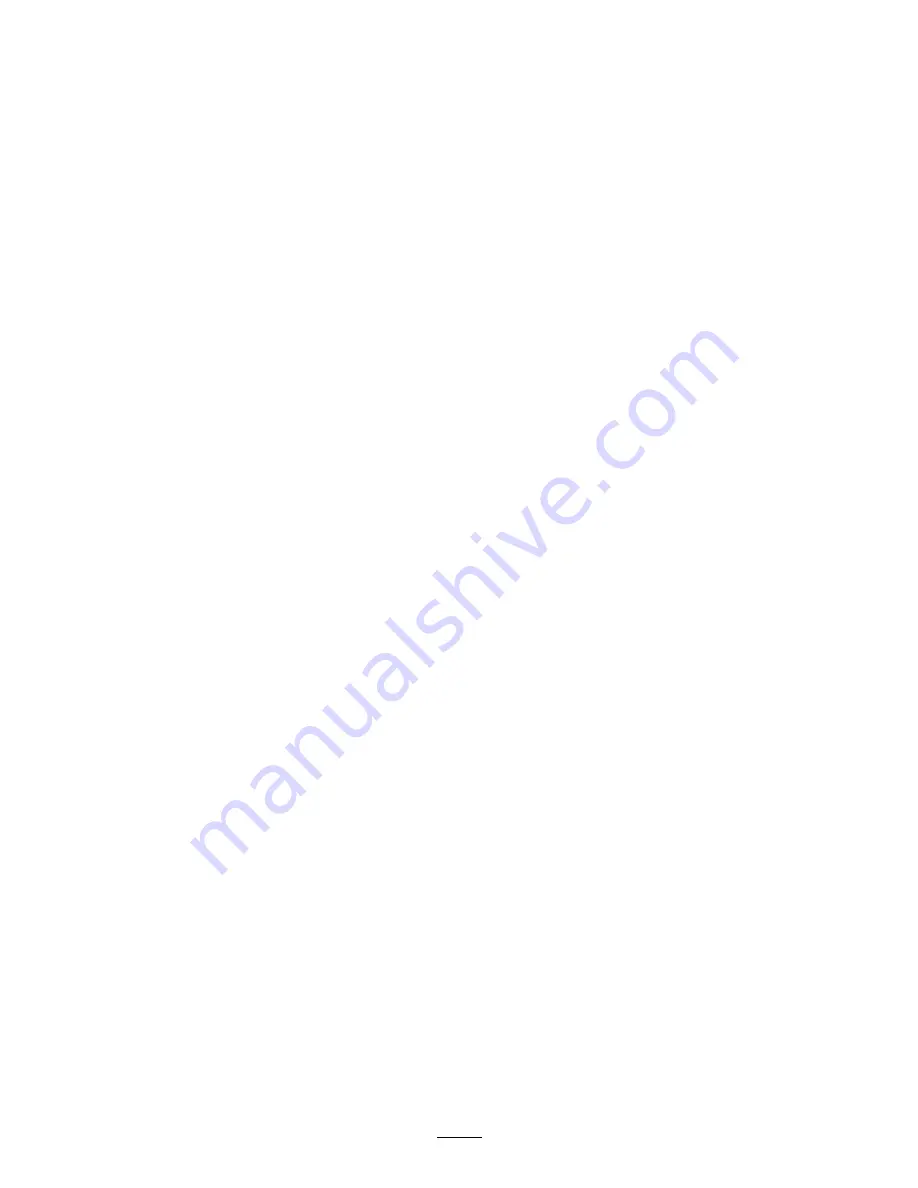
General Operation
•
Be sure the area is clear of other people before
mowing. Stop the machine if anyone enters the area.
•
Do not touch equipment or attachment parts which
may be hot from operation. Allow to cool before
attempting to maintain, adjust or service.
•
Use only Toro approved attachments. Warranty may
be voided if used with unapproved attachments.
•
Check carefully for overhead clearances (i.e.
branches, doorways, electrical wires) before operating
under any objects and do not contact them.
•
Slow down before making turns and use extra
caution.
•
Use caution when riding the platform over curbs,
rocks, roots, or other obstructions.
•
Look behind and down before backing up to be sure
of a clear path. Use extra care when operation in
reverse.
•
Never jerk the controls; use a steady motion.
•
Do not carry passengers.
Slope Operation
All slopes and ramps require extra caution. If you feel
uneasy on a slope, do not mow it.
•
Remove obstacles such as rocks, tree limbs, etc. from
the mowing area.
•
Watch for holes, ruts or bumps. Tall grass can hide
obstacles.
•
Use caution near drop-offs, ditches, or embankments.
The machine could suddenly turn over if a wheel
goes over the edge of a cliff or ditch, or if an edge
caves in.
•
Use extra care with grass catchers or other
attachments. These can change the stability of the
machine.
•
Keep all movement on slopes slow and gradual. Do
not make sudden changes in speed or direction.
•
Mow slopes side to side.
Service
•
Never store the machine or fuel container inside
where there is an open flame, such as near a water
heater or furnace.
•
Keep nuts and bolts tight, especially the blade
attachment bolts. Keep equipment in good
condition.
•
Never tamper with safety devices. Check safety
systems for proper operation before each use.
•
Use only genuine replacement parts to ensure that
original standards are maintained.
•
Check brake operation frequently. Adjust and service
as required.
Sound Pressure
Model 74534TE has a sound pressure level at the
operator’s ear of 88 dBA, which includes an Uncertainty
Value (K) of 1 dBA.
Model 74536TE has a sound pressure level at the
operator’s ear of 86 dBA, which includes an Uncertainty
Value (K) of 1 dBA.
The sound pressure level was determined according to
the procedures outlined in EN 836.
Sound Power
Model 74534TE has a guaranteed sound power level
of 100 dBA, which includes an Uncertainty Value (K)
of 1 dBA.
Model 74536TE has a guaranteed sound power level
of 100 dBA, which includes an Uncertainty Value (K)
of 1 dBA.
The sound power level was determined according to the
procedures outlined in ISO 11094.
Vibration Level for Model
74534TE
Hand-Arm
Measured vibration level for right hand = 0.8 m/s
2
Measured vibration level for left hand = 0.6 m/s
2
Uncertainty Value (K) = 0.4 m/s
2
Measured values were determined according to the
procedures outlined in EN 836.
Whole Body
Measured vibration level = 0.79 m/s
2
Uncertainty Value (K) = 0.39 m/s
2
Measured values were determined according to the
procedures outlined in EN 836.
Vibration Level for Model
74536TE
Hand-Arm
Measured vibration level for right hand = 1.1 m/s
2
6
Summary of Contents for GrandStand 74534TE
Page 65: ...Schematics Hydraulic Schematic Rev A 65 ...
Page 66: ...G015606 Electrical Schematic Rev A 66 ...
Page 67: ...Notes 67 ...
Page 68: ...Notes 68 ...
Page 69: ...Notes 69 ...