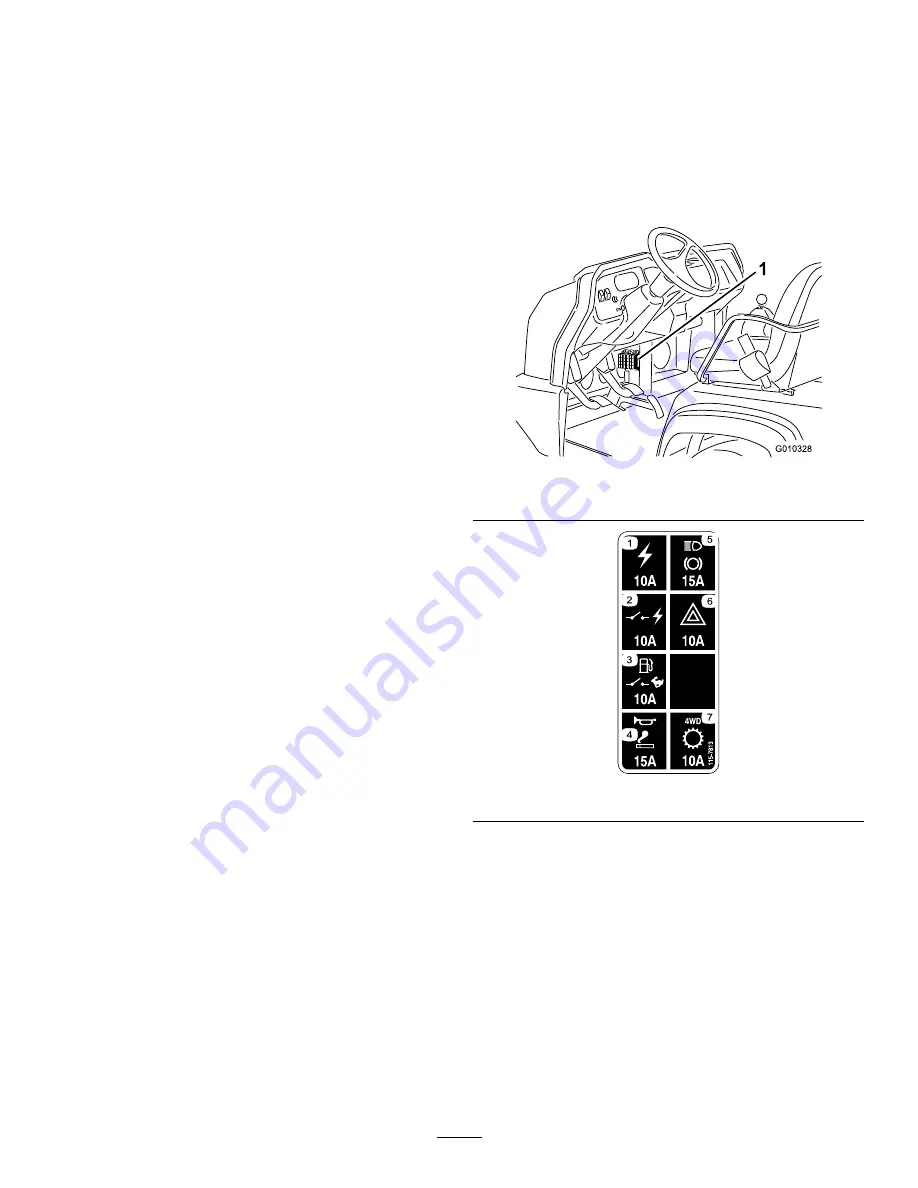
3. Remove the filter canister and clean the mounting
surface.
4. Lubricate the gasket on the filter canister with clean
oil.
5. Install the filter canister by hand until the gasket
contacts mounting surface, then rotate it an
additional 1/2 turn.
6. Tighten the drain plug on the bottom of the filter
canister.
Electrical System
Maintenance
Fuses
The fuses for the machine’s electrical system are
located under the center of the dash panel (Figure 42
& Figure 43).
Figure 42
1.
Fuses
Figure 43
39
Summary of Contents for 7354
Page 35: ...Figure 34 Figure 35 Figure 36 35 ...
Page 36: ...Figure 37 36 ...
Page 51: ...Schematics Hydraulic Schematic Rev A 51 ...
Page 52: ...High Flow Hydraulics Schematic Optional Rev A 52 ...
Page 53: ...Electrical Schematic Rev A 53 ...
Page 54: ...Notes 54 ...
Page 55: ...Notes 55 ...