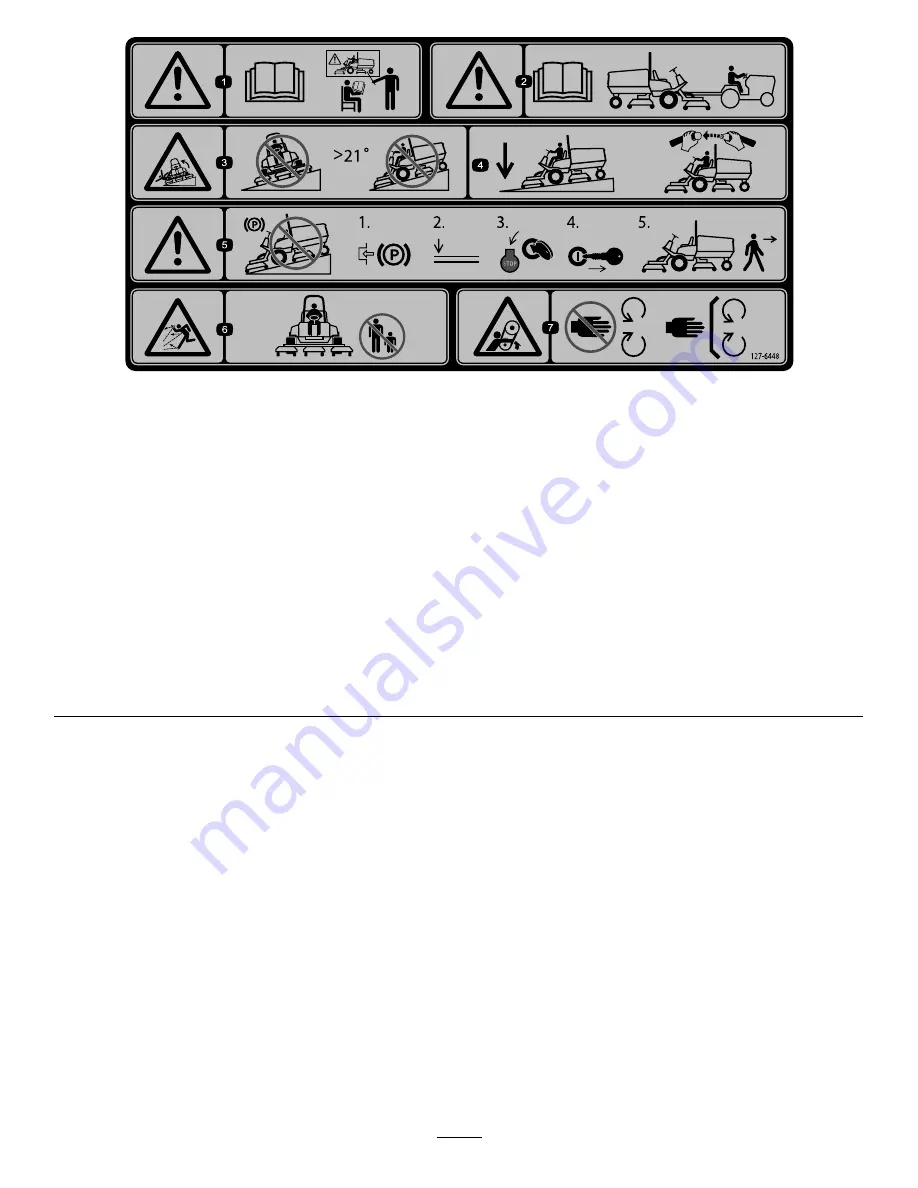
decal127-6448
127-6448
(Affix over Part No. 112-5297 for CE* for 4700 series machines)
Note:
This machine complies with the industry standard stability test in the static lateral and longitudinal tests with the maximum
recommended slope indicated on the decal. Review the instructions for operating the machine on slopes in the
Operator's Manual
and the conditions in which the machine is being operated to determine whether the machine can be operated in the conditions on
that day and at that site. Changes in the terrain can result in a change in slope operation for the machine. If possible, keep the
cutting units lowered to the ground while operating the machine on slopes. Raising the cutting units while operating on slopes can
cause the machine to become unstable.
1.
Warning—read the
Operator’s Manual
; do
not operate the machine
unless you have received
training.
3.
Tipping hazard—do not
drive on slopes greater than
21 degrees.
5.
Warning—do not park on
slopes; 1) Engage the
parking brake, 2) Lower the
cutting units, 3) Shut off the
engine, 4) Remove the key,
5) Leave the machine.
7.
Entanglement hazard,
belt—keep away from
moving parts; keep all
guards and shields in place.
2.
Warning—read the
Operator’s Manual
for
information on towing.
4.
Keep the cutting units
lowered while driving down
slopes; always wear a seat
belt when operating the
machine.
6.
Thrown object
hazard—keep bystanders
away from the machine.
10