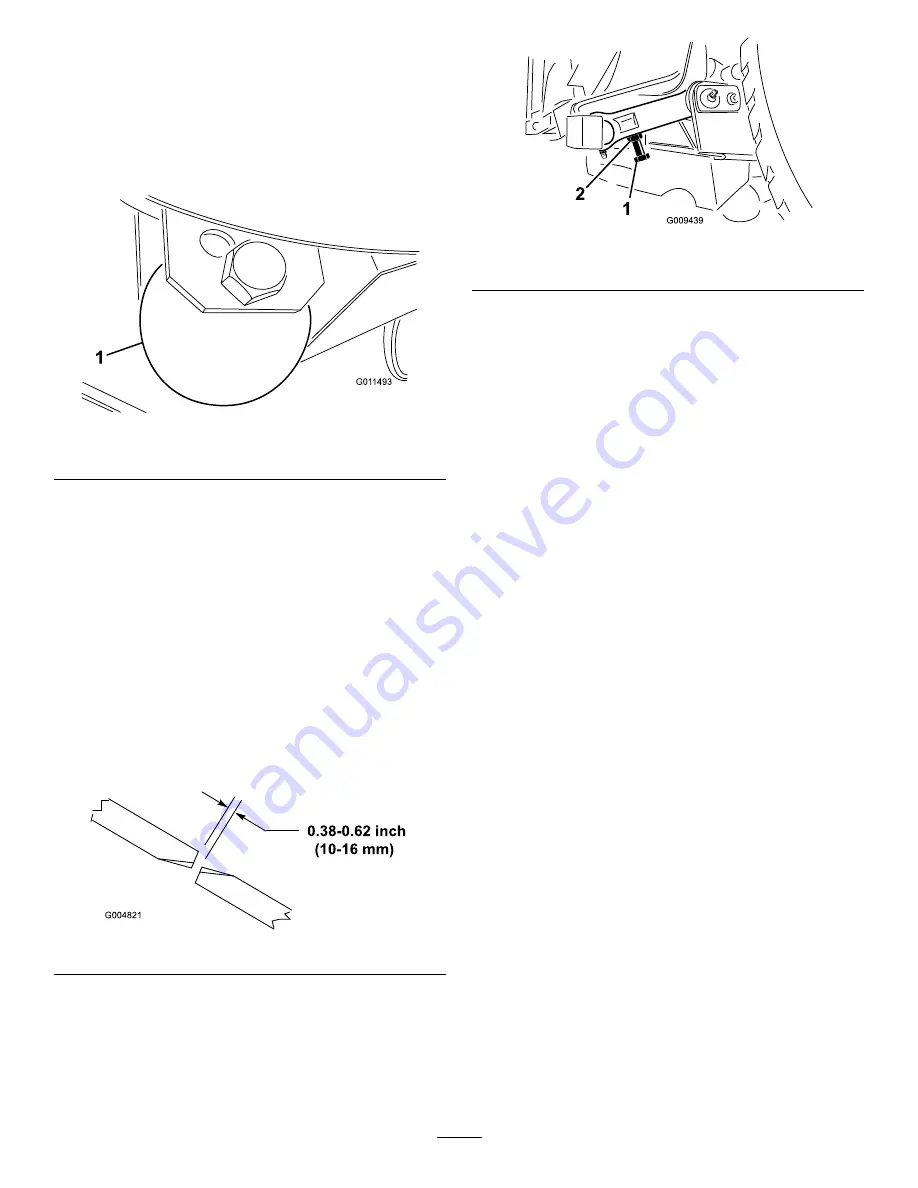
Adjusting the Cutting Unit Rollers
The cutting unit rollers should be mounted in the lower
position when operating in height of cuts greater than 2-1/2
inches (64 mm) and in the higher position when operating in
height of cuts lower than 2-1/2 inches (64 mm).
1.
Remove the bolt and nut securing the gage wheel to
the cutting unit brackets (Figure 25).
Figure 25
1.
Gage wheel
2.
Align the roller and spacer with the top holes in the
brackets and secure them with the bolt and nut.
Adjusting the Blade
To ensure proper operation of the cutting unit, there must be
0.38-0.62 inch (10-16 mm) clearance between the tips of the
wing and center cutting unit blades (Figure 26).
1.
Raise cutting unit so blades are visible and block center
deck section so it cannot fall accidentally. Wing decks
must be horizontal to center cutting unit.
2.
Rotate a center and adjoining wing blade so there blade
tips are aligned. Measure distance between blade tips,
distance should be approximately 0.38-0.62 inch (10-16
mm) (Figure 26).
Figure 26
3.
To adjust distance, locate adjuster bolt on rear pivot
link of cutting unit (Figure 27). Loosen jam nut on
adjuster bolt. Loosen or tighten adjuster bolts until
0.38-0.62 inch (10-16 mm) clearance is attained, then
tighten jam nut.
4.
Repeat procedure on opposite side of cutting deck.
Figure 27
1.
Adjuster bolt
2.
Jam nut
Correcting Mismatch Between Cutting
Units
Due to differences in grass conditions and the counterbalance
setting of the traction unit, it is advised that a sample area of
grass be cut and appearance checked before formal cutting
is started.
1.
Set all cutting units to the desired height of cut; refer to
Adjusting the Height of Cut.
2.
Check and adjust front and rear tractor tire pressure to
25-30 psi (172-207 kPa).
3.
Check and adjust all castor tire pressures to 50 psi (345
kPa).
4.
Check charge and counterbalance pressures with
engine at high idle using test ports defined in Hydraulic
Systems Test Ports. Adjust counterbalance setting to be
230 psi (1585 kPa) higher than charge pressure reading.
5.
Check for bent blades; refer to Checking for a Bent
Blade.
6.
Cut grass in a test area to determine if all cutting units
are cutting at the same height.
7.
If cutting unit adjustments are still needed, find a flat
surface using a 6 foot (2 m) or longer straight edge.
8.
To ease measuring blade plane, raise the height of cut
to the highest position; refer to Adjusting the Height
of Cut.
9.
Lower cutting units onto the flat surface. Remove the
covers from the top of the cutting units.
10.
Loosen the flange nut, securing the idler pulley, to
release the belt tension on each cutting unit.
Center Cutting Unit Setup
Rotate blade on each spindle until the ends face forward and
backward. Measure from the floor to the front tip of the
cutting edge. Adjust 1/8 inch shims on front castor fork(s) to
match height of cut to decal (Figure 28); refer to Adjusting
the Cutting Unit Pitch.
25
Summary of Contents for 30447N
Page 57: ...Schematics g014815 Electrical Schematic Rev D 57...
Page 58: ...g017775 Electrical Schematic Rev D 58...
Page 59: ...g017776 Electrical Schematic Rev D 59...
Page 60: ...g017779 Electrical Schematic GM 4000 4100 Rev D 60...
Page 61: ...g017780 Electrical Schematic GM 4010 Rev D 61...
Page 62: ...g017781 Electrical Schematic GM 4110 Rev D 62...
Page 63: ...g017782 Electrical Schematic GM 4010 Rev D 63...
Page 64: ...g017783 Electrical Schematic GM 4110 Rev D 64...
Page 65: ...g017784 Electrical Schematic GM 4110 Cab Rev D 65...
Page 66: ...g017785 Electrical Schematic GM 4110 Cab Rev D 66...
Page 67: ...Hydraulic Schematic Rev B 67...