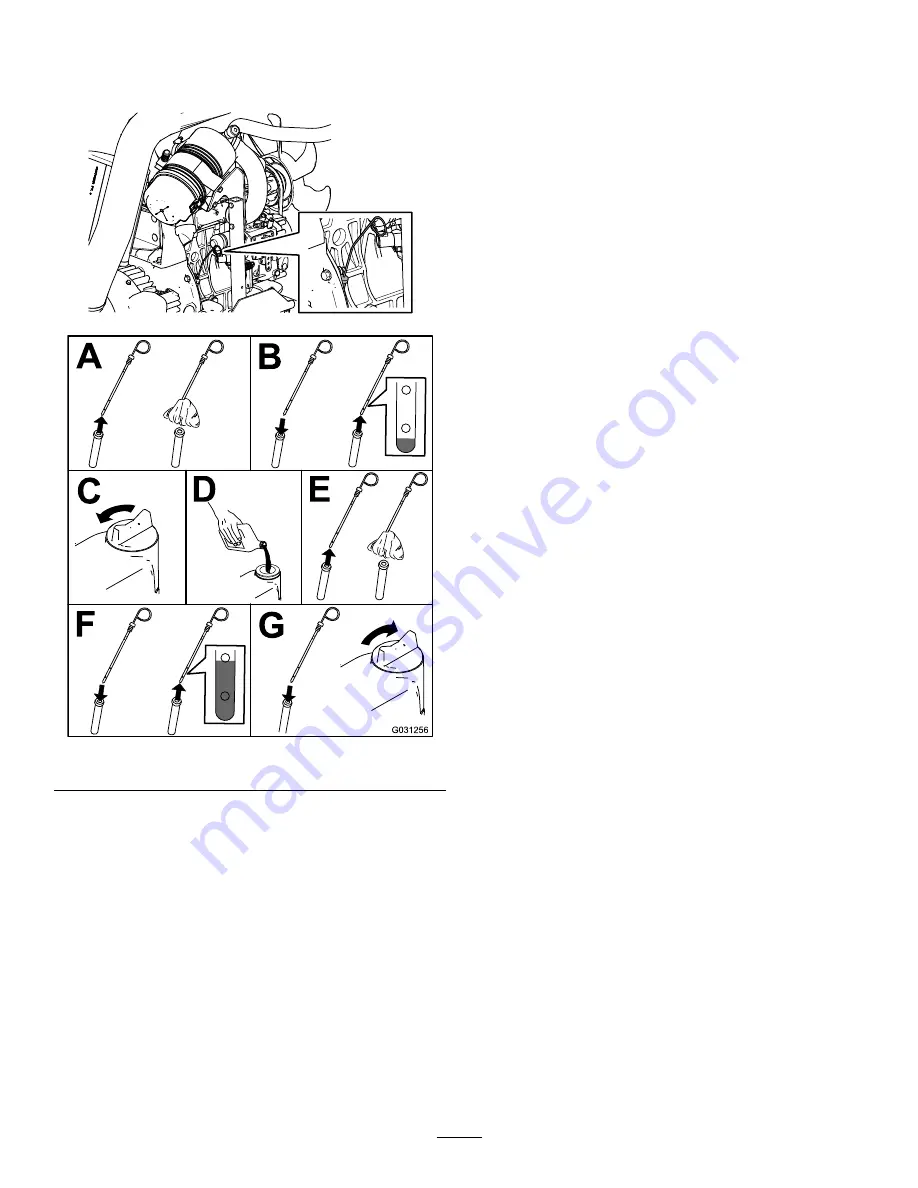
2.
Open the hood; refer to
Opening the Hood (page
.
3.
Check the level of the engine oil (
g378928
g031256
Figure 82
Important:
Be sure to keep the level of
the engine oil between the upper and lower
limits on the oil gauge. Engine failure may
occur because of over filling or under filling
the engine oil.
4.
Close and latch the hood; refer to
.
Crankcase Oil Capacity
Approximately 3.3 L (3.5 US qt) with the filter.
Changing the Engine Oil
and Filter
Service Interval:
After the first 50 hours—Change
the engine oil and filter.
Every 150 hours
1.
Prepare the machine; refer to
Maintenance (page 43)
.
2.
Drain the oil and change the filter.
51