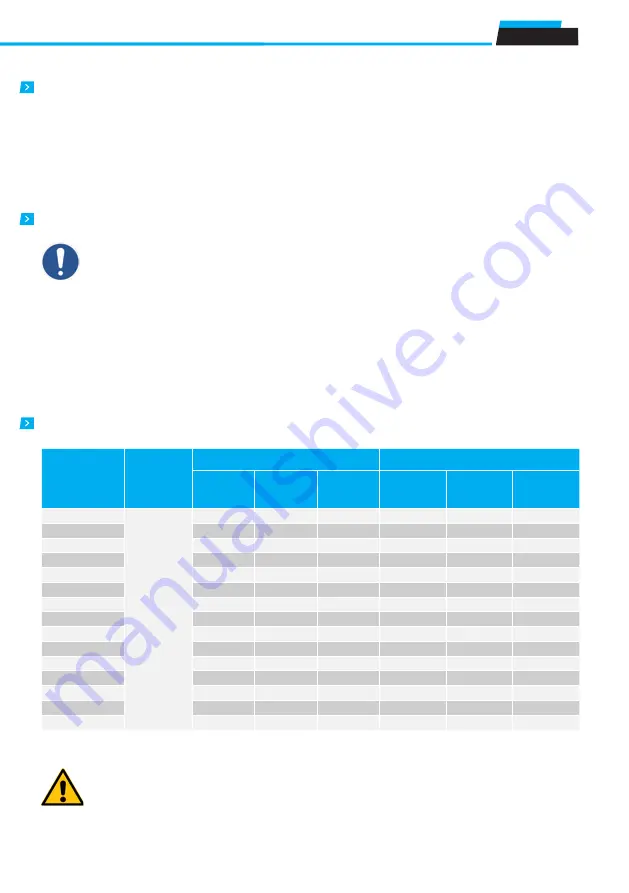
Tecline
UM-5
The Partly Completed Machinery shown in this catalog is to be
considered a mere supply of simple Cartesian axes and their ac-
cessories agreed when the contract is stipulated with the client. The
following are therefore to be considered excluded from the contract:
1. Assembly on the client’s premises (direct or final)
2. Commissioning on the client’s premises (direct or final)
3. Testing on the client’s premises (direct or final)
It is therefore understood that the aforementioned operations
in points 1.,2., and 3. are not chargeable to Rollon. Rollon is the
supplier of Partly Completed Machinery, the (direct or final) client
• Mechanical risks due to the presence of moving elements (X, Y axes).
• Risk of fire resulting from the flammability of the belts used on the axes,
for temperatures in excess of 250 °C in contact with the flame.
• The risk of the Z axis dropping during handling and installation
operations on the partly completed machinery, before commissioning.
• Risk of the Z axis dropping during maintenance operations in the case
All the screws belong to the UNI-3740. Locking assemblies are provided with class 12.9 fastening screws.
Basic components
Residual risks
Tightening torque and traction vector values
Thread
Friction
coefficient
Tightening torque [Nm]
Traction vector [Nm]
Resistance
grade
8,8
Resistance
grade
10,9
Resistance
grade
12,9
Resistance
grade
8,8
Resistance
grade
10,8
Resistance
grade
12,8
M3
0,15
1,21
1,21
2,09
2075
3048
3567
M4
2,78
4,09
4,79
3594
5279
6178
M5
5,5
8,1
9,5
5886
8645
10116
M6
9,5
14,0
16,4
8302
12194
14269
M8
23
34
40
15242
22388
226498
M10
46
67
79
24275
35655
41724
M12
79
116
136
35401
51995
60845
M14
127
187
219
46816
71408
83563
M16
1998
291
341
66955
98340
115079
M18
283
402
471
8346
119454
139787
M20
402
570
667
107941
153657
179811
M22
552
783
917
134806
192157
224865
M24
691
981
1148
155489
221266
258928
M27
1022
1452
1700
204577
291534
341157
M30
1387
1969
2305
248811
354209
414500
is responsible for testing and safely checking all equipment whi-
ch, by definition, cannot be theoretically tested or checked at our
facilities where the only movement possible is manual movement
(for example: motors or reduction gears, cartesian axes movements
that are not manually operated, safety brakes, stopper cylinders,
mechanical or induction sensors, decelerators, mechanical limit
switches, pneumatic cylinders, etc.). The partly completed machine
must not be commissioned until the final machine, in which it is to
be incorporated, has been declared compliant, if necessary, with the
instructions in Machinery Directive 2006/42/CE.
IMPORTANT!
All screws used for installing ROLLON modules have self-
locking washers or semi-permanent threadlock fluid (blue,
such as Loctite 243). We recommend that the user also
employ these devices, both while setting up the partially
assembled machine in this manual, and during the assembly
or maintenance phases: If this is not done, the manufacturer
of the partially assembled machine declines all responsibility
for any accidents, breakage, damage and the consequences
of said events on people, animals and property, due to the
failure of fixing elements.
of a drop in the electrical power supply voltage.
• Crushing hazard near moving parts with divergent and convergent
motion.
• Shearing hazard near moving parts with divergent and convergent
motion.
• Cutting and abrasion hazards.