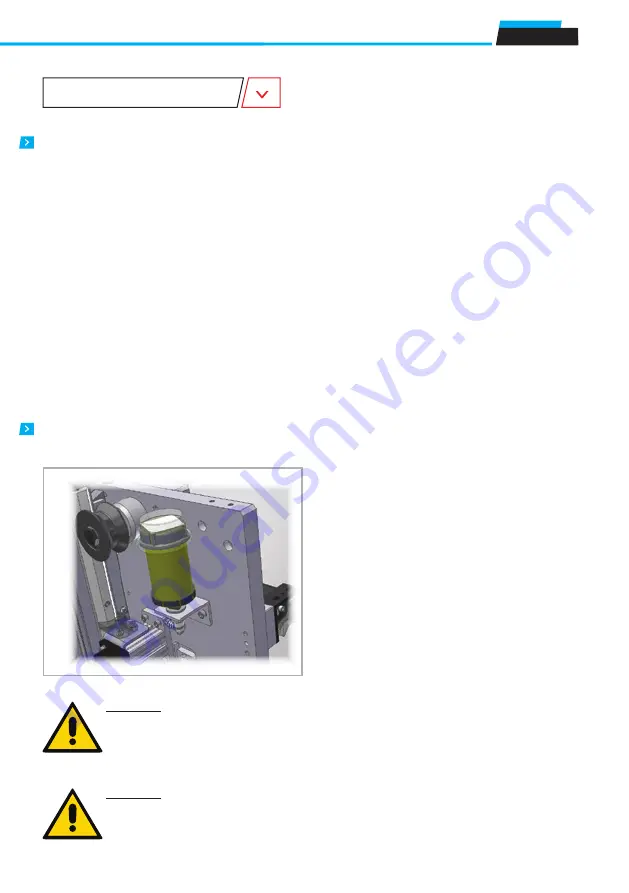
Tecline
UM-13
The scraper with felt (PAR axes) requires no special main-
tenance, it is sufficient its replacement every 12, 24 or 36
months according to the specific case. However, depending
on the dynamics incurred by the system, it may be necessary
to maintain the surface of the prismatic steel guides slightly
moistened, injecting into the scraper with felt cm
3
of grease
such as “Purpose”, consistency 2, every 500 hours or 10,000
km of operation.
The guides for the recirculating ball slides (PAS axes) must not
be lubricated. Provide greasing the slides for every 500 hours
or 10,000 km of operation, using grease
ranging between ISO VG 68 and ISO VG-100. In the case of
high loads must be used grease type ISO VG 220.
Automatic rack lubrication
Rack lubrication is provided by an automatic greasing system
(optional), which can be operated by an on/off switch located
in the rear part of the lubrication unit: this unit comprises a
replaceable cartridge, a pinion made form Vulkollan and ad-
justable lubrication frequency, depending on the particular
dynamic requirements.
Manual greasing and lubrication
For both PAR and PAS axes, never lubricate bearings type
2RS wherever they are present: the pressure exerted during
the operation would get the side seals out of seat. For axes
equipped with “Rod Locking” safety system unit, never lubri-
cate the sliding calibrated bar.
ATTENTION!
For instructions on routine and special maintenance and for the safety informations about the automatic
greasing system of the rack, refer to the specific manual assembly of the accessory in question.
ATTENTION!
The lubricator cartridge unit must be replaced before having completely run out,
otherwise abnormal consumption of the pinion or the rack may occur.
Routine maintenance