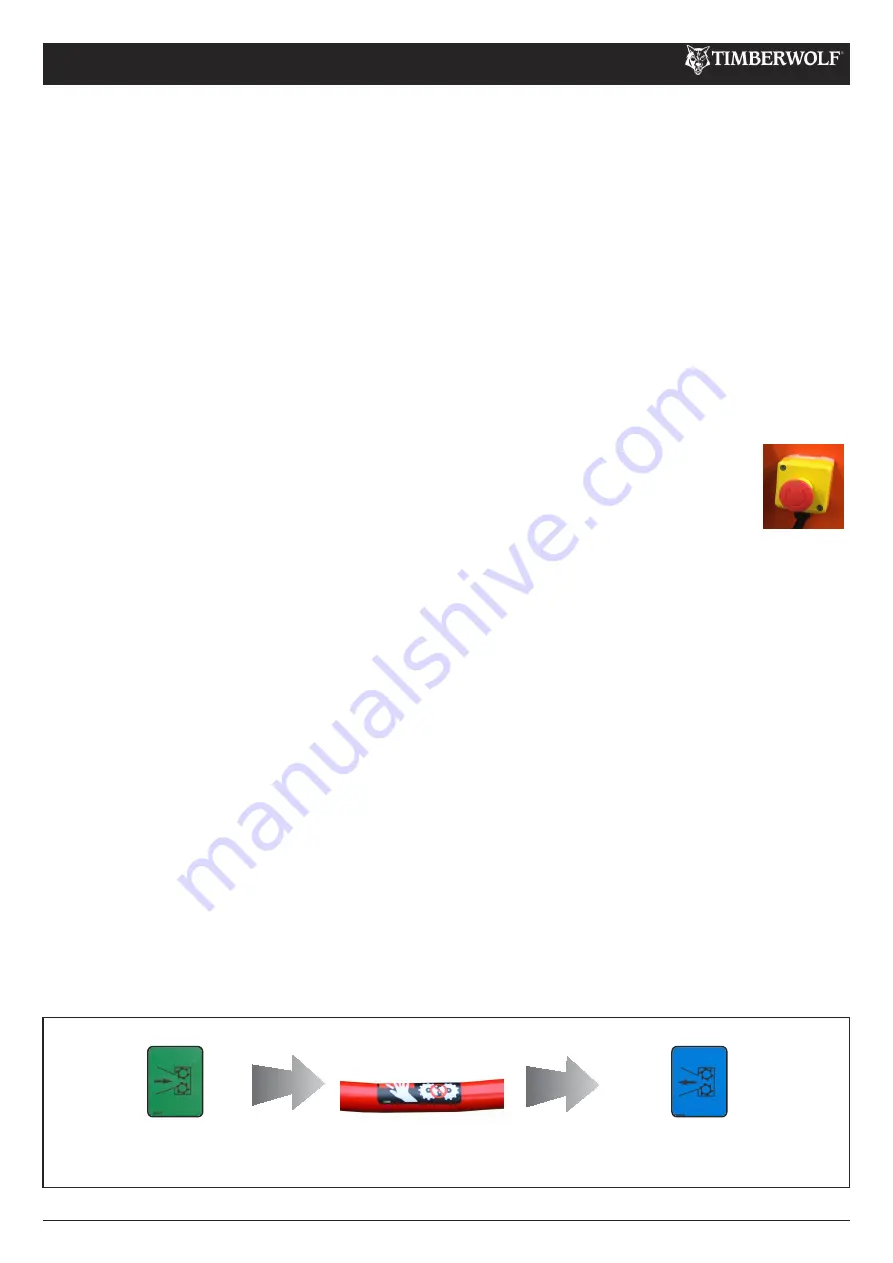
TW 280TDHB/(a)
11 / 65
OPERATING INSTRUCTIONS
C190-0142
01.03.2019
Rev: 2.0
AUTO CONTROLS
The no stress control unit controls the feed rate of the material going into the chipping chamber. If the engine speed is
below the predetermined level, the no stress unit will not allow the feed rollers to work in the forward “infeed” direction,
until the rotor speed rises above the predetermined level. At this point, the feed rollers will start turning without warning.
The reverse function will work at any engine speed.
EMERGENCY STOPPING
There are two ways of stopping the TW 280TDHB/(a) chipper in the event of an emergency.
Stopping the rollers
Activating the
red safety bar
will stop the rollers immediately. The rotor will still be turning, the engine must be powered
down to stop the rotor. Turn off the engine ignition key. To restart the rollers, just push the
green forward
or
blue reverse
feed control.
Stopping the engine
: Should the engine need to be stopped in an emergency, the
engine stop switch
on top of the engine
bay should be pushed. This will shut down the engine in the shortest possible time. The engine cannot be restarted until
the engine stop switch is pulled out and the main ignition switch is turned off to reset the machine.
Stopping the rollers and the engine:
Should the entire machine need to be stopped in an emergency, activate
one of the
red emergency stop
buttons positioned on top of the funnel or on either sides of the feed tray.
This function kills all power to both the engine and the rollers, bringing the machine to a complete stop. The
engine cannot be restarted until the button is restored to its original position and the main ignition switch is
turned off to reset the machine. Before disengaging the emergency stop button, inspect the machinery to
determine the reason for activation.
ENGINE CONTROLS
The engine controls are in two locations. The engine ignition is on the control panel in the centre of the machine and the
throttle lever is mounted on the feed funnel.
LOCATE the machine on firm level ground.
•
CHECK the machine is well supported and cannot move.
•
CHECK the jack stand is lowered and secure.
•
CHECK all guards are fitted and secure.
•
CHECK the discharge unit is in place and fastened
•
securely.
CHECK the discharge tube is pointing in a safe direction.
•
CHECK the feed funnel to ensure no objects are inside.
•
CHECK the feed tray is in up position - to prevent people
•
reaching rollers.
CHECK the controls as described below.
•
CHECK (visually) for fluid leaks.
•
CHECK fuel and hydraulic oil levels.
•
If still hitched, ensure tow vehicle is isolated prior to
•
operation of the chipper.
For parts location see diagrams on pages 4 - 5.
DAILY CHECKS BEFORE STARTING
BEFORE USING THE CHIPPER
3
1
PRESS THE GREEN FEED CONTROL
THE IN-FEED SHOULD TURN
FORWARDS
PRESS THE RED SAFETY
BAR
THE IN-FEED SHOULD STOP
PRESS THE BLUE FEED CONTROL
THE IN-FEED SHOULD TURN BACKWARDS ONLY
WHILE THE FEED CONTROL IS PRESSED
WITH THE ENGINE RUNNING AT FULL SPEED
2
It is essential to carry out the following tests to check safety equipment - this sequence of tests will only take a few seconds
to carry out. We recommend that these tests are carried out daily. Observing the function as described will confirm that
the safety circuits are working correctly. This is also a good opportunity to remind all operators of the control and
emergency stop systems.
Summary of Contents for TW 280TDHB
Page 1: ...timberwolf uk com TW 280TDHB a BROYEUR MANUELOP RATEUR TRADUCTIONDUMODED EMPLOID ORIGINE...
Page 26: ...TW 280TDHB a 24 65 PLAQUES D IDENTIFICATION C190 0144 FR 01 03 2019 Rev 2 0 EXEM PLE...
Page 29: ...TW 280TDHB a 27 65 LOCALISATION DES PI CES LECTRIQUES C190 0144 FR 01 03 2019 Rev 2 0...
Page 31: ...29 65 SCH MA DE CIRCUIT C190 0144 FR 01 03 2019 Rev 2 0 TW 280TDHB a P 2741 plus C161 0106...
Page 37: ...timberwolf uk com TW 280TDHB a WOOD CHIPPER UKINSTRUCTION MANUAL ORIGINALINSTRUCTIONS...
Page 62: ...TW 280TDHB a 24 65 IDENTIFICATION PLATE C190 0142 01 03 2019 Rev 2 0 EXAM PLE...
Page 65: ...TW 280TDHB a 27 65 ELECTRICAL PARTS LOCATOR C190 0142 01 03 2019 Rev 2 0...
Page 80: ...TW 280TDHB a 42 65 C190 0141 13 08 2019 Rev 2 0...
Page 81: ...43 65 C190 0141 13 08 2019 Rev 2 0 TW 280TDHB a...
Page 82: ...TW 280TDHB a 44 65 C190 0141 13 08 2019 Rev 2 0...
Page 83: ...TW 280TDHB a 45 65 C190 0141 13 08 2019 Rev 2 0...
Page 86: ...TW 280TDHB a 48 65 C190 0141 13 08 2019 Rev 2 0...
Page 87: ...TW 280TDHB a 49 65 C190 0141 13 08 2019 Rev 2 0...
Page 88: ...TW 280TDHB a 50 65 C190 0141 13 08 2019 Rev 2 0...
Page 89: ...TW 280TDHB a 51 65 C190 0141 13 08 2019 Rev 2 0...
Page 90: ...TW 280TDHB a 52 65 C190 0141 13 08 2019 Rev 2 0 Kit No P2821...
Page 91: ...TW 280TDHB a 53 65 C190 0141 13 08 2019 Rev 2 0...
Page 92: ...TW 280TDHB a 54 65 C190 0141 13 08 2019 Rev 2 0...
Page 93: ...TW 280TDHB a 55 65 C190 0141 13 08 2019 Rev 2 0...
Page 94: ...TW 280TDHB a 56 65 C190 0141 13 08 2019 Rev 2 0...
Page 95: ...TW 280TDHB a 57 65 C190 0141 13 08 2019 Rev 2 0...
Page 96: ...58 65 C190 0141 13 08 2019 Rev 2 0 TW 280TDHB a Hydraulic oil lter FL100...
Page 97: ...59 65 C190 0141 13 08 2019 Rev 2 0 TW 280TDHB a...
Page 98: ...60 65 C190 0141 13 08 2019 Rev 2 0 TW 280TDHB a...
Page 99: ...61 65 C190 0141 13 08 2019 Rev 2 0 TW 280TDHB a...
Page 100: ...62 65 C190 0141 13 08 2019 Rev 2 0 TW 280TDHB a...
Page 101: ...63 65 C190 0141 13 08 2019 Rev 2 0 TW 280TDHB a...