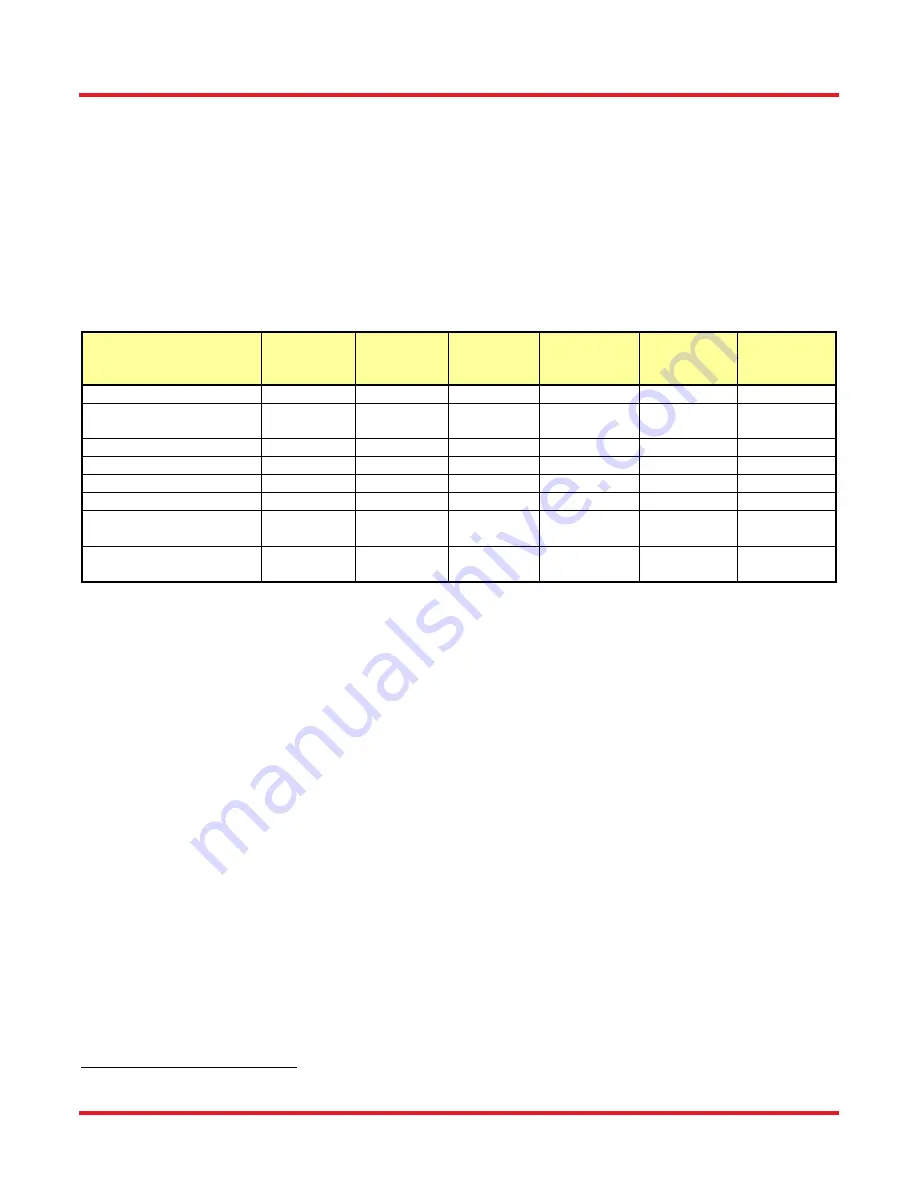
PTR306 / PTR306B Recoaters with Linear Proof Testers
Chapter 8: Maintenance
Page 26
TTN090913-D02
Chapter 8
Maintenance
The purpose of the maintenance section is to define the planned maintenance requirements of the PTR306 and
PTR306B. Where appropriate maintenance procedures are included.
8.1. Planned Maintenance
The device is designed for a production environment to give trouble free operation provided normal planned
maintenance is adhered to. Maintenance and repair procedures should only be performed by trained personnel.
Improper service and/or repair could result in the safety features being disabled and can also lead to damage that
will not be covered under warranty.
Planned Maintenance Schedule
Maintenance
Every
Cycle
Every
Shift
Daily
Monthly
3 Months 6 Months
Check Mold
1
Check/Clean Fiber
Holding Block Inserts
1
Check UV Lamps
1
Run Purge (5 Cycles)
Replace UV Lamps
2
Flush Recoat System
Replace Recoat
Material
Check Proof Test
Calibration/Recalibrate
8.2. Cleaning
Clean Mold
Keeping the mold plates clean is vitally important for proper recoat performance and quality. The mold plates should
be cleaned of dirt, dust or excessive recoat material before each use. Clean the mold plates only with a soft cotton
swab soaked in cleaning solution. Acetone is the preferred solution for cleaning the mold plates. Acetone cleans
more thoroughly than alcohol and will also soften and lift away any cured recoat material. Do not use excessive
scrubbing or scraping action to clean the plates. Give the cleaning solution time (60 s- 90 s) to soften and lift any
cured material. Excessive cleaning can shorten the life of the mold through damage to the coatings on the mold
plates or chipping of the mold channel.
To dispose of acrylate material safely, place in a plastic bag and then close the plastic bag with a knot before placing
in the garbage. Alternatively, expose the material to sunlight for four hours and then throw in the garbage.
Check/Clean FHB Inserts
The fiber holding block inserts have a rubber insert that grips the fiber for proof testing. These should be checked
for damage and cleanliness prior to each shift. If the rubber insert is damaged or dirty, the fiber may slip prior to
reaching the maximum proof test level. If required, clean the rubber insert with a cotton swab or lens tissue soaked
in isopropyl alcohol. If rubber insert is damaged it should be replaced.
Note
: Do not use acetone to clean the rubber inserts. Repeated cleaning with acetone will damage the rubber.
Note
: Do not clean the insert with alcohol when the unit is turned ON. The alcohol could be drawn into the vacuum
system, causing damage.
1
Maintenance operations can be performed by the operator
2
Lamp replacement based schedule is based on 2,000 recoats/month at 15 s/recoat.
Summary of Contents for PTR306
Page 1: ...PTR306 PTR306B Manual Fiber Recoater with Linear Proof Tester User Guide...
Page 39: ...PTR306 PTR306B Recoaters with Linear Proof Testers Chapter 10 Appendix Page 36 TTN090913 D02...
Page 41: ...PTR306 PTR306B Recoaters with Linear Proof Testers Chapter 10 Appendix Page 38 TTN090913 D02...
Page 43: ...PTR306 PTR306B Recoaters with Linear Proof Testers Chapter 10 Appendix Page 40 TTN090913 D02...
Page 48: ...www thorlabs com...