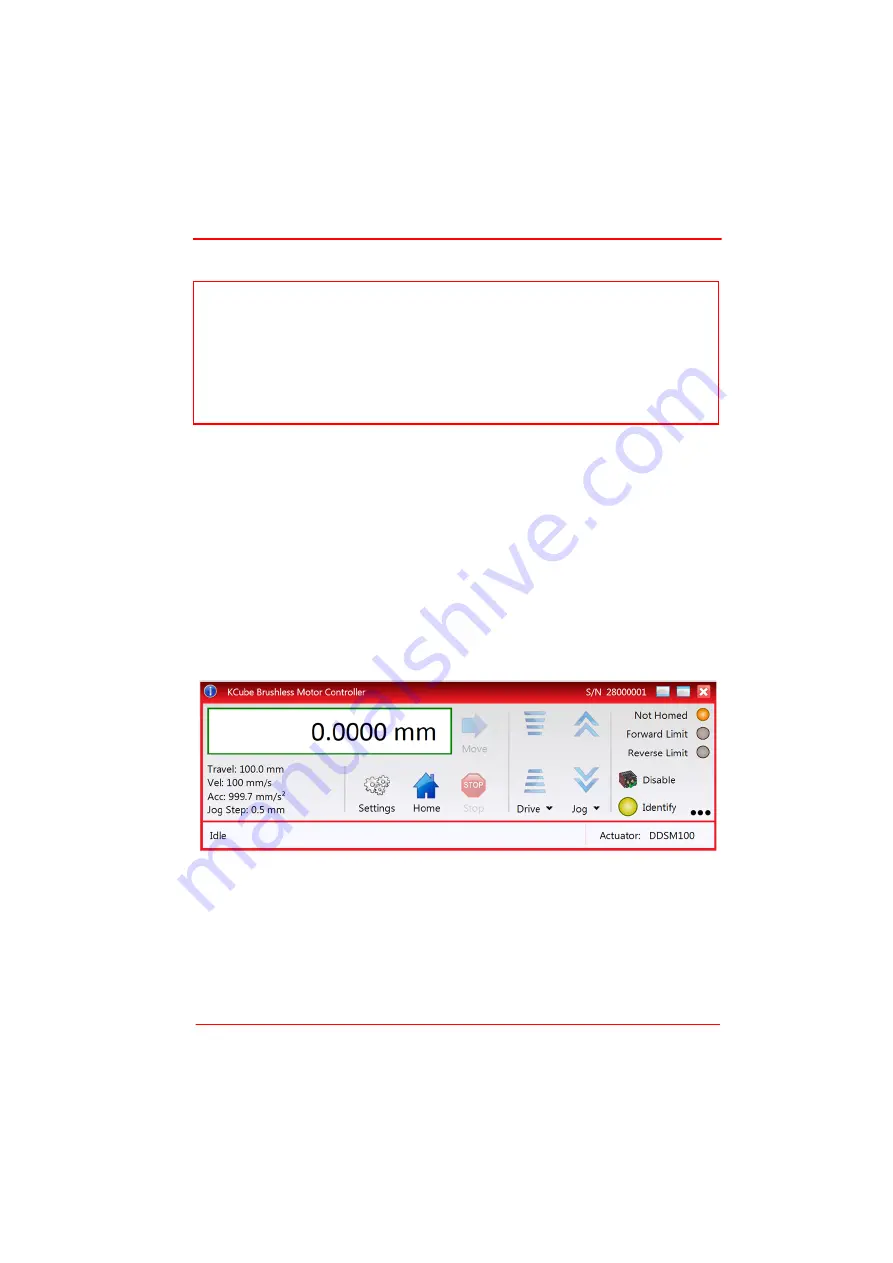
Rev G Apr 2019
Page 9
Chapter 4 Operation
5) The stage can now be moved using the Pot, GUI panel, or by setting commands
to move each axis by relative and absolute amounts – see the handbook supplied
with the KBD101 controller, and the helpfile supplied with the software for more
information
6) The stage is shipped already loaded with default parameter settings, which should
give satisfactory performance in most cases. However, depending on the
application, it may be necessary to adjust the PID loop parameter settings to fine
tune the response - see the following pages for more information.
4.2 Using the Kinesis software
1) If it is not already running, start the Kinesis software - Start/Programs/Thorlabs/
Kinesis/Kinesis
The software reads in the stage and controller information on boot up and the GUI
panel shown below is displayed..
Fig. 4.1 Kinesis GUI screen
Note
The need for homing comes from the fact that on power up the motor (stage) is at a
random position, so the value of the position counter is meaningless. Homing
involves moving the motor to a known reference marker and resetting the position
counter to the associated absolute value. This reference marker can be one of the
limit switches or can be provided by some other signal. The DDSM series stages use
an electronic reference marker and therefore the limit switches are not used for
reference.