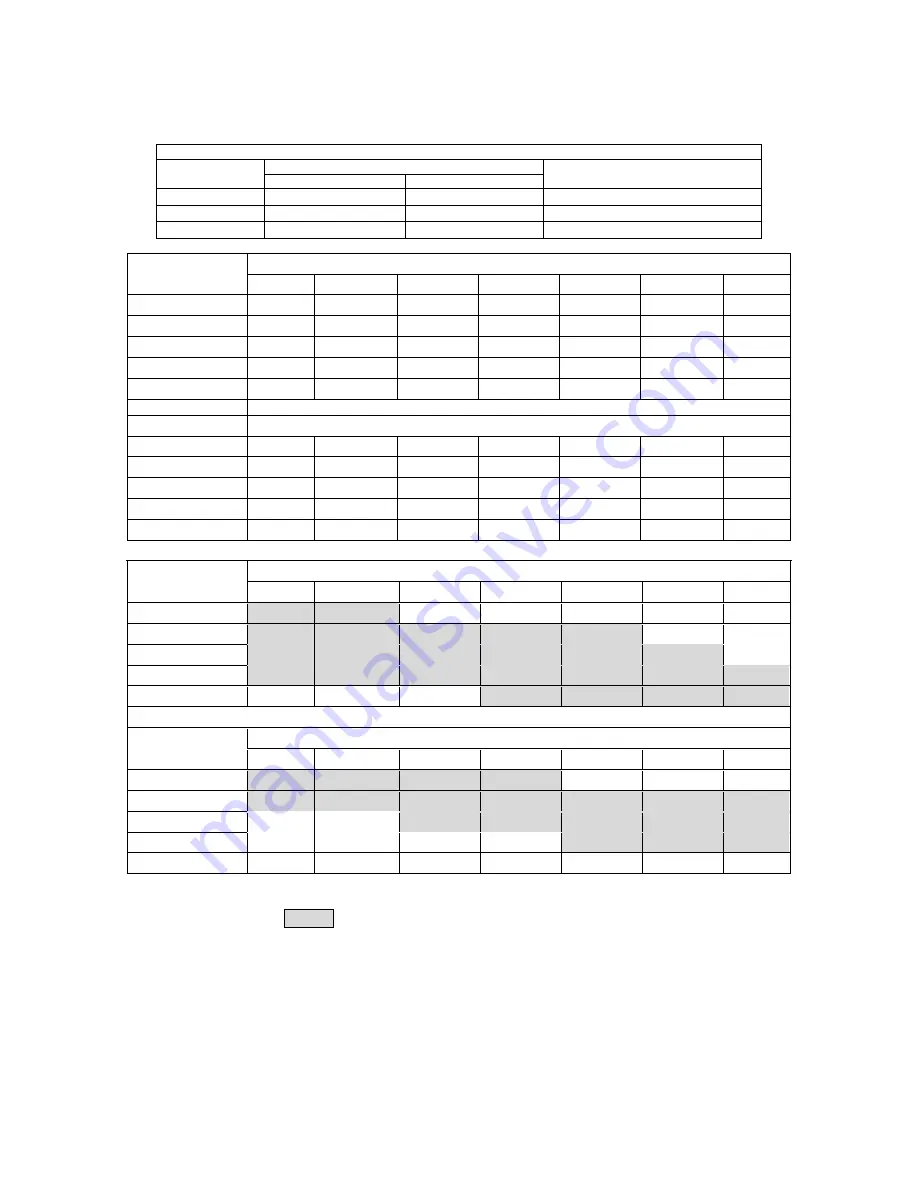
All installations and services must be performed by qualified service personnel.
28
OME-72T36
ALTERATIONS REQ’D FOR A/C @ DESIGN EXTERNAL STATIC PRESSURE
COOLING UNIT
HTG Speed by Input
Recommended CLG Speed (Color)
Low fire
High Fire
24,000
Low
Med
Med / ML
30,000
Low
Med
MH
36,000
Low
Med
High
Speed Tap\ Static
Pressure
Furnace Airflow (CFM) vs. External Static pressure (in. WC.)
0.1
0.2
0.3
0.4
0.5
0.6
0.7
Low
873
807
746
677
602
531
448
ML
1024
975
916
863
812
739
671
MED
1081
1032
980
931
886
1823
757
MH
1175
1138
1091
1041
991
950
887
High
1360
1320
1279
1233
1189
1148
1107
Motor Current Draw (Amps/Watts) vs. External Static pressure (in. WC.)
Low
1.6/111
1.6/116
1.7/121
1.7/126
1.8/130
1.8/135
1.9/141
ML
2.2/166
2.3/172
2.3/178
2.4/183
2.5/189
2.5/195
2.6/200
MED
2.5/193
2.6/200
2.7/206
2.7/212
2.8/217
2.9/224
2.9/230
MH
3.1/246
3.2/250
3.8/257
3.3/263
3.4/269
3.5/275
3.5/282
High
4.4/366
4.5/372
4.5/373
4.6/383
4.7/390
4.7/397
4.8/404
Speed Tap\ Static
Pressure
High Fire Temperature Rise vs. External Static pressure (in. WC.)
0.1
0.2
0.3
0.4
0.5
0.6
0.7
Low
78
84
91
100
112
128
151
ML
66
69
74
78
83
92
101
MED
63
66
69
73
76
82
89
MH
58
59
62
65
68
71
76
High
50
51
53
55
57
59
61
Speed Tap\ Static
Pressure
Low Fire Temperature Rise vs. External Static pressure (in. WC.)
0.1
0.2
0.3
0.4
0.5
0.6
0.7
Low
64
69
75
83
93
105
125
ML
55
57
61
65
69
76
83
MED
52
54
57
60
63
68
74
MH
47
49
51
54
56
59
63
High
41
42
44
45
47
49
50
=
Recommended operation range
Summary of Contents for OME-72D36
Page 2: ......
Page 7: ...All installations and services must be performed by qualified service personnel 4a...
Page 21: ...All installations and services must be performed by qualified service personnel 18 Figure 6...
Page 34: ...All installations and services must be performed by qualified service personnel 31...
Page 53: ...All installations and services must be performed by qualified service personnel 50...
Page 54: ...All installations and services must be performed by qualified service personnel 51...
Page 55: ......