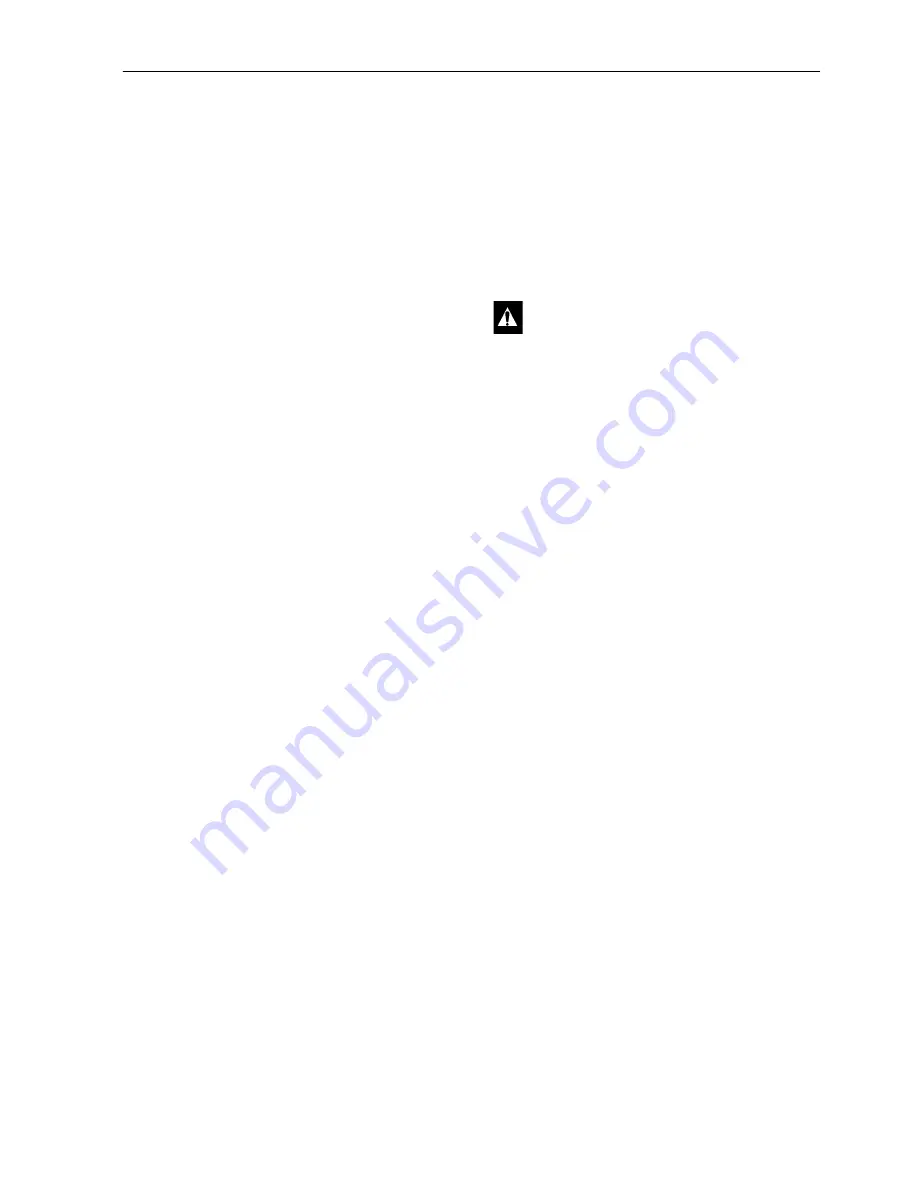
Operating Instructions
49
Engine Low Oil Pressure Cutout:
The engine low
oil pressure cutout is a pressure sensitive switch
located in the engine oiling system. This switch
will trip the Engine Reset and stop the engine if
the oil pressure drops below 8 to 12 psi
(55 to 83 kPa).
Refrigerant High Pressure Cutout:
The high
pressure cutout is a pressure sensitive switch
located in the compressor head. If the refrigerant
discharge pressure exceeds the current setting,
this switch opens the circuit to the fuel solenoid,
stopping the engine. Within 30 to 50 seconds, the
engine reset will also trip because of no oil
pressure in the engine. For Model 50 units, this
switch also shuts down electric motor operation.
Refrigerant High Pressure Relief Valve:
This valve
is designed to relieve excess pressure within the
refrigeration system. Located on a high pressure
line near the condenser, it is non-repairable and
requires no adjustment. When pressure is released
from the valve, it is directed away from anyone
servicing the unit.
Preheat Buzzer (CYCLE-SENTRY Units):
The
preheat buzzer sounds when the
CYCLE-SENTRY system causes the glow plugs
to preheat.
Unit Operation
Pretrip Inspection
Pretrip inspections are a very important part of
regularly scheduled preventive maintenance
programs designed to minimize operating
problems and breakdowns before they happen.
While pretrips are not intended to take the place
of regular maintenance inspections, the following
suggested pretrip inspection should be performed
before every trip involving refrigerated cargo.
Fuel:
The diesel fuel supply must be adequate to
guarantee the operation of the engine to at least
the next check point.
Engine Oil:
The engine oil level should be at the
FULL mark on the dipstick. Never overfill.
Coolant:
Check coolant level gauge for the correct
amount of coolant. The indicator should be in the
FULL (white) range. If the coolant level is in the
ADD (red) range, add coolant to the expansion
tank. The coolant should be a 50/50 mixture of
ethylene glycol and water and provide protection
to -30 F (-34 C).
Battery:
The terminals must be tight and free of all
corrosion. Electrolyte should be at full mark.
Belts:
The belts must be in good condition and
adjusted to the proper tension. Allow 1/2 inch
(13 mm) deflection at the center of the span
between pulleys.
Electrical:
Check all electrical connections to
make certain they are securely fastened. Wires
and terminals should be free of corrosion, cracks
or moisture.
Structural:
Visually inspect the unit for leaks,
loose or broken parts and other damage.
Gasket:
The unit mounting gasket should be
tightly compressed and in good condition.
Coils:
The condenser and evaporator coils should
be clean and free of debris.
Cargo Box:
Inspect the interior and exterior of the
box for damage. Any damage to the walls or
insulation must be repaired.
Defrost Drain:
Check the defrost drain hoses and
fittings to be sure they are open.
Doors:
Be sure doors and weather seals are in
good condition, door latches securely and weather
seals fit tightly.
CAUTION: Do not remove the expansion
tank cap while the coolant is hot.
Summary of Contents for 920000
Page 4: ......
Page 10: ...Table of Contents 10...
Page 22: ...Specifications 22...
Page 41: ...Unit Description 41 Unit Photographs Figure 12 Front View Figure 13 Top View ARD026 AGA267...
Page 42: ...Unit Description 42 Figure 14 Engine Side Door Open ARD041...
Page 76: ...Electrical Maintenance 76...
Page 132: ...Hilliard Clutch Maintenance 132...
Page 134: ...Structural Maintenance 134...
Page 146: ...Refrigeration Diagnosis 146...
Page 148: ...Remote Evaporator Specifications 148...
Page 150: ...Remote Evaporator Maintenance Inspection Schedule 150...
Page 154: ...Remote Evaporator Unit Description 154...
Page 158: ...Remote Evaporator Structural Maintenance 158...
Page 160: ...Remote Evaporator System Diagnosis 160...
Page 164: ...Wiring and Schematic Diagrams Index 164...
Page 165: ...165 MD RD MT Model 30 w In Cab Schematic Diagram Page 1 of 2...
Page 166: ...166 MD RD MT Model 30 w In Cab Schematic Diagram Page 2 of 2...
Page 167: ...167 MD RD MT Model 30 w In Cab Wiring Diagram Page 1 of 3...
Page 168: ...168 MD RD MT Model 30 w In Cab Wiring Diagram Page 2 of 3...
Page 169: ...169 MD RD MT Model 30 w In Cab Wiring Diagram Page 3 of 3...
Page 170: ...170 MD RD MT Model 30 w In Cab CYCLE SENTRY Schematic Diagram Page 1 of 2...
Page 171: ...171 MD RD MT Model 30 w In Cab CYCLE SENTRY Schematic Diagram Page 2 of 2...
Page 172: ...172 MD RD MT Model 30 w In Cab CYCLE SENTRY Wiring Diagram Page 1 of 3...
Page 173: ...173 MD RD MT Model 30 w In Cab CYCLE SENTRY Wiring Diagram Page 2 of 3...
Page 174: ...174 MD RD MT Model 30 w In Cab CYCLE SENTRY Wiring Diagram Page 3 of 3...
Page 175: ...175 MD RD MT Model 30 CYCLE SENTRY Wiring Diagram Page 1 of 3...
Page 176: ...176 MD RD MT Model 30 CYCLE SENTRY Wiring Diagram Page 2 of 3...
Page 177: ...177 MD RD MT Model 30 CYCLE SENTRY Wiring Diagram Page 3 of 3...
Page 178: ...178 MD RD MT Model 50 w In Cab Schematic Diagram Page 1 of 2...
Page 179: ...179 MD RD MT Model 50 w In Cab Schematic Diagram Page 2 of 2...
Page 180: ...180 MD RD MT Model 50 w In Cab Wiring Diagram Page 1 of 3...
Page 181: ...181 MD RD MT Model 50 w In Cab Wiring Diagram Page 2 of 3...
Page 182: ...182 MD RD MT Model 50 w In Cab Wiring Diagram Page 3 of 3...
Page 183: ...183 MD RD MT Model 50 w In Cab CYCLE SENTRY Schematic Diagram Page 1 of 2...
Page 184: ...184 MD RD MT Model 50 w In Cab CYCLE SENTRY Schematic Diagram Page 2 of 2...
Page 185: ...185 MD RD MT Model 50 w In Cab CYCLE SENTRY Wiring Diagram Page 1 of 3...
Page 186: ...186 MD RD MT Model 50 w In Cab CYCLE SENTRY Wiring Diagram Page 2 of 3...
Page 187: ...187 MD RD MT Model 50 w In Cab CYCLE SENTRY Wiring Diagram Page 3 of 3...
Page 188: ...188 MD RD MT Model 50 CYCLE SENTRY Wiring Diagram Page 1 of 3...
Page 189: ...189 MD RD MT Model 50 CYCLE SENTRY Wiring Diagram Page 2 of 3...
Page 190: ...190 MD RD MT Model 50 CYCLE SENTRY Wiring Diagram Page 3 of 3...