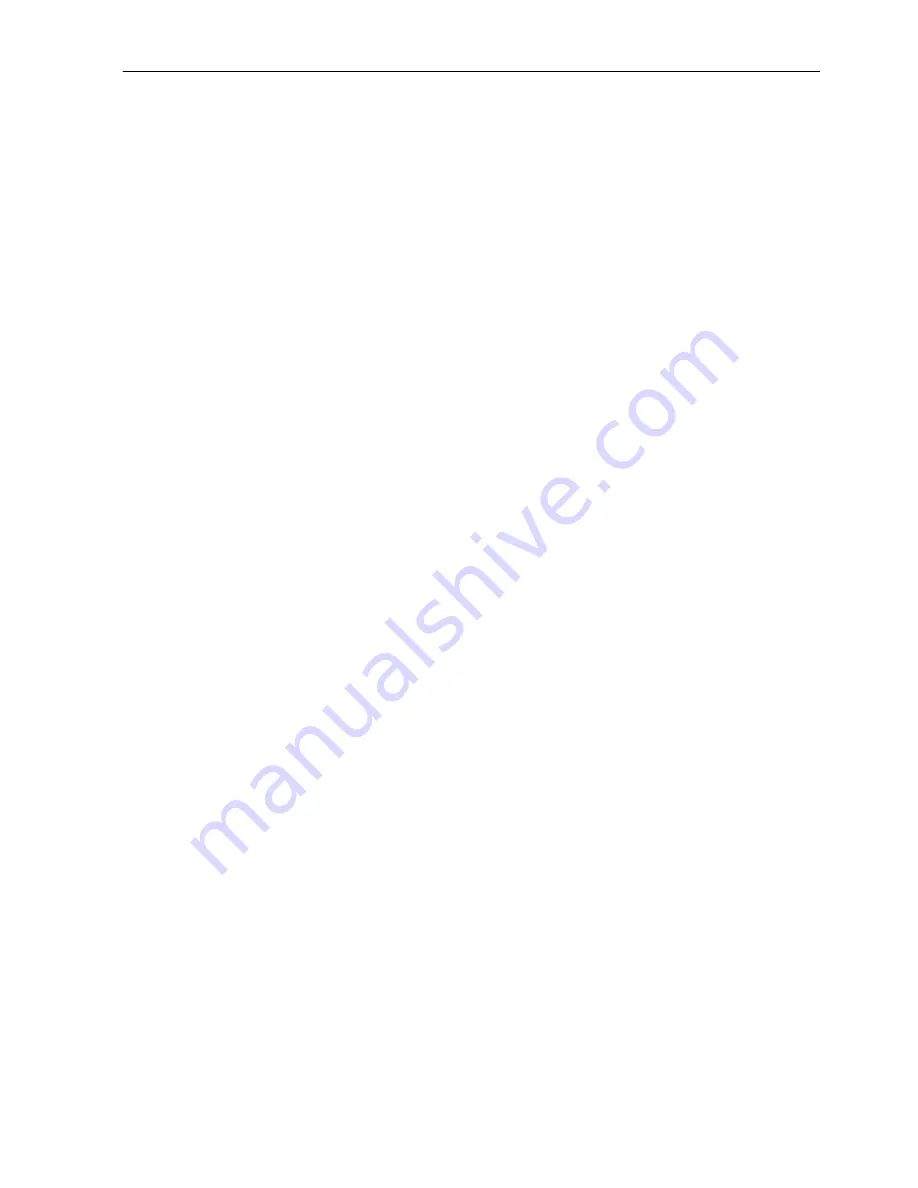
Safety Precautions
15
Welding of Units or Truck Bodies
When electric welding is to be performed on any
portion of the temperature control unit, truck or
truck chassis when the temperature control unit is
attached, it is necessary to ensure that welding
currents are not allowed to flow through the
electronic circuits of the unit.
These procedures must be rigidly adhered to when
servicing units to avoid damage or destruction of
the controller.
1. Disconnect all power to the unit.
2. Disconnect all wire harnesses from the
controller.
3. Switch all of the electrical circuit breakers in
the control box to the Off position.
4. Weld unit or container per normal welding
procedures. Keep ground return electrode as
close to the area to be welded as practical.
This will reduce the likelihood of stray
welding currents passing through any
electrical or electronic circuits.
5. When the welding operation is completed, the
unit power cables, wiring and circuit breakers
must be restored to their normal condition.
High Voltage
When servicing or repairing a temperature control
unit, the possibility of serious or even fatal injury
from electrical shock exists. Extreme care must be
used when working with a refrigeration unit that
is connected to a source of operating power, even
if the unit is not operating. Lethal voltage
potentials can exist at the unit power cord, inside
the control box, at the motors and within the
wiring harnesses.
Precautions
1. Be certain the Unit On/Off switch is turned
Off before connecting or disconnecting the
standby power plug. Never attempt to stop the
unit by disconnecting the power plug.
2. Be certain the unit power plug is clean and dry
before connecting it to a power source.
3. When working on high voltage circuits on the
temperature control unit, do not make any
rapid moves. If a tool drops, do not grab for it.
People do not contact high voltage wires on
purpose. It occurs from an unplanned
movement.
4. Use tools with insulated handles that are in
good condition. Never hold metal tools in
your hand if exposed, energized conductors
are within reach.
5. Treat all wires and connections as high
voltage until a meter and wiring diagram show
otherwise.
6. Never work alone on high voltage circuits on
the temperature control unit. Another person
should always be present to shut off the
temperature control unit and to provide aid in
the event of an accident.
7. Have electrically insulated gloves, cable
cutters and safety glasses available in the
immediate vicinity in the event of an accident.
First Aid
Immediate action must be initiated after a person
has received an electrical shock. Obtain
immediate medical assistance if available.
The source of shock must be immediately
removed by either shutting down the power or
removing the victim from the source. If it is not
possible to shut off the power, the wire should be
cut with either an insulated instrument (e.g., a
wooden handled axe or cable cutters with heavy
insulated handles) or by a rescuer wearing
electrically insulated gloves and safety glasses.
Whichever method is used do not look at the wire
while it is being cut. The ensuing flash can cause
burns and blindness.
Summary of Contents for 920000
Page 4: ......
Page 10: ...Table of Contents 10...
Page 22: ...Specifications 22...
Page 41: ...Unit Description 41 Unit Photographs Figure 12 Front View Figure 13 Top View ARD026 AGA267...
Page 42: ...Unit Description 42 Figure 14 Engine Side Door Open ARD041...
Page 76: ...Electrical Maintenance 76...
Page 132: ...Hilliard Clutch Maintenance 132...
Page 134: ...Structural Maintenance 134...
Page 146: ...Refrigeration Diagnosis 146...
Page 148: ...Remote Evaporator Specifications 148...
Page 150: ...Remote Evaporator Maintenance Inspection Schedule 150...
Page 154: ...Remote Evaporator Unit Description 154...
Page 158: ...Remote Evaporator Structural Maintenance 158...
Page 160: ...Remote Evaporator System Diagnosis 160...
Page 164: ...Wiring and Schematic Diagrams Index 164...
Page 165: ...165 MD RD MT Model 30 w In Cab Schematic Diagram Page 1 of 2...
Page 166: ...166 MD RD MT Model 30 w In Cab Schematic Diagram Page 2 of 2...
Page 167: ...167 MD RD MT Model 30 w In Cab Wiring Diagram Page 1 of 3...
Page 168: ...168 MD RD MT Model 30 w In Cab Wiring Diagram Page 2 of 3...
Page 169: ...169 MD RD MT Model 30 w In Cab Wiring Diagram Page 3 of 3...
Page 170: ...170 MD RD MT Model 30 w In Cab CYCLE SENTRY Schematic Diagram Page 1 of 2...
Page 171: ...171 MD RD MT Model 30 w In Cab CYCLE SENTRY Schematic Diagram Page 2 of 2...
Page 172: ...172 MD RD MT Model 30 w In Cab CYCLE SENTRY Wiring Diagram Page 1 of 3...
Page 173: ...173 MD RD MT Model 30 w In Cab CYCLE SENTRY Wiring Diagram Page 2 of 3...
Page 174: ...174 MD RD MT Model 30 w In Cab CYCLE SENTRY Wiring Diagram Page 3 of 3...
Page 175: ...175 MD RD MT Model 30 CYCLE SENTRY Wiring Diagram Page 1 of 3...
Page 176: ...176 MD RD MT Model 30 CYCLE SENTRY Wiring Diagram Page 2 of 3...
Page 177: ...177 MD RD MT Model 30 CYCLE SENTRY Wiring Diagram Page 3 of 3...
Page 178: ...178 MD RD MT Model 50 w In Cab Schematic Diagram Page 1 of 2...
Page 179: ...179 MD RD MT Model 50 w In Cab Schematic Diagram Page 2 of 2...
Page 180: ...180 MD RD MT Model 50 w In Cab Wiring Diagram Page 1 of 3...
Page 181: ...181 MD RD MT Model 50 w In Cab Wiring Diagram Page 2 of 3...
Page 182: ...182 MD RD MT Model 50 w In Cab Wiring Diagram Page 3 of 3...
Page 183: ...183 MD RD MT Model 50 w In Cab CYCLE SENTRY Schematic Diagram Page 1 of 2...
Page 184: ...184 MD RD MT Model 50 w In Cab CYCLE SENTRY Schematic Diagram Page 2 of 2...
Page 185: ...185 MD RD MT Model 50 w In Cab CYCLE SENTRY Wiring Diagram Page 1 of 3...
Page 186: ...186 MD RD MT Model 50 w In Cab CYCLE SENTRY Wiring Diagram Page 2 of 3...
Page 187: ...187 MD RD MT Model 50 w In Cab CYCLE SENTRY Wiring Diagram Page 3 of 3...
Page 188: ...188 MD RD MT Model 50 CYCLE SENTRY Wiring Diagram Page 1 of 3...
Page 189: ...189 MD RD MT Model 50 CYCLE SENTRY Wiring Diagram Page 2 of 3...
Page 190: ...190 MD RD MT Model 50 CYCLE SENTRY Wiring Diagram Page 3 of 3...