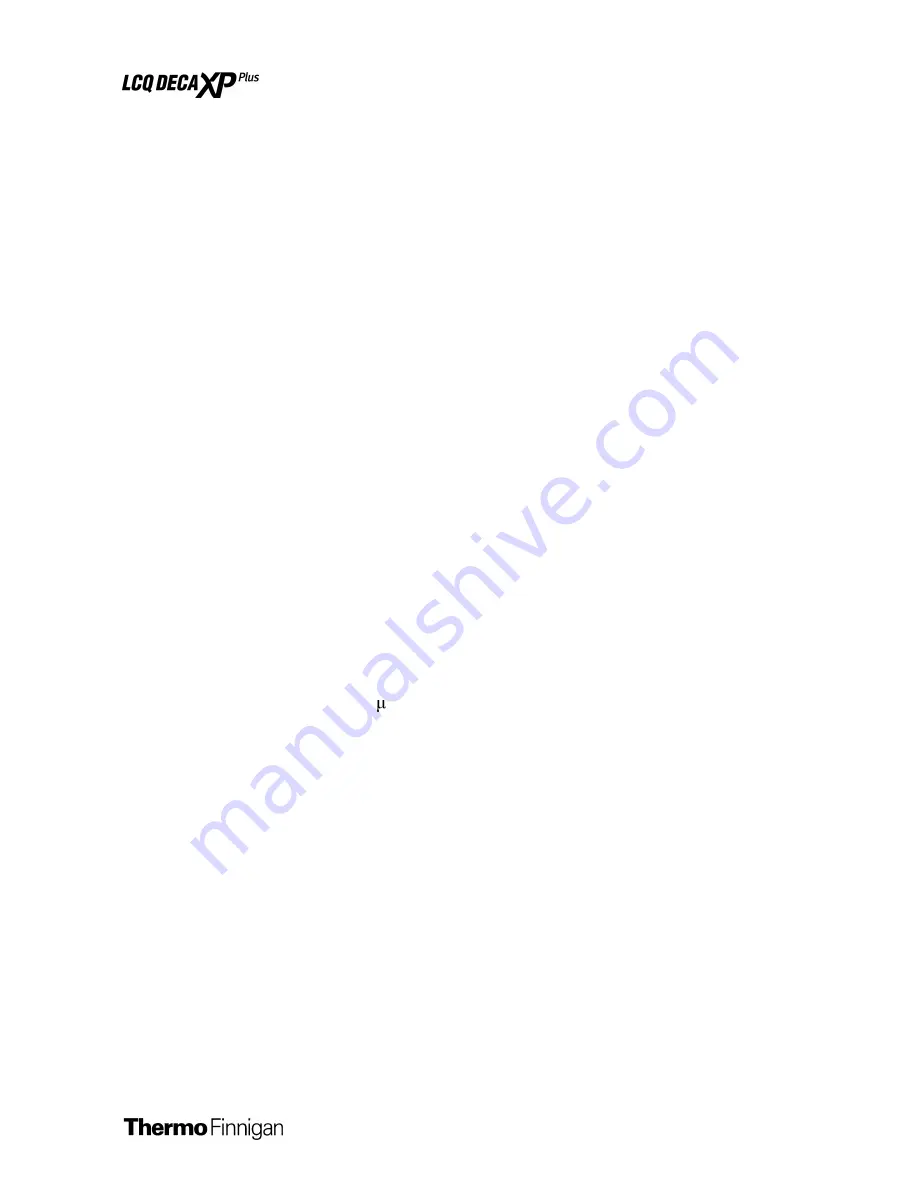
User Maintenance
______________________________________________________ API Source Maintenance
__________________ LCQ Deca XP Plus Hardware Manual __________________
4-7
To flush the sample transfer line, sample tube, and API probe, proceed as
follows:
1. Make sure that the API flange is secured to the spray shield by the two
flange retainer bolts.
2. Choose
Start | Programs | Xcalibur | LCQ Tune
to open the Tune
Plus window.
3. From the Tune Plus window, choose
Control | On
(or click on the
On/Standby button) to turn on the voltages and gas flows to the API
source.
•
If you are operating in APCI mode, go to step 4.
•
If you are operating in ESI mode, go to step 5.
4. Set up the APCI source as follows:
a.
Ensure that the auxiliary gas line is connected to the A port on the
APCI probe.
b. In the Tune Plus window, choose
Setup | APCI Source
(or click on
the APCI Source button). The APCI Source dialog box appears.
c.
In the APCI Source dialog box, use the Vaporizer Temp spin box to
set the vaporizer temperature to 500 °C.
d. Use the Sheath Gas Flow Rate spin box to set the sheath gas flow rate
to 80 units.
e.
Use the Aux Flow Rate spin box to set the auxiliary gas flow rate to
10 units.
f.
Use the
'LVFKDUJH&XUUHQWVSLQER[WRVHWWKHGLVFKDUJHFXUUHQWWR
$
g. Click on
OK
to set the APCI parameters and close the dialog box.
h. Go to step 6.
5. Set up the ESI source as follows:
a.
Ensure that the auxiliary gas line is connected to the Aux port on the
ESI probe.
b. In the Tune Plus window, choose
Setup | ESI Source
(or click on
the ESI Source button). The ESI Source dialog box appears.
c.
Use the Sheath Gas Flow Rate spin box to set the sheath gas flow rate
to 80 units.
d. Use the Aux Flow Rate spin box to set the auxiliary gas flow rate to
10 units.
e.
Use the Spray Voltage spin box to set the spray voltage to 0 kV.
f.
Click on
OK
to set the ESI parameters and close the dialog box.
Summary of Contents for LCQ Deca XP Plus
Page 1: ...LCQ Deca XP Plus Hardware Manual Revision A 97344 97003 TM ...
Page 46: ......
Page 56: ......
Page 70: ......
Page 114: ...INSERT Figure5_2 ps 11 X 17 Z fold Figure 5 2 Mass analyzer and ion optics ...
Page 172: ......
Page 194: ......
Page 216: ......