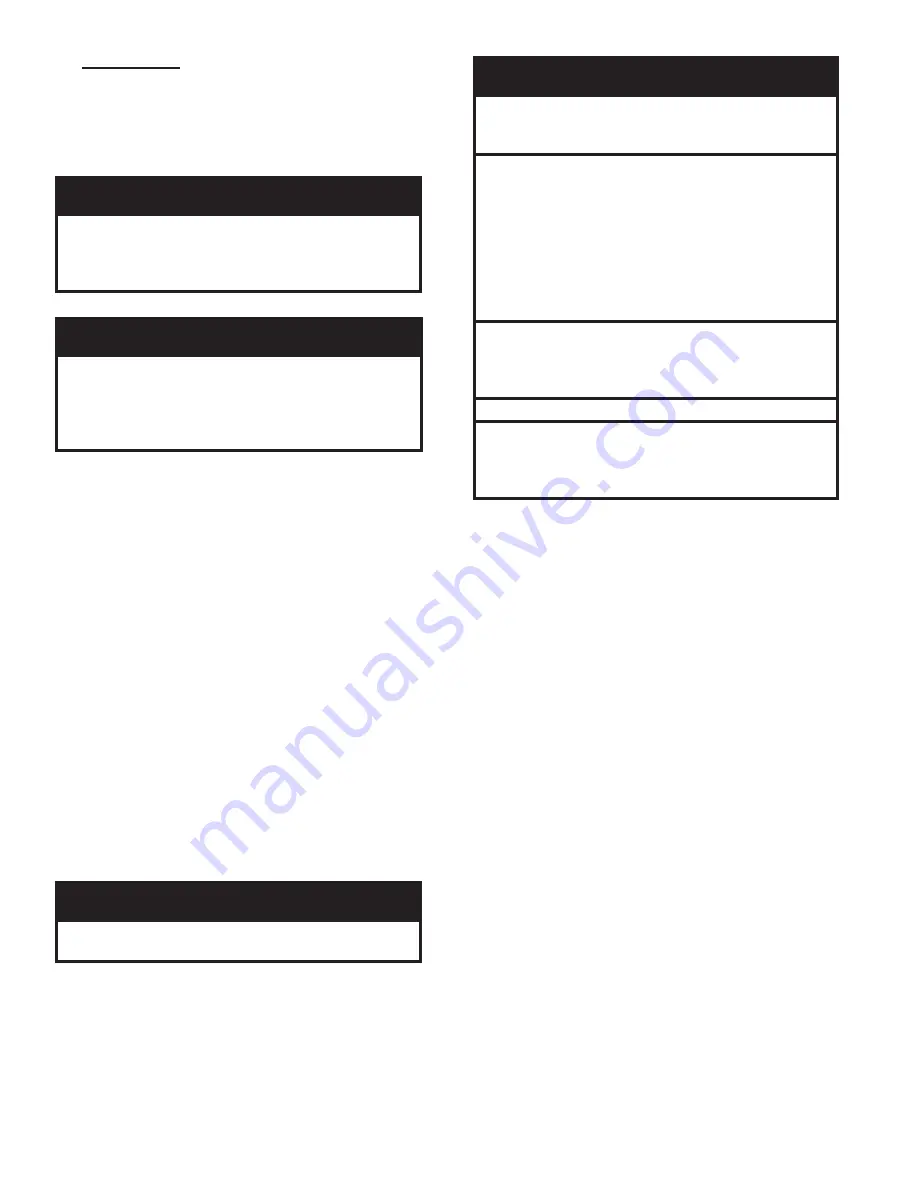
24
F.
ELECTRICAL
1. General. Install wiring and ground boiler in
accordance with authority having jurisdiction or in
absence of such requirements National Electrical
Code, ANSI/NFPA 70 and/or CSA C22.1 Electrical
Code.
WARNING
Failure to properly wire electrical connections to
the boiler may result in serious physical harm.
DO NOT ATTACH ADDITIONAL J-Box to back or
top of boiler jacket.
DANGER
Positively assure all electrical connections are
unpowered before attempting installation or
service of electrical components or connections
of the boiler or building. Lock out all electrical
boxes with padlock once power is turned off.
2. A separate electrical circuit must be run from
the main electrical service with an over-current
device/disconnect in the circuit. A service switch
is recommended and may be required by some
local jurisdictions. Locate the service switch such
that the appliance can be shut off without exposing
personnel to danger in the event of an emergency.
3. Connect the main power supply and ground from
fused disconnect to proper boiler electrical leads
located in the junction box at the rear of the boiler.
Refer to electrical consumption plate on boiler
jacket.
4. Protection for the factory installed circulator is
provided by the factory. Install a separate fused
disconnect switch for each additional circulator
installed (i.e. boiler and system circulators).
5. Connect field supplied safety limits or devices
using proper terminals provided in boiler electrical
cabinet. Refer to wiring diagram supplied with
boiler for wiring information. Refer to Figures 9a -
9f for typical wiring diagrams. Refer to Figure 1, for
electrical requirements for boiler.
CAUTION
Each boiler must be protected with a dedicated
properly sized fused disconnect.
WARNING
Electrical power may be supplied from more than
one service. Make sure all power is off before
attempting any electrical work.
The wiring diagrams contained in this manual are
for reference purposes only. Each boiler may be
wired differently according to the specifications
given to Thermal Solutions at the time the boiler
was purchased. Always use the wiring diagram
provided with the boiler. If the wiring diagram
provided with the boiler is unavailable, STOP all
wiring work and contact Thermal Solutions for a
replacement diagram.
Do not directly connect low voltage (24 volt,
milliamp, etc.) controls to this boiler. If low
voltage controls are desired, isolating relays
must be used.
Never jump out any safety controls.
Never jump out or make inoperative any safety
or operating controls. Each boiler must be
protected with a properly sized over-circuit
device.
6. The following pages have sample wiring diagrams.
Contact Thermal Solutions Representative or visit
website (www.thermalsolutions.com) for current
wiring options.
7. An as-built wiring diagram is included with every
boiler when it ships.
Summary of Contents for EVCA SERIES
Page 14: ...14 Figure 4 Typical Vertical Pressurized Venting ...
Page 16: ...16 Figure 6 Vertical Air Intake Piping Figure 5 Horizontal Air Intake Piping ...
Page 19: ...19 Figure 8 Schematic Boiler Piping ...
Page 25: ...25 Figure 9a 208 230 480V 1PH 3PH 60HZ Supply Power Wiring Schematic ...
Page 26: ...26 Figure 9b 120V 1PH 60HZ Supply Power Wiring Schematic ...
Page 27: ...27 Figure 9c Control Wiring Schematic EVCA 750 2000 ...
Page 29: ...29 Figure 9e Control Wiring Schematic EVCA 3000 ...
Page 32: ...32 Figure 10 Modular System Horizontal Air Intake Piping ...
Page 33: ...33 Figure 11 Modular System Vertical Air Intake Piping ...
Page 34: ...34 Figure 12 Modular System Typical One Pipe Water Piping ...
Page 35: ...35 Figure 13 Modular System Typical Primary Secondary Water Piping ...
Page 36: ...36 Figure 14 Modular System Typical Primary Secondary without System Pump ...
Page 37: ...37 Figure 15 Modular System Typical Reverse Return Water Piping ...
Page 38: ...38 Figure 16 Modular System Reverse Return with System Pump Only ...
Page 39: ...39 Figure 17 Modular System Typical Primary Secondary with Reverse Return ...
Page 55: ...55 Figure 18 Cleaning Secondary Heat Exchanger 1 2 ...
Page 56: ...56 This page intentionally left blank ...
Page 58: ...58 Figure 19 Boiler Combustion Chamber ...
Page 60: ...60 Figure 20 Burner Assembly FRONT VIEW TOP VIEW ...
Page 62: ...62 Figure 21a UL FM CSD 1 Main Gas Train Assembly EVCA 750 2000 ...
Page 64: ...64 Figure 21b UL FM CSD 1 Main Gas Train Assembly EVCA 3000 ...
Page 66: ...66 Figure 22a DB B Gas Train 750 Figure 22b DB B Gas Train 1000 2000 ...
Page 68: ...68 Figure 22c DB B w POC Gas Train 750 Figure 22d DB B w POC Gas Train 1000 2000 ...
Page 70: ...70 Figure 22e DB B Gas Train EVCA 3000 Figure 22f DB B w POC Gas Train EVCA 3000 ...
Page 72: ...72 Figure 23 Jacket ...
Page 74: ...74 Figure 24 EVCA 750 1000 and 1500 Secondary Heat Exchanger and Housing ...
Page 78: ...78 Figure 25b EVCA 3000 Secondary Heat Exchanger and Housing ...
Page 80: ...80 Figure 26 Control Panel Assembly ...
Page 82: ...82 Figure 27 Bishop Pilot Assembly ...
Page 97: ...97 NOTES ...
Page 98: ...98 NOTES ...
Page 99: ...99 NOTES ...