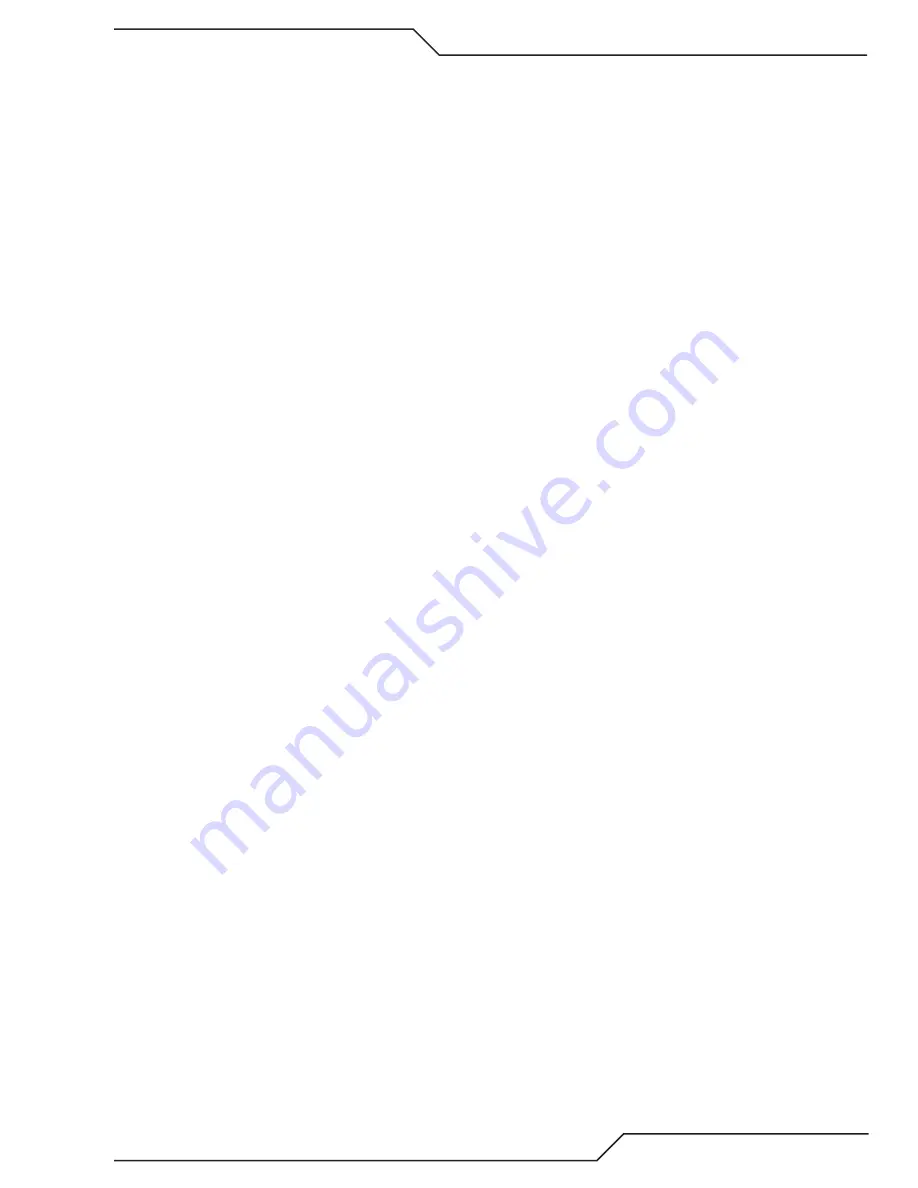
AUTO-CUT 300 XT
Manual 0-5300
APPENDIX
A-69
Turn the on the unit. You will have 4 minutes to perform the test/adjustment before the system times out with
a coolant flow fault. If that happens recycling the power gives you another 4 minutes.
1. The pressure on the gauge should be close to 173 (170-175) PSI. If it is the pump and the bypass are OK.
2. If the pressure is less than 173 PSI adjust the bypass screw clockwise to raise the pressure. If you can
change the pressure with the bypass screw but cannot reach 173 PSI it is likely the pump is worn out or
damaged. If the pressure does not change using the bypass screw it is likely the bypass is defective.
3. If the pressure is above 173 reduce the pressure by adjusting the bypass valve screw counter clockwise.
Coolant flow test:
In addition to the pressure test or in place of it if you don’t have a gauge, determine if the flow returning from
the torch (the flow that passes through the FS1), is greater than the required minimum. With the unit switched
off remove the return hose from the back of the power supply. Place it in a container of a known volume. Turn
the unit on and let the pump run exactly 30 seconds. It should pump at least 3/8 gal. (1.4 l). Use a larger con
-
tainer in case the flow is greater and it overflows.
If the flow is lower than 0.75 GPM:
• Look for restrictions such as sharp bends or something pinching the coolant hoses or torch leads.
• Other possibilities are the bypass valve has been adjusted wrong (someone may have turned the adjust
-
ment screw) see pressure test/adjustment above
• The pump is worn out (may be the case with an older unit).
Coolant flow is correct but system doesn’t detect it due to defective components:
• Defective or disconnected FS1 flow switch.
• Relay board.
• CCM.
Flow Switch FS1 disconnected – FS1 comes with wire about 1 ft. long and a connector that connects to a 3 wire
harness. This could be disconnected at either end, J74 or J5 on the relay board.
Defective FS1– The flow switch, normally open, closes when flow through it exceeds 0.75 GPM, could be open.
Easiest place to measure the switch is at the J5 harness connector that plugs into the Pilot board. Assuming you
have previously determined flow is sufficient, disconnect J5 from the Pilot board, start the unit so the coolant
is flowing and measure continuity between the 2 pins of J5.
• If there is no continuity either the switch is open or the harness between J5 and J74 at FS1 is open.
• If there is continuity between the J5 pins with sufficient coolant flow then either relay board or the CCM
is faulty.
• Relay board
• CCM
405
Low Coolant Level Warning
If the coolant level becomes low while cutting it is not necessary to immediately stop the cut as there is still
enough coolant to continue so we display E405 as a warning. Once the cut stops if the coolant is still low the
display changes to E401 and prevents starting another cut. Refer to the section for code 401 for troubleshooting.
406
Coolant Flow Low Warning
Ultra-Cut XT units, in addition to a coolant flow switch, include a turbine flow sensor FL1, referred to in the
plumbing diagram as a “bubble sensor”, with a pulse output that accurately measures coolant flow and in ad
-
dition can detect the presence of gas bubbles in the coolant. Gas bubbles from leaking seals in the torch or hose
fittings have been proven to reduce consumable life. This code is a warning, it does not prevent cutting but if
it persists the cause should be investigated.
Summary of Contents for AUTO-CUT 300 XT
Page 6: ...This Page Intentionally Blank...
Page 13: ...AUTO CUT 300 XT Manual 0 5300 SAFETY INSTRUCTIONS 1 5 This Page Intentionally Blank...
Page 52: ...This Page Intentionally Blank...
Page 105: ...AUTO CUT 300 XT Manual 0 5300 APPENDIX A 19 Display PCB Test Points TP1 GND TP2 5VDC TP3 24VDC...
Page 114: ...AUTO CUT 300 XT APPENDIX Manual 0 5300 APPENDIX 11 Cap Bias Bottom PCB Layout Art A 11685_AB...
Page 115: ...AUTO CUT 300 XT Manual 0 5300 APPENDIX A 29 APPENDIX 12 Cap Bias Top PCB Layout Art A 11686_AB...
Page 116: ...AUTO CUT 300 XT APPENDIX Manual 0 5300 APPENDIX 13 Suppressor PCB Layout Art A 11684_AB...
Page 161: ......