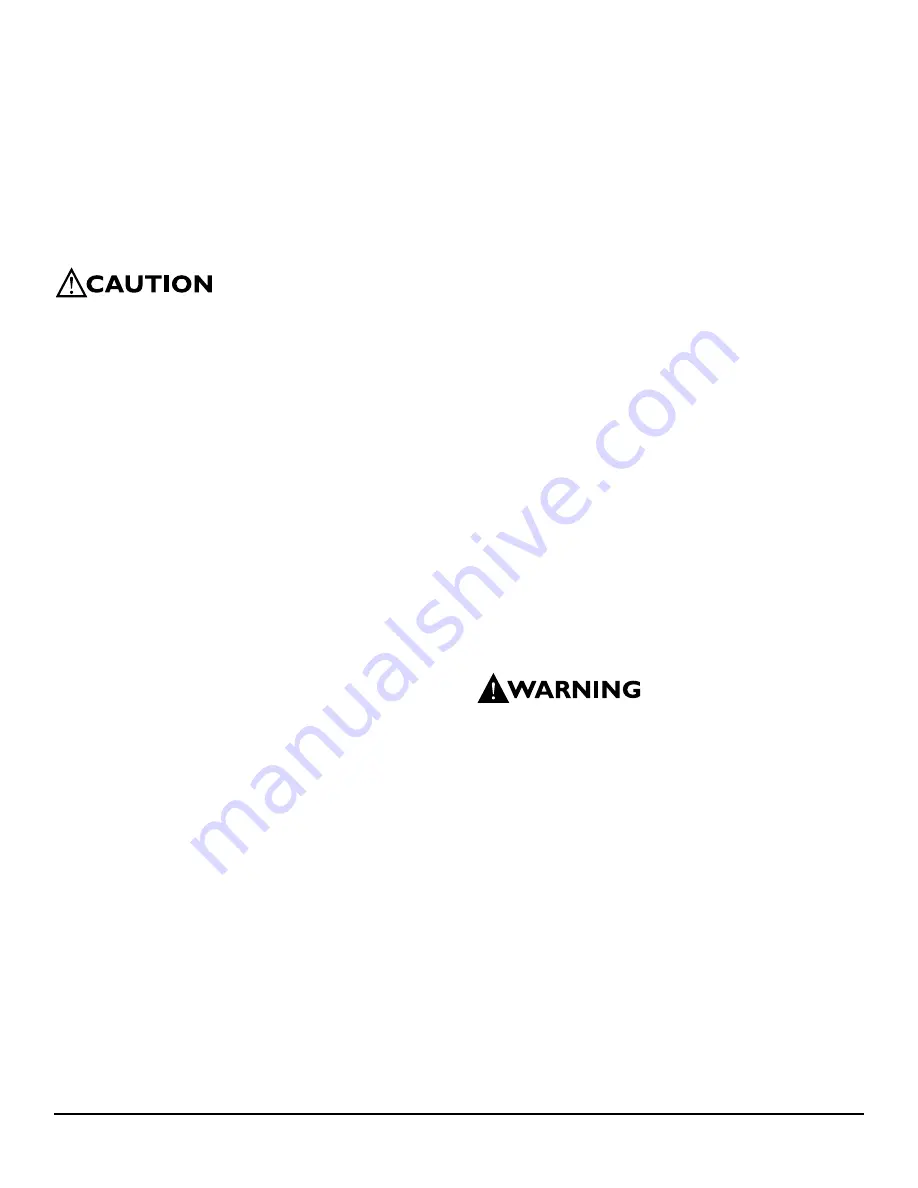
6
www.thermastor.com • [email protected]
Toll-Free 1-800-533-7533
5. Rotate the blower outlet toward you as you remove it.
Use care to avoid hooking wiring, tubing or electrical
components.
6. Reassembling with the new blower in the above
procedure reversed.
4.6 Compressor/Capacitor Replacement
This compressor is equipped with a two terminal external
overload, run capacitor, but no start capacitor or relay (see
Fig. 3).
CAUTION-ELECTRICAL SHOCK HAZARD: Electrical power
must be present to perform some tests; these tests should
be performed by a qualified service person.
4.6A Checking Compressor Motor Circuits
Perform the following tests if the blower runs but the
compressor does not with the power switch ON.
. Turn the power switch OFF and unplug the unit, remove
top panel and the cabinet front (6 screws).
2. Plug in the unit and turn the power switch ON. Use
a voltmeter to check for 0 to 20 volts between
(a) the relay terminal that the black wire from the
compressor connects to and (b) the capacitor terminal
with the 2 white wires & blue wire connected. If
voltage is present, go to step 3. If no voltage, the
low pressure control or relay are open or there is a
loose connection in the compressor circuit. Test each
component for continuity; see the appropriate section
if a defect is suspected.
3. Turn the power switch OFF and unplug the unit, then
disconnect the red and yellow wires from compressor
terminals R & S. Using an ohmmeter, check continuity
between the points listed below.
4. Compressor terminals C and S: No continuity indicates
an open start winding; the compressor must be
replaced. Normal start winding resistance 3 to 7
ohms.
5. Compressor terminals C and R: No continuity indicates
an open run winding; the compressor must be
replaced. Normal run winding resistance is .5 to 2
ohms.
6. Compressor terminal C and overload terminal : No
continuity indicates a defective overload lead.
7. Overload terminals and 3: If there is no continuity,
the overload may be tripped; wait 0 minutes and try
again. If there is still no continuity, it is defective and
must be replaced.
8. Compressor terminal C and compressor case:
Continuity indicates a grounded motor; the compressor
must be replaced.
9. Disconnect the wires from the capacitor. Set the
ohmmeter to the Rx scale; the capacitor is shorted
and must be replaced if continuity exists across its
terminals. If there is no needle movement with the
meter set on the Rx00000 scale, the capacitor is
open and must be replaced.
0. Reconnect the wires to the compressor and capacitor;
plug in and turn on the unit. If the compressor fails to
start, replace the run capacitor.
. If the unit still does not start, adding a hard-start kit
will provide greater starting torque. If this does not
work, the compressor has an internal mechanical
defect and must be replaced.
4.6B Replacing a Burned Out Compressor
The refrigerant and oil mixture in a compressor is
chemically very stable under normal operating conditions.
However, when an electrical short occurs in the
compressor motor, the resulting high temperature arc
causes a portion of the refrigerant oil mixture to break
down into carbonaceous sludge, a very corrosive acid,
and water. These contaminants must be carefully removed
otherwise even small residues will attack replacement
compressor motors and cause failures.
The following procedure is effective only if the system is
monitored after replacing the compressor to insure that
the clean up was complete.
. This procedure assumes that the previously listed
compressor motor circuit tests revealed a shorted or
open winding. If so, cautiously smell the refrigerant
from the compressor service port for the acid odor of
a burn out.
WARNING: The gas could be toxic and highly acidic. If no
acid odor is present, skip down to the section on changing
a non-burn out compressor.
2. Remove and properly dispose of the system charge.
DO NOT vent the refrigerant or allow it to contact your
eyes or skin.
3. Remove the burned out compressor. Use rubber gloves
if there is any possibility of coming in contact with the
oil or sludge.
4. To facilitate subsequent steps, determine the type of
burn out that occurred. If the discharge line shows no
evidence of sludge and the suction line is also clean
or perhaps has some light carbon deposits, the burn
out occurred while the compressor was not rotating.
Contaminants are therefore largely confined to the
compressor housing. A single installation of liquid
and suction line filter/driers will probably clean up the
system.