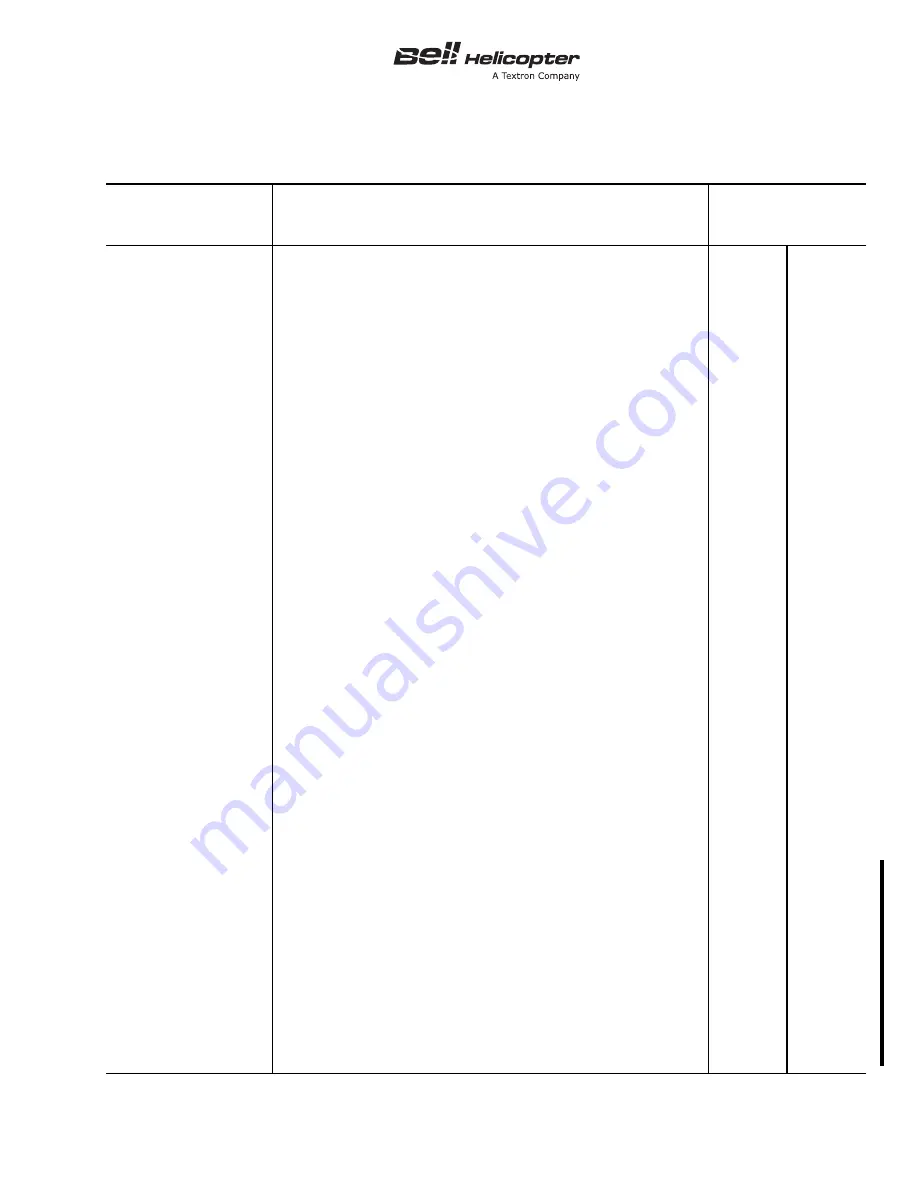
BHT-412-MM-2
5-00-00
Export Classification C, ECCN EAR99
3.
Tailboom and fin external skin for damage, corrosion, and
cracks.
4.
Tailboom access panels and covers for condition and
attachment. Tail rotor driveshaft cover hinges for wear.
5.
Tailboom baggage compartment door for condition,
attachment, and door handle operation.
6.
Tailboom baggage compartment interior for damage,
panels for disbonding, and corrosion. Longerons above roof
panel for corrosion and cracks. Longerons below floor panel for
corrosion and cracks.
7.
Tailboom interior bulkheads and stringers for cracks and
corrosion.
8.
Intermediate gearbox mount pad for damage, cracks,
fretting, and corrosion.
9.
Tail rotor gearbox support fitting assembly for damage,
cracks, fretting, and corrosion. Pay particular attention to
mounting holes and lugs.
10.
Tailboom exterior bonded panels adjacent to baggage
compartment for damage, delamination, and corrosion.
11.
With a borescope or equivalent, inspect interior structure
of vertical fin for cracks, corrosion, fretting, and damage.
12.
Control tube fairleads (grommets and guides) for wear and
security of attachment.
SCHEDULED INSPECTIONS
5-8.
5000 HOUR/5 YEAR INSPECTION — PART A (CONT)
DATA REFERENCE
INSPECTION TASK DESCRIPTION
INITIAL
MECH OTHER
15 DEC 2015
Rev. 23
Page 56A
Summary of Contents for Bell 412
Page 6: ......
Page 12: ......
Page 32: ......
Page 40: ......
Page 152: ......
Page 154: ......
Page 156: ......
Page 158: ......
Page 160: ......
Page 164: ......
Page 166: ......
Page 168: ......
Page 172: ......
Page 174: ......
Page 198: ......
Page 202: ......
Page 220: ......
Page 224: ......
Page 232: ......
Page 234: ......
Page 236: ......
Page 242: ......
Page 256: ......
Page 262: ......
Page 268: ......
Page 288: ......