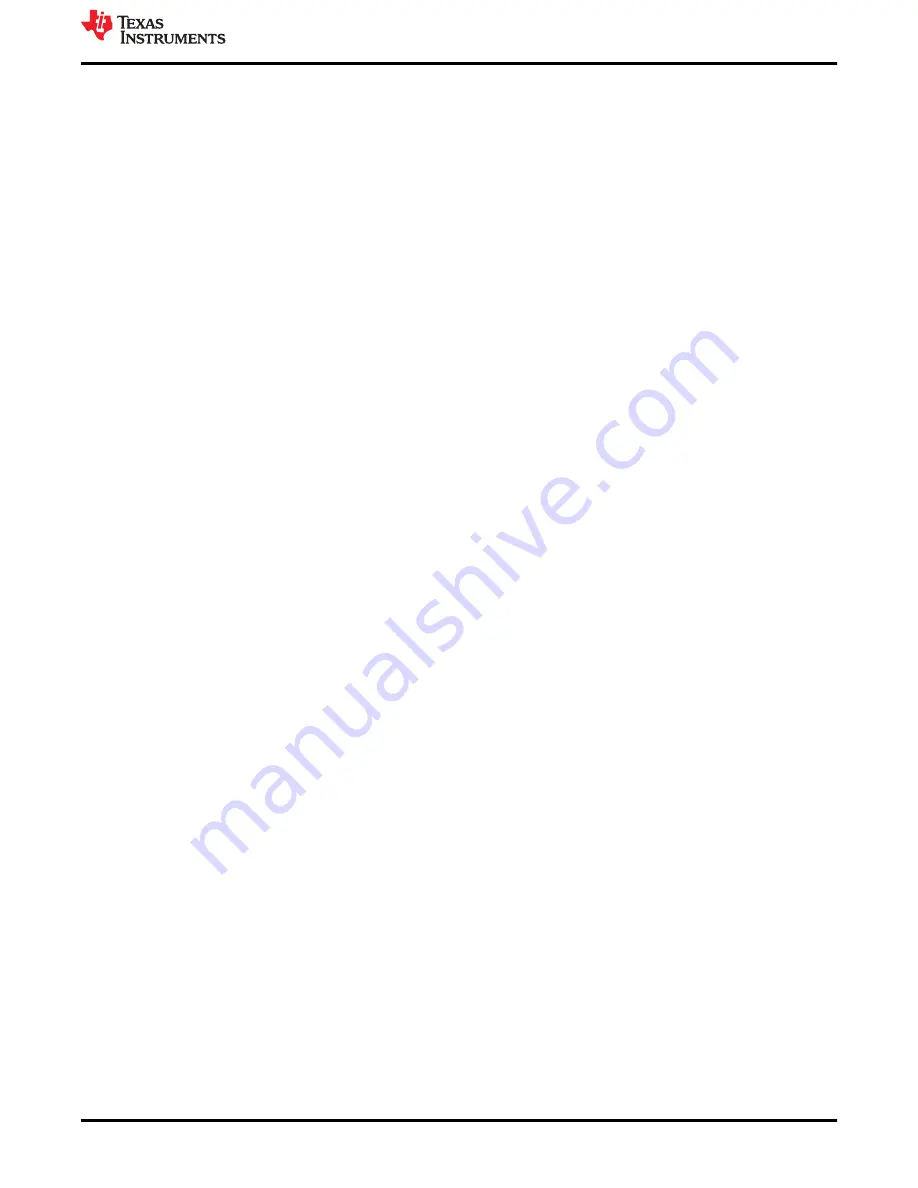
Motor can be stopped by issuing 0% input speed duty cycle.
Step 1: Configure closed loop deceleration [CL_DEC] to a value that is same as closed loop acceleration
[CL_ACC].
Step 2: Configure Motor stop option [MTR_STOP] to either High side or low side braking.
Step 3: Set the active spin brake threshold [ACT_SPIN_BRK_THR] to a value such that Overcurrent protection
fault does not get triggered. Check GATE_DRIVER_FAULT_STATUS (register address: 0x000000E0) bit 28 for
Overcurrent protection fault status.
Step 4: Configure Recirculation Brake time [RECIR_BRK_TIME] to a value such that motor is stopped
completely. Recirculation brake time might be higher for motors with higher inertia.
Step 5: Enable Fast deceleration [FAST_DECEL_EN].
Note: Fast deceleration will be active till the input speed duty cycle decelerates to active spin brake threshold
[ACT_SPIN_BRK_THR]. Device will engage High side or low side braking when the input speed duty cycle is
below the active spin brake threshold [ACT_SPIN_BRK_THR].
Option 2: Stopping motor quickly during all stages of motor operation.
Step 1: Configure closed loop deceleration [CL_DEC] to a value that is same as closed loop acceleration
[CL_ACC].
Step 2: Configure brake input [BRAKE_INPUT] to “Hardware pin brake” to apply brake using the BRAKE pin.
Use Brake switch S1 in MCx8316AEVM to pull the BRAKE pin HIGH or LOW. MCT8316A applies brake when
BRAKE pin is pulled HIGH. Configure brake input [BRAKE_INPUT] to “Overwrite Hardware pin with Active
Brake” to apply brake using I
2
C.
Step 3: Set the brake duty threshold [BRAKE_DUTY_THRESHOLD] to a value such that Overcurrent protection
fault does not get triggered. Check GATE_DRIVER_FAULT_STATUS (register address: 0x000000E0) bit 28 for
Overcurrent protection fault status.
Step 4: Enable Fast deceleration [FAST_DECEL_EN].
Note: Fast deceleration will be active till the input speed duty cycle decelerates to brake duty threshold
[BRAKE_DUTY_THRESHOLD]. Device will engage High side or low side braking when the input speed duty
cycle is below the brake duty threshold [BRAKE_DUTY_THRESHOLD].
4.3.7 Faster deceleration
Follow below steps to decelerate the motor quickly.
Step 1: Configure closed loop deceleration [CL_DEC] to a value that is same as closed loop acceleration
[CL_ACC].
Step 2: Enable Fast deceleration [FAST_DECEL_EN].
Step 3: Configure Fast deceleration current limit [FAST_DECEL_CURR_LIM]. Fast deceleration current limit will
be higher for motors with higher inertia.
Step 4: Enable AVS [AVS_EN] to protect the power supply from voltage overshoots during motor deceleration. If
AVS is enabled, the time taken to decelerate the motor will increase.
Disable AVS, if the power supply can withstand voltage overshoots.
Step 5: Configure Fast Decel Brake Threshold [FAST_BRK_DELTA] if the fast deceleration should be disabled
before the actual motor speed reaches the target speed. For example, if the Fast Decel Brake Threshold
[FAST_BRK_DELTA] is configured to 0.5% and target duty cycle is configured to 5%, device will stop
decelerating the motor at 5.5%. This can be helpful in applications where the motor is decelerated to critically
low speeds. While the motor decelerates quickly to critically low speeds, there are possibilities that the motor
might stop. In such applications, it is required to stop decelerating the motor at slightly higher speeds to avoid
the device from completely stopping the motor.
shows phase current and motor electrical speed waveform when the motor decelerates from 100%
duty cycle to 10% duty cycle. Time taken for the motor to decelerate from 100% duty cycle to 10% duty cycle
Basic Controls
SLLU336 – MAY 2021
MCT8316A Tuning Guide
19
Copyright © 2021 Texas Instruments Incorporated