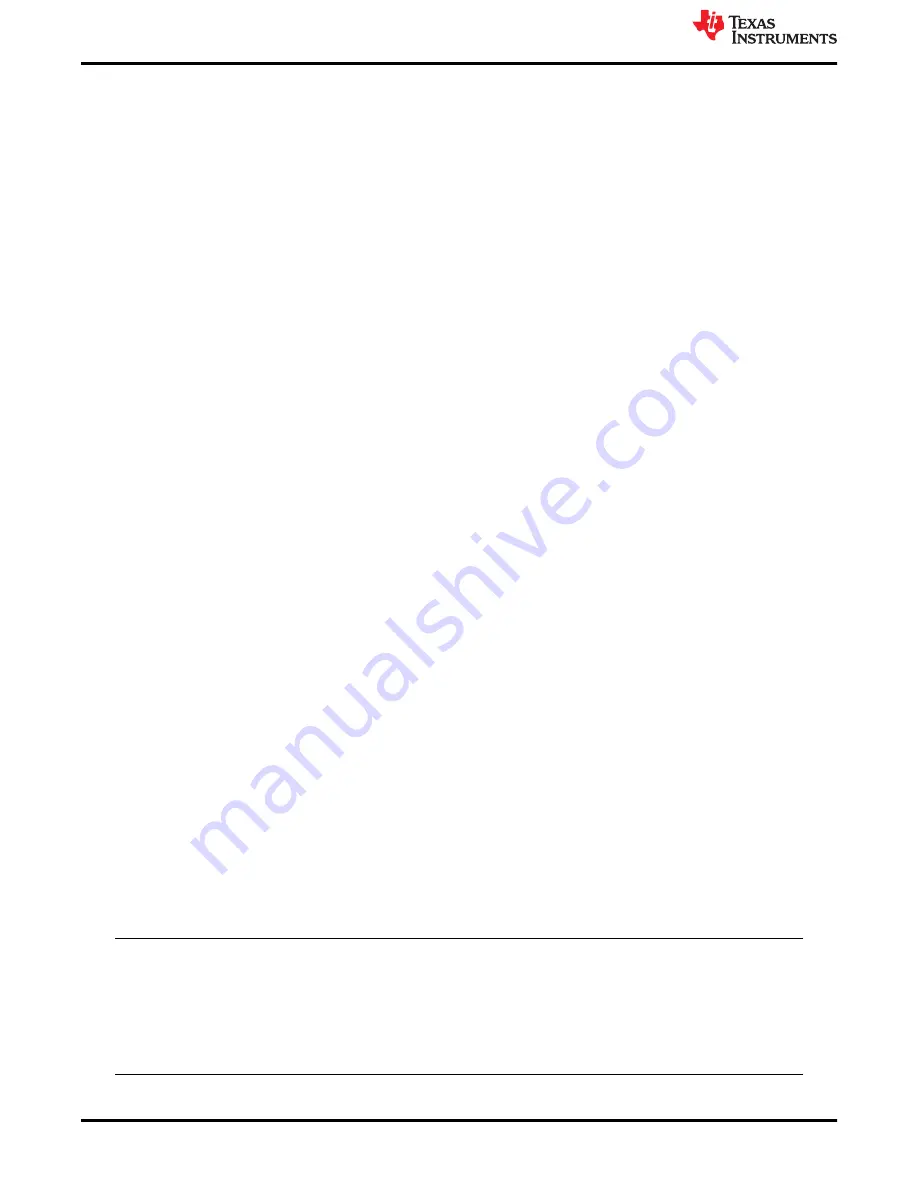
Option 2: Slow first cycle
Follow below steps if Slow first cycle is chosen as the startup method.
Step 1: Select Slow first cycle in the Motor startup option [MTR_STARTUP] in “Control Configuration – Motor
Startup Stationary” tab in the GUI.
Step 2: Select Align current threshold [ALIGN_CURR_THR]. Lower current threshold may lose synchronization
of motor. Higher current may lead to sustained oscillations for high inertia motors, or sudden jerky motion for
low inertia motors. It is recommended to start with 50% of the rated current of the motor. In applications where
the startup torque is high, the motor might lose synchronization. In such applications, it is recommended to
increase the current reference. In applications where, sustained oscillations or sudden jerks are observed, it is
recommended to decrease the current threshold.
Step 3: Select Align current ramp rate [ALIGN_RAMP_RATE]. Current reference is ramped to avoid reverse
rotation of the motor. Lower current ramp rate may lose synchronization of motor. A higher current ramp rate
may lead to sustained oscillations for high inertia motors, or sudden jerking motion for low inertia motors. It
is recommended to start with setting up the ramp time to 0.5 sec to ramp to rated current of the motor. In
applications where the startup torque is high, the motor might lose synchronization. In such applications, it is
recommended to increase the current ramp rate. In applications where, sustained oscillations or sudden jerks
are observed, it is recommended to decrease the current ramp rate.
Step 4: Select Frequency of first cycle [SLOW_FIRST_CYC_FREQ]. Lower frequency may give a jerky motion
at startup. Higher frequency may not be able to synchronize the motor. It is recommended to start with 20%
of the maximum speed of the motor. In applications where the startup torque is high, the motor might lose
synchronization. In such applications, it is recommended to decrease the frequency. In applications where jerky
motions are observed, it is recommended to increase the frequency.
4.3.4 Faster startup timing
Startup time is the time taken for the motor to reach closed loop from zero speed. For applications that require
quick startup time, we recommend choosing either Initial Position Detection (IPD) or Align as the startup method.
Option 1: Initial Position Detection (IPD)
Step 1: Select IPD [MTR_STARTUP] as the motor startup method.
Step 2: Increase IPD current threshold [IPD_CURR_THR] to rated current of the motor. Use equation 4 to
choose the correct IPD_CURR_THR.
Step 3: Increase IPD clock value [IPD_CLK_FREQ] to higher frequency up to a value where the device does not
trigger IPD frequency fault. Check section 3.4.4 (Step 3) for more details.
Step 4: Select IPD repeating times [IPD_REPEAT] to 1 time.
Step 5: Configure IPD release mode [IPD_RLS_MODE] to Tri state.
Step 6: Select Open loop current limit [OL_ILIMIT] to be the same as cycle by cycle current limit [ILIMIT].
If the device triggers cycle by cycle current limit [CBC_ILIMIT], it is recommended to increase [ILIMIT] upto the
stall current of the motor. Configuring this to a value higher than motor stall current might overheat or damage
the motor.
Step 7: Increase Open loop acceleration coefficient A1 [OL_ACC_A1] and Open loop acceleration coefficient A2
[OL_ACC_A2].
Note
A1 and A2 can be increased until open loop current reaches Lock detection current threshold
[LOCK_ILIMIT]. Open loop current can be measured using oscilloscope.
Increasing Open loop acceleration coefficient A1 [OL_ACC_A1] and Open loop acceleration
coefficient A2 [OL_ACC_A2] might trigger LOCK_LIMIT or CBC_ILIMIT. If this happens, reduce A1
and A2 until LOCK_LIMIT no longer triggers.
Basic Controls
16
MCT8316A Tuning Guide
SLLU336 – MAY 2021
Copyright © 2021 Texas Instruments Incorporated