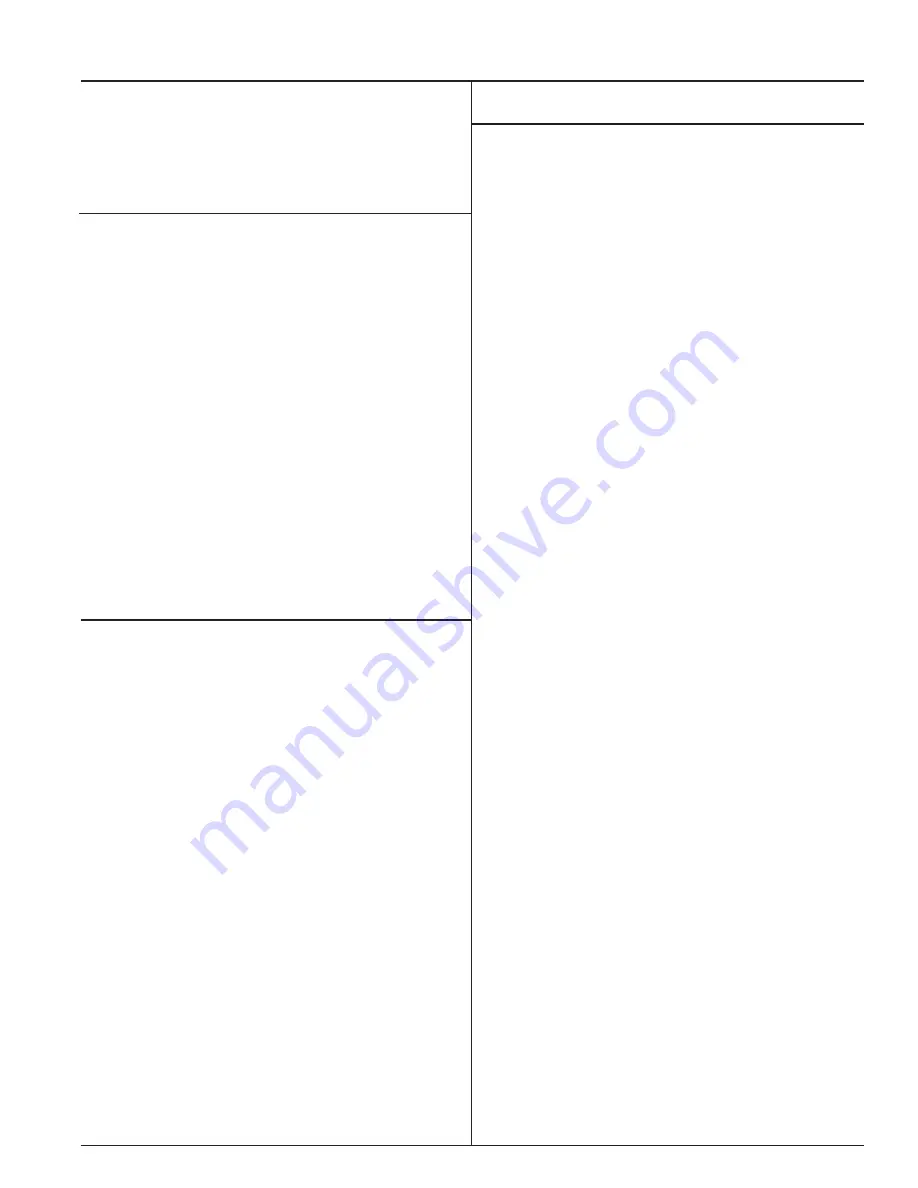
Page 15
472H Potato Harvester Owner Operator’s Manual
3.4 INITIAL OPERATING PROCEDURE
Although no operational restrictions exist when using the
Lockwood 472H Potato Harvester for the first time, Lockwood
recommends that the following mechanical items be
checked:
3.4.1 PRE-START INSPECTION
1.
Read the Operator’s Manual.
2.
Tighten wheel bolts to (5/8) 125-140 ft-lbs. torque and
(3/4) 200-250 ft-lbs torque.
3.
Check tires and inflate to their specified pressure.
4.
No hydraulic lines and electrical harnesses should con-
tact moving parts. Clip, tape, or tie all components se-
curely in place.
5.
Check that all guards are installed and secured.
6.
Install and tighten all required nuts and bolts to their
specified torque.
3.4.2 AFTER OPERATING FOR 2 HOURS
1. Re-torque all the wheel bolts.
2. Re-torque all other fasteners and hardware.
3. Check that all safety decals are installed and legible.
Apply new decals if required.
4. Check for any pinched, crimped, or rubbing hoses.
Reroute as required.
5. Check that the wiring harness is not being pinched,
crimped, or rubbing. Reroute as required.
6. Check the tension and alignment of all drive and feed
chains. Adjust as required.
3.4.3 AFTER OPERATING FOR 10 HOURS:
1. Re-torque all wheel bolts, fasteners and hardware.
2. Check that all guards are installed, secured and func-
tioning as intended. Do not operate with missing or
damaged shields.
3. Check safety decals. Install new ones if required.
4. Check the routing of hydraulic lines and the wiring
harness. Reroute as required to prevent pinching,
crimping, binding, or rubbing.
5. Go to the normal servicing and maintenance sched-
ule as defined in the Maintenance Section.