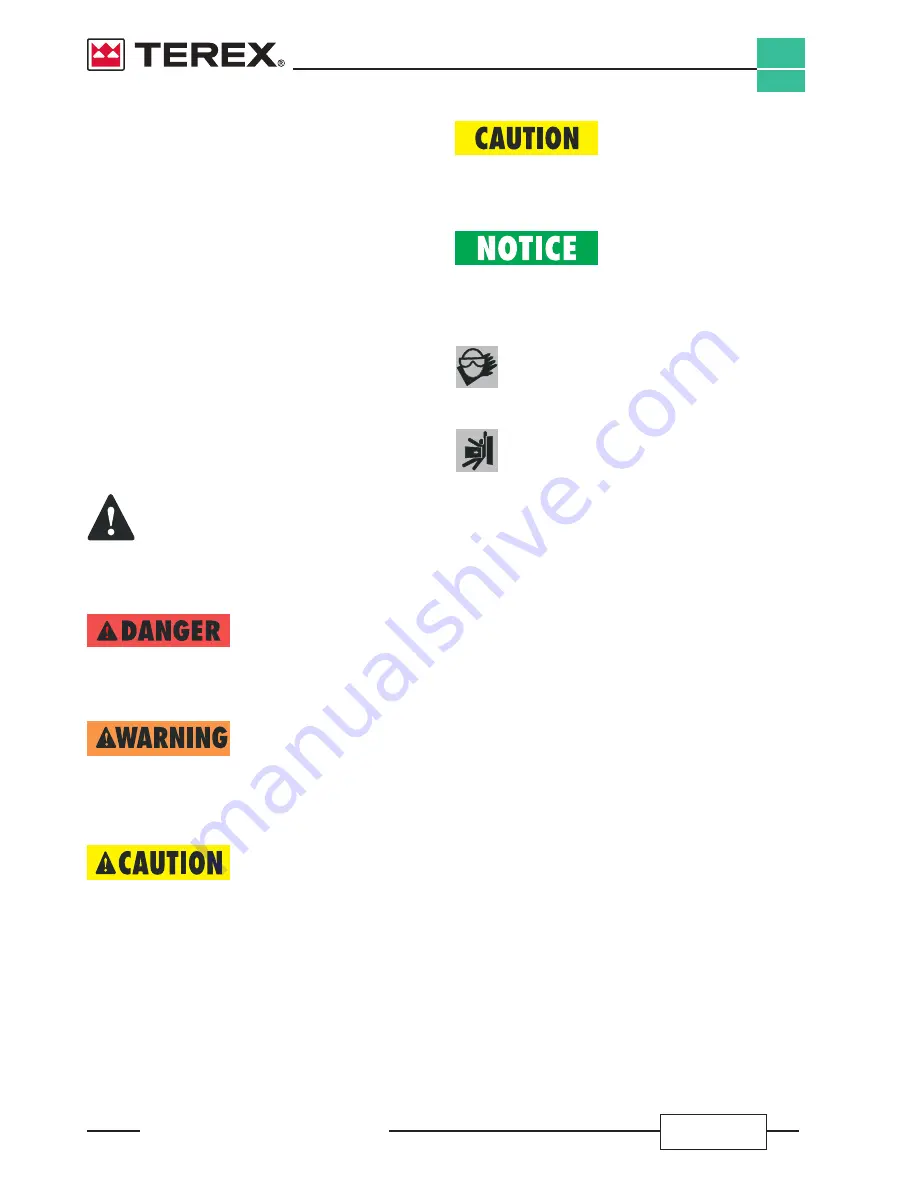
INDEX
GYRO 4020 - 4518
SAFETY
1
2
Document 57.4402.8200 - 1
st
Edition 03/2007
1.1
SAFETY RULES
1.1-1
Personal Safety
In this manual, any important information is preceded by
a
SPECIAL SYMBOL
.
All operators who work or service the machine must know
the exact meaning of these safety symbols.
There are six special (or safety) symbols in this manual,
always combined with keywords that class the situations
according to their danger degree.
The symbols are always followed by a text explaining
the situation taken into account, the attention to be paid
to such situation, the method and the behaviour to be
adopted. When necessary, it stresses prohibitions or
supplies instructions to prevent dangers.
Sometimes, it can be followed by illustrations.
We list below the special (or safety) symbols according
to the relative seriousness of the hazard situation:
Draws the attention to situations that involve your
own as well as the others’ safety and that can result
in serious or lethal injury.
Draws the attention to situations that involve your
own as well as the others’ safety and that can result
in serious or lethal injury.
Draws the attention either to situations that involve
your own as well as the others’ safety and that can
result in minor or moderate injury or to situations
that involve the machine efficiency.
Draws the attention either to situations that involve
your own as well as the others’ safety and that can
result in minor or moderate injury or to situations
that involve the machine efficiency.
Draws the attention to important technical information
or practical advice that allows for a safer and more
efficient use of the machine.
Draws the attention to important environment-related
information.
Be sure to wear protective eye wear and
other protective clothing if the situation
warrants it.
Be aware of potential crushing hazards such
as moving parts, free swinging or unsecured
components when lifting or placing loads.
Always wear approved steel-toed shoes.