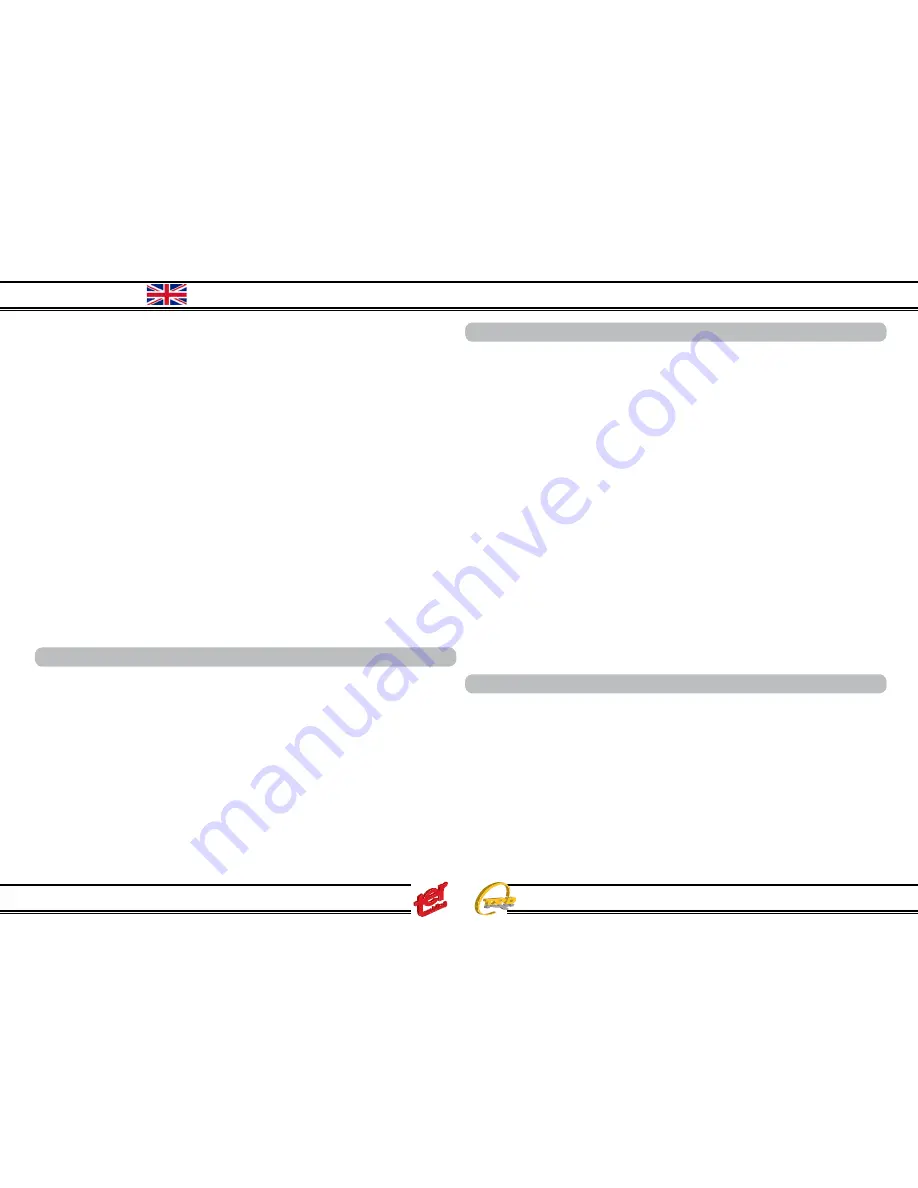
Instruction Manual
Multi Synergic 280 - Multi Synergic 350 - Multi Synergic 400F - Multi Synergic 500- Multi Synergic 500F and Accessories
8
The MULTI series generators are characterised by a its ED factor – 40% at 40°C and
power supply may, in certain cases, be sufficient for this output but the used can
adjust higher power output causing damages on the existing supply network. (or can
use long interconnecting cable at maximum output current).
The MULTI SYNERGIC series controls regularly the output power Vs the input power
value and in case of any discrepancy the welding stops and the display will shows:
ALL Ed xxx:
The machine will be available again at the end of the count-down
shown on the display.
INVERTER OVER HEATING OR OVER LOAD OR OVER CURRENT
The MULTI SYNERGIC series generators are fan cooled. Forced ventilation is activated
once the inverter temperature exceed the 40°C and fan turns automatically off once inter-
nal components are correctly cooled.
Fan cooling is anyway rarely activated: it may occurs when duty cycle has been exceed-
ed, in case of high environment temperatures, etc.
In case of overheating, output is disabled and display will shows:
ALL OL
10. AUXILIARY ELECTRONIC WARNING AND FAILURE
The Internal electronic is governed by software and when errors come from the execution
of the cycles the display shows the alarms that can be ALL MEM, ALL TAB, I2C OCC,
when those alarms occurs may be the machine still works, refer to the troubleshooting
for the solution.
WIRE FEEDER STATUS
The wire feeder is digitally controlled, and ever, the wire speed has the right value,
in the case that something doesn’t works properly two alarms indicates the kind of
failure :
ALL ENC and ALL BRA
that means a wrong or missing speed or a wrong or
missing brake status of the motor at the end of the welding, refer to the troubleshoot-
ing for the solution.
11. WATER COOLING UNIT STATUS
When the generator is equipped with the cooling unit, the correct cooling liq-
uid circulation is constantly controlled. The cooling unit works only when Mig,
Pulsed Mig or Tig processes are activated.
The cooling unit pump is activated switching the torch trigger and turns off after
some time that the welding job end.
In case of liquid circulation failures, output is disabled and display will show:
ALL h2o
Reset the machine switching the main knob ON/OFF.
Long inactivity periods may damage the cooling unit pump or generate momen-
tary re-start problems. First ensure the presence of liquid inside the tank and
control the right positioning of the in/out hoses – following instructions may help:
• unplug the water-out blu hose from the machine rear panel and plug a tempo-
rary hose
• push & release the torch trigger once: cooling unit pump test should be acti-
vated for 15 seconds
• cooling liquid should flow from the temporary hose: if not, repeat the pump
test as above
• once ensured the correct liquid flowing, restore the original hose
• if necessary, control the correct liquid flowing at the intermediary levels, i.e
wire feeder unit rear and front
12. COMMUNICATION WITH THE EXTERNAL WIRE FEEDER
The external wire feeder can be connected to the connectors of the back panel of the
machine, the machine recognise the wire feeder and starts to communicate.
The control from the machine is passed to the wire feeder when the torch switch
of the wire feeder is pressed or when one of the pushbuttons of the wire feeder is
touched.
When an error in the communication between the machine and the wire feeder ap-
pear, the two display of the wire feeder show thee lines instead the values, this prob-
lem often occurs when the interconnecting cable connectors are loose or internal
wires of the interconnecting cable are open.