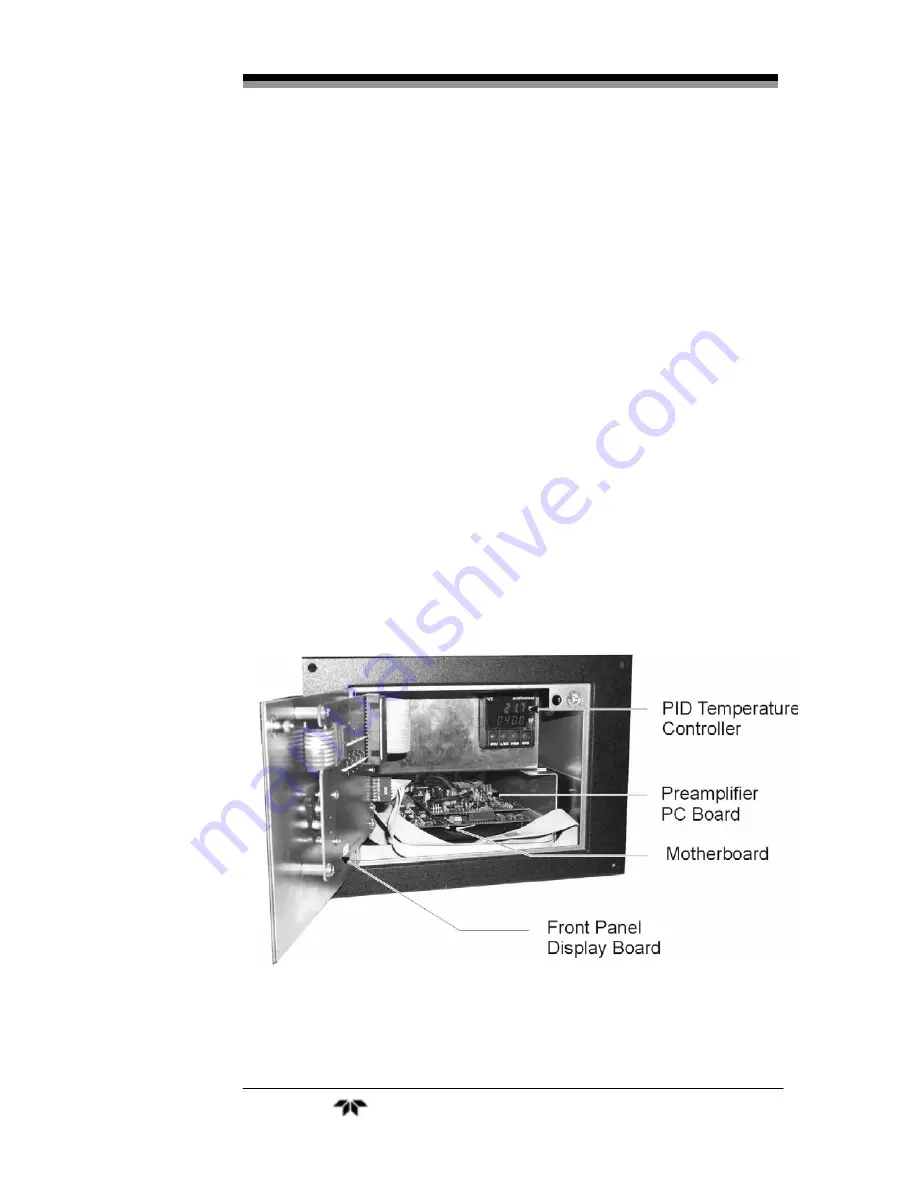
Part 2 Analysis Unit
Model 3010MA
Teledyne Analytical Instruments
74
Cyclo hexane C
6
H
12
-1.56
Nitric
oxide
NO
+40.00
Ethane C
2
H
6
-0.43
n-Octane
C
8
H
18
-2.50
Ethylene C
2
H
4
-0.26
n-Pentane
C
5
H
12
-1.45
Helium He
+0.30
Propane C
3
H
8
-0.86
n-Heptane C
7
H
16
-2.10
Propylene
C
3
H
6
-0.55
n-Hexane C
6
H
14
-1.70
Vinyl
chloride
-0.63
Hydrogen H
2
+0.24
Water
H
2
O -0.02
Hydrogen bromide HBr
-0.61
Xenon Xe
-0.95
6.3 Oven and Temperature Controller
The oven in the Analysis Unit is used to provide thermal stability to
the sensor assembly is comprised of dual 40 watt heaters powered by 115
or 230 V ac from the Control Unit. The oven temperature is maintained at
40
°
C by a PID temperature controller housed in the Control Unit. An RTD
sensor is mounted in the Analysis Unit to provide feedback to the PID
controller. The temperature in the Analysis Unit at any time can be read
from the display on the temperature controller after opening the front
panel of the Control Unit. See Figure 6-5. This can be done without
affecting the thermal environment of the Analysis Unit.
Figure 6-5: Access to Temperature Controller in Control Unit
Summary of Contents for 3010MA
Page 12: ...Part 1 Control Unit Model 3010MA Teledyne Analytical Instruments xii...
Page 14: ...Part 1 Control Unit Model 3010MA Teledyne Analytical Instruments 14...
Page 24: ...Part 1 Control Unit Model 3010MA Teledyne Analytical Instruments 24...
Page 64: ...Part 1 Control Unit Model 3010MA Teledyne Analytical Instruments 64...
Page 66: ...Part 2 Analysis Unit Model 3010MA Teledyne Analytical Instruments 66...