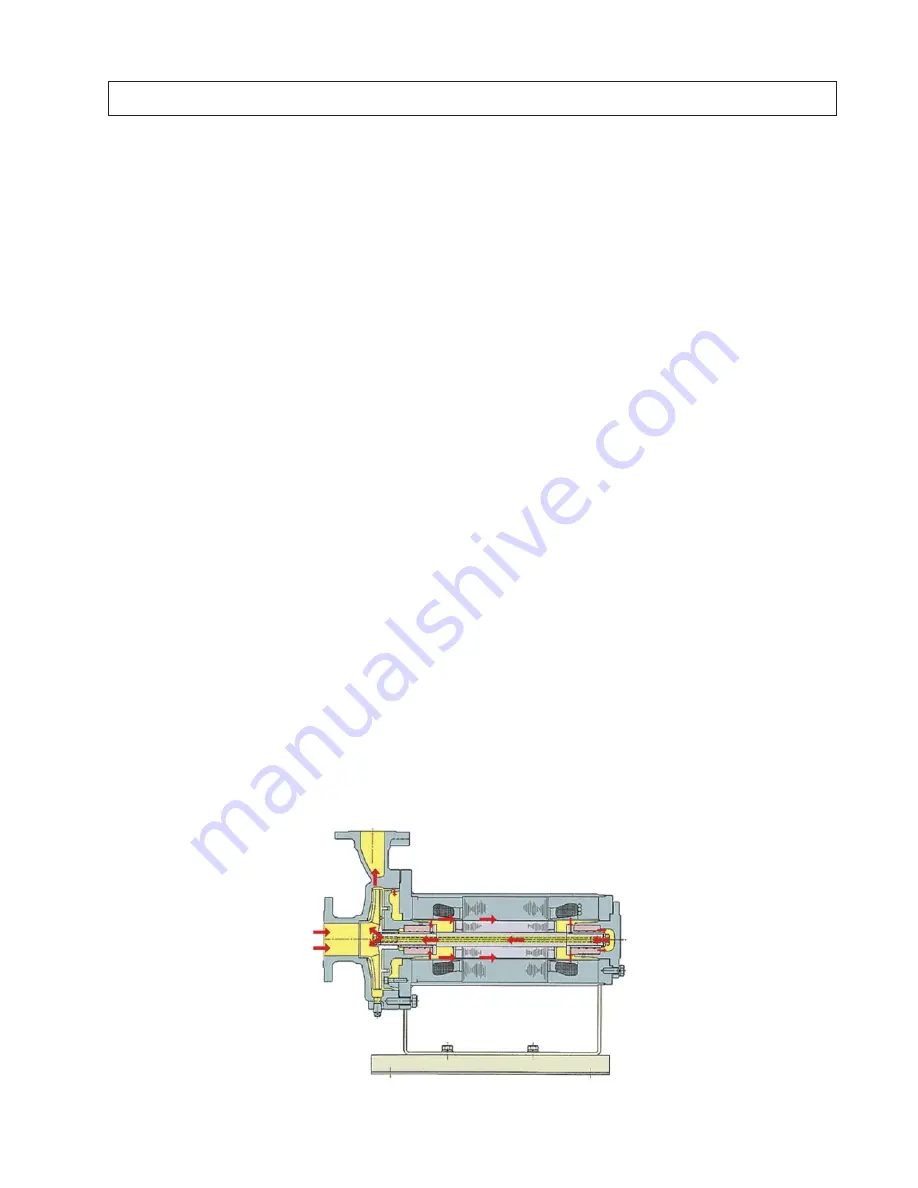
1.1 General Design and Operation
The Dynapump LE Series is a combined centrifugal
pump and squirrel cage induction electric motor built
together into a single hermetically sealed unit. The
pump impeller is of the closed type, and is mounted
on one end of the rotor shaft, which extends from the
motor section into the pump casing. The rotor is sub-
merged in the fluid being pumped and is, therefore,
“canned” to isolate the motor rotor from contact with
the fluid. The stator winding is also “canned” to iso-
late it from the fluid being pumped. Bearings are
submerged in system fluid and are therefore, lubri-
cated by the process fluid.
The Dynapump LE has only one moving part, a com-
bined rotor-impeller assembly that is driven by the
induced magnetic field of an induction motor. A por-
tion of the pumped fluid is allowed to re-circulate
through the rotor cavity to cool the motor and lubri-
cate the bearings. The stator windings are protected
from contact with the re-circulating fluid by a corro-
sion resistant, non-magnetic, alloy liner, which com-
pletely seals or “cans” the stator winding. The re-
circulating fluid is channeled into the motor section
by holes drilled in the front bearing housing. A por-
tion of the pumpage flows across the front bearing
and returns to the rear of the impeller. The remain-
der passes over the rotor, across the rear bearing,
and returns to suction through a hollow shaft. See
Figure 1-1.
The Dynapump LE offers true positive secondary
containment as a standard design feature. In the
event of a failure of the primary containment can, the
stator assembly in conjunction with the leak proof
terminal post assembly provides the secondary con-
SECTION 1. General Information
Page 1
Figure 1-1. Dynapump LE Series Standard Circulation
tainment. This design prevents any release of the
process fluid out to the atmosphere.
A standard feature of the Dynapump LE is the pat-
ented Teikoku Rotary Guardian (TRG). The TRG is
an electrical meter that continuously monitors the
condition of the bearings. For more information on
the TRG refer to 2-3.4 Bearing Wear Monitor, Page 7.
The Dynapump LE sealless pump is a precision-
built unit that, with proper care, will give years of
trouble-free, leakproof service. The entire unit is
mounted on a fabricated steel base cradle. Opera-
tion is unaffected by the mounting or operating posi-
tion, eliminating the need for any costly alignment
procedures. This manual, containing basic instruc-
tions for installation, operation and maintenance of
the Dynapump LE Series, is designed to assist you
in obtaining this service.
It is important that the persons responsible for the
installation, operation, and maintenance of the pump,
read and understand the manual thoroughly.
Trouble-free Dynapump LE performance begins with
proper pump selection and application. If the se-
lected pump does not have the required performance
characteristics, or if the materials of construction are
not properly specified for the fluid being handled,
unsatisfactory operation may result. No amount of
maintenance can compensate for this.
If you are in doubt about proper Dynapump LE selec-
tion or application, write or call your Dynapump LE
engineering representative or the factory for assis-
tance. Additional copies of this manual are available
from the Dynapump LE field representative, the fac-
tory or on our website: www.dynapump.com.
Summary of Contents for DynaPump LE Series
Page 2: ...This page intentionally blank...
Page 6: ...This page intentionally blank...
Page 10: ...This page intentionally blank...
Page 16: ...This page intentionally blank...
Page 21: ...Figure 4 2 g Gap Figure 4 1 Bearing Wear Page 13...
Page 23: ...APPENDIX...
Page 27: ...A 4...
Page 28: ...A 5...
Page 29: ...A 6...
Page 30: ...A 7...