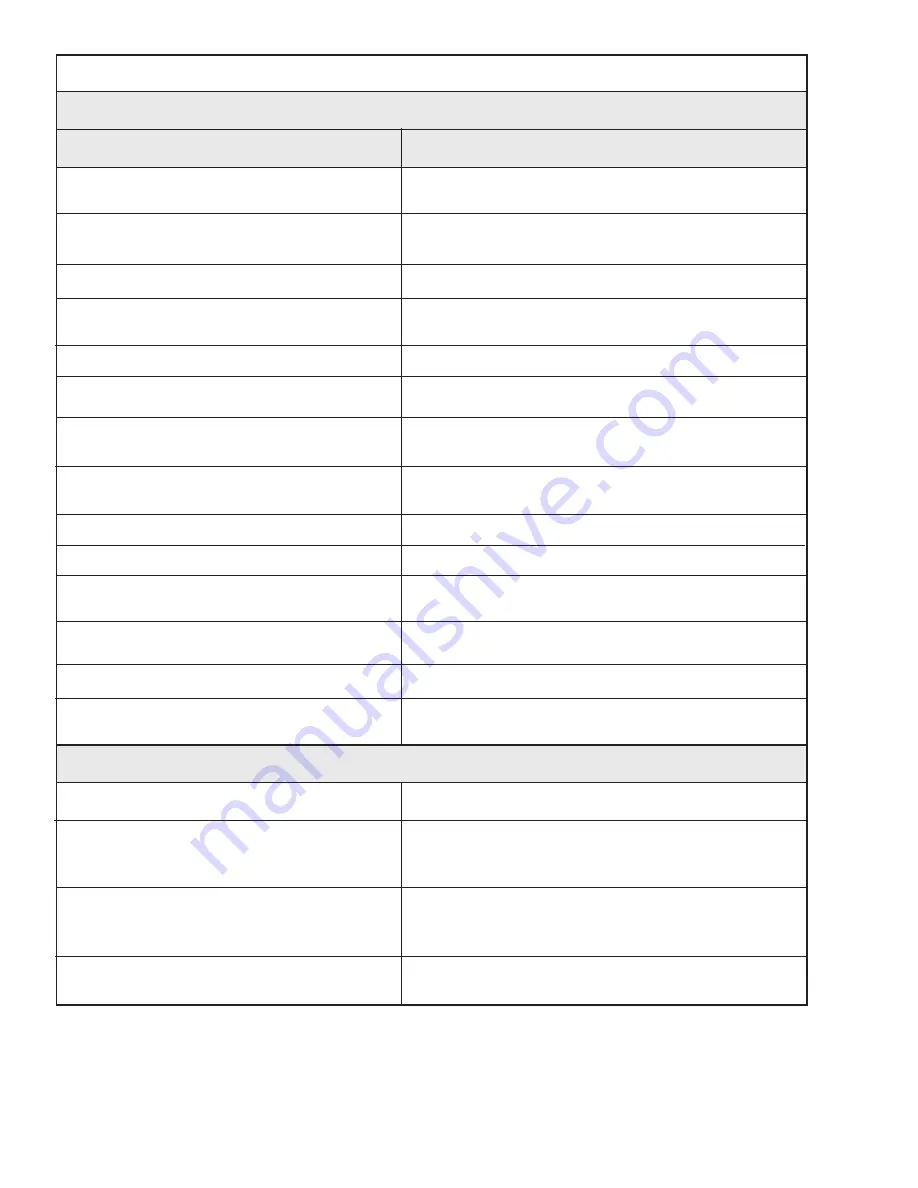
695578
Oil level too high.
To check level turn dipstick cap tightly into receptacle for
accurate level reading.
Oil filler cap loose or gasket damaged causing
Replace ring gasket under cap and tighten tube securely.
spillage.
Engine speed too fast.
Using tachometer adjust engine RPM to spec.
Gaskets damaged or gasket surfaces nicked
Clean and smooth gasket surfaces. Always use new
causing oil to leak out.
gaskets.
Breather tube not connected to air cleaner.
Reconnect tube.
Using 10W30 oil under high load/high temperature
Replace with SAE 30 oil.
conditions.
Breather mechanism damaged or dirty causing
Replace breather assembly.
leakage.
Drain hole in breather box clogged causing oil to
Clean hole with wire to allow oil to return to crankcase.
spill out of breather.
Oil passages obstructed.
Clean out all oil passages.
Piston oil control ring return holes clogged.
Remove oil control ring and clean return holes.
Piston rings and grooves worn excessively.
Reinstall new rings and check land clearance and correct
as necessary.
Cylinder wall worn or glazed, allowing oil to
Bore cylinder for oversized piston & rings.
bypass rings into combustion chamber.
Piston fit undersized.
Measure and replace as necessary.
Valve guides worn excessively thus passing oil
Ream valve guide oversize and install 1/32'’ oversize valve
into combustion chamber.
and new valve seal if equipped.
Crankcase breather plugged.
Clean or replace breather.
Seal outside seat in cylinder or side cover is
Visually check seal receptacle for nicks and damage.
damaged, allowing oil to seep around outer
Replace P.T.O. cylinder cover, or small cylinder cover on
edge of seal.
the magneto end if necessary.
Old seal hardened and worn.
Replace seal.
Crankshaft seal contact surface is worn undersize
Check crankshaft size and replace if worn excessively.
causing seal to leak.
Crankshaft bearing under seal is worn excessively,
Check crankshaft bearings for wear and replace if
causing crankshaft to wobble in oil seal.
necessary.
13-3
Remedy and Reference
Cause
Engine Uses Excessive Amount of Oil
Table 1. 4-Cycle Engine Troubleshooting Chart (Continued)
Oil Seal Leaks