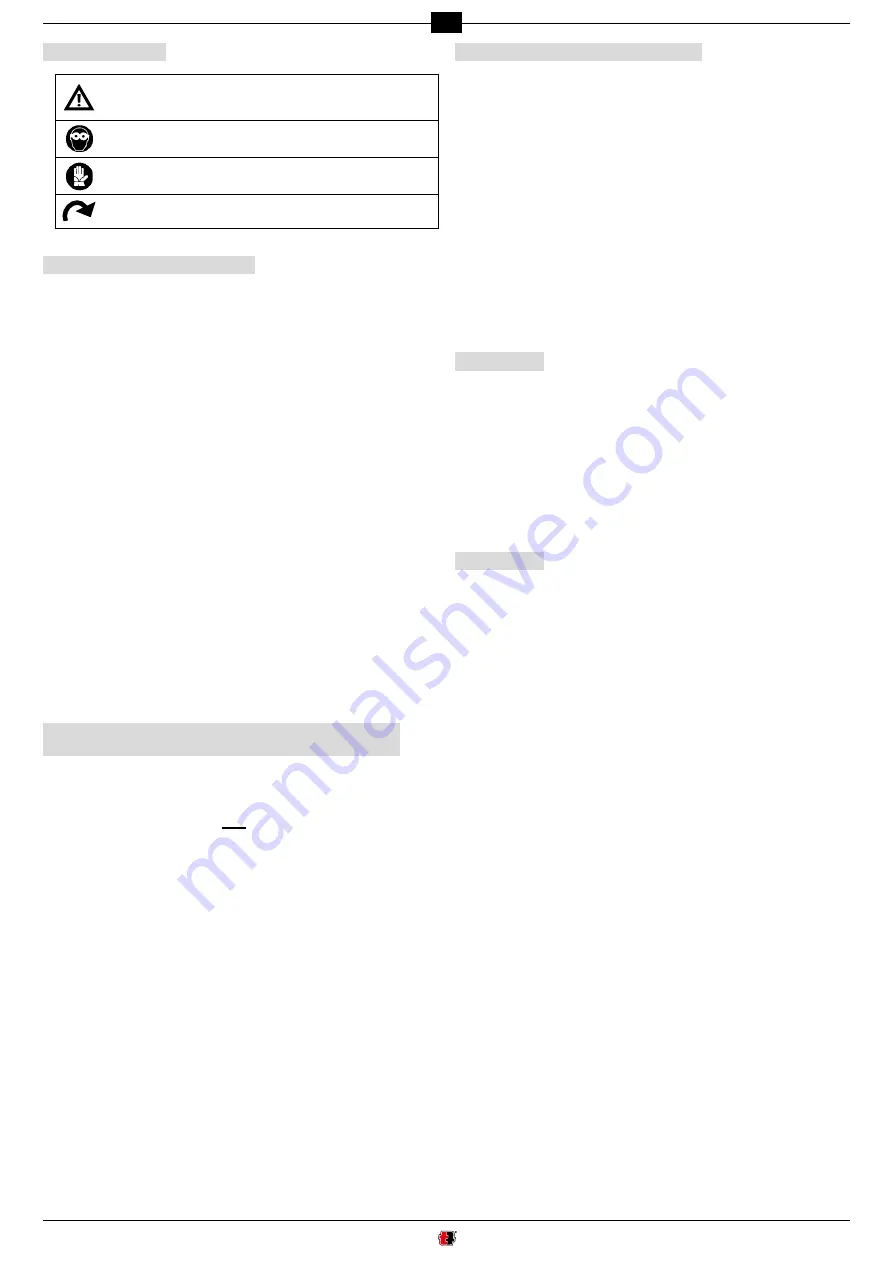
5
EN
SYMBOLS
This symbol points out the possibility of serious
personal injuries if the provisions and instructions are
not complied with.
This symbol points out that the user must wear
protection goggles when he uses the machine.
This symbol points out that the user must wear
protective gloves when he uses the machine.
This symbol points out the correct running direction of
the machine (grinding wheel)
PART DESCRIPTION (FIG.
V
)
1. Depth adjustment knob
2. Grinding wheel
3. Front protection
4. Large washer
5. Flange nut
6. Shield guard screw
7. Knob
8. Vise assembly
9. Dressing brick
10. Template
11. Handle bolt
12. Operating handle
13. Rear fih ed protection
Note:
for spare sarts, see
fig.
VI
.
ATTENTION – SETTING UP THE GRINDER
- the grinder shall only be used in a place protected from dust
and dampness, well-lighted, away from children, gases, or
other flammable or explosive liquids. The grinder shall be
placed near a suitable earthed outlet, not to use dangerous
extension cables.
- fasten the grinder onto the bench
(photo 1)
or to the wall
(photo 2)
with two M8 bolts (not provided). For fastening the grinder onto a
bench, carefully position it, using the relevant reference notches.
- when the grinder is fastened onto the bench or to the wall
(photo 2)
use a suitable square support (not provided), making sure that the
machine is not fastened at the level of the operator’s eyes. We
recommend that you install the grinder at a max. height of 120 -
130cm from ground level.
- insert screw M6x25 provided, making it slide up to the end of its seat
on the
arm
(photo 3)
- insert the screw into the slot
(photo 3)
.
- position the rear protection
(photo 4A)
.
- secure the handle on the screw
(photo 4B)
.
- after installing the grinder properly, assemble the wheel.
ASSEMBLY AND WARNINGS ABOUT THE GRINDING
WHEEL
- use a wheel fit for the type of chain to be ground, consulting the
chain table enclosed at the end of the handbook
(column
I - L)
-
before using the machine, check that the grinding wheels are
in perfect condition
. To do so, hang the wheels by the central hole
and tap them lightly with a
non
-metal object on the side near the
perimeter. If they are in perfect condition you should hear a metallic
sound. A dull sound means that the wheel is cracked or broken,
and
shall be replaced
.
- do not force the grinding wheel on the hub and do not modify the
diameter of the assembly hole. Be careful not to use grinding wheels
which do not perfectly match the machine
- to install the wheel, use only clean and perfect hub and ring nut
- make sure that the outside diameters of the hub/ring nut are identical
(fig.
I
)
- the hub is steadily fastened onto the electrical motor’s shaft
- unscrew the ring nut manually, center and install the wheel on the
hub, and re-screw the ring nut manually
(photo 5)
-
be careful with the ring nut assembly, since its discharge must
be on the wheel side (fig.
II
)
- if the grinding wheel’s ring nut is too tightened, the wheel could
break or disintegrate during operation, seriously damaging the
operator. To avoid this risk, do not overtight, since this ring nut is
made of thermoplastic material
- position the wheel guard properly
(foto 6A - 6B),
by rotating it till
the notch hits the arm
(foto 6C)
and secure it with the position lock
screw
(foto 6D)
.
CHECKING THE GRINDING WHEEL
- stand beside the wheel, start the grinder, and examine it to ensure
that it does not oscillate either laterally or transversally, creating any
anomalous vibration
- if the wheel oscillates, immediately stop the machine and make sure
that the wheel has been assembled properly.
If necessary, replace
the wheel with an original spare part
- with the machine off, check the wheel profile by means of the special
orange template
(fig.
III
point C)
- if necessary,
after wearing suitable goggles and gloves
, start
the grinder and retouch the wheel profile with the dressing stone
provided, working carefully, grasping the dressing stone with two
hands. The contact with the grinding wheel revolving at high speed
could cause burns and injuries
- before initiating grinding operations, test the assembled grinding
wheel at working speed for at least one minute, keeping far from the
machine and checking that nobody is standing on the trajectory of
its rotation plane.
N.B.: Replace the grinding wheels when their minimum
diameter is about 80mm (3.14 inches)
START-UP
- after fastening the machine onto the bench or to the wall, properly
install the wheel, its guard, and the handle, make sure that the
direction of rotation of the wheel is the one indicated on the wheel
guard; then, start up the machine
- the machine is equipped with a safety switch with a release coil, i.e.
in case of sudden power failure, this switch is deactivated, leaving
the machine on stand-by in case of a sudden return of current (to
restart the grinder, push the switch again)
- the machine must be connected with an outlet that ensures a
230V~
voltage or to a U.S. outlet that ensures 120V~
voltage and
10A current
GRINDING
- clean the chain before grinding it
- since this grinder has a fixed angle for the wheel inclination, the upper
cutting angle of the tooth is fixed at 60° (measured anticlockwise)
- position the chain to be ground on the two jaws, making sure that
the depth gauge is on the right, as indicated
(photo 7-points 1)
- loosen the ring nut at the back of the grinder
(photo 7 - point 2)
,
and turn the vise clockwise, considering the grade that corresponds
to the upper grinding angle of the right tooth, using the graduated
scale
(photo 7 - point 3)
- make one of the right teeth hit the chain stop, and, with the register
screw
(photo 8 - point 1)
, adjust the tooth feeding
- the chain stop is installed on a pin installed on a plastic connecting
rod. This pin has two position notches, so that the chain stop can be
positioned just at the center of the tooth to be ground
- stop the motor and lower the arm; then, with the chain feed register
screws, try to approach the tooth to the wheel, until it is slightly
touched, always starting from the worst tooth identified using the
template
(fig.
III
point D)
- start the grinder and, with the tooth feed register screw, determine
the quantity to be removed
- after determining the quantity to be removed, lock the register screw
with the ring nut
(photo 8 - point 2)
-
to avoid overloading the motor and to prevent the chain from
being damaged, remove minimum quantities of material and
do not work too long on the same tooth, so as not to damage
the cutter
- adjust the grinding depth with the register screw positioned on the
arm, without nicking connecting links
(photo 9)
- after determining the grinding depth, lock the register screw with the
ring nut
(photo 9 - point 1)
-
midi jolly-N
:
• adjust the clamping lever; press the red push-button and pull the
lever. The correct tightening of both jaws
(photo 10)
is set by a
slight clockwise rotation (clockwise rotation increases tightening,
whilst anti-clockwise rotation loosen it). The tightening system
with clamping lever allows a uniform deformation of the two chain
support jaws, so that the chain is always positioned just at the
center of the vise rotation. This is an essential requirement for
perfect grinding, because the length of the right and left teeth
must be the same.
• if the clamping lever is turned clockwise, the chain is locked
between the two jaws, for precise and safe grinding
(photo 11)
Summary of Contents for Midi Jolly-N
Page 2: ......
Page 45: ...43 ...
Page 50: ...I II III 48 IV RED 230V 120V BLACK ...
Page 52: ...6A 2 3 4A 4B 5 6C 6D 6B clik 1 clik 50 ...
Page 53: ...9 10 11 12 13 7 8 51 1 3 2 1 2 ...
Page 54: ...NOTE ...
Page 55: ......