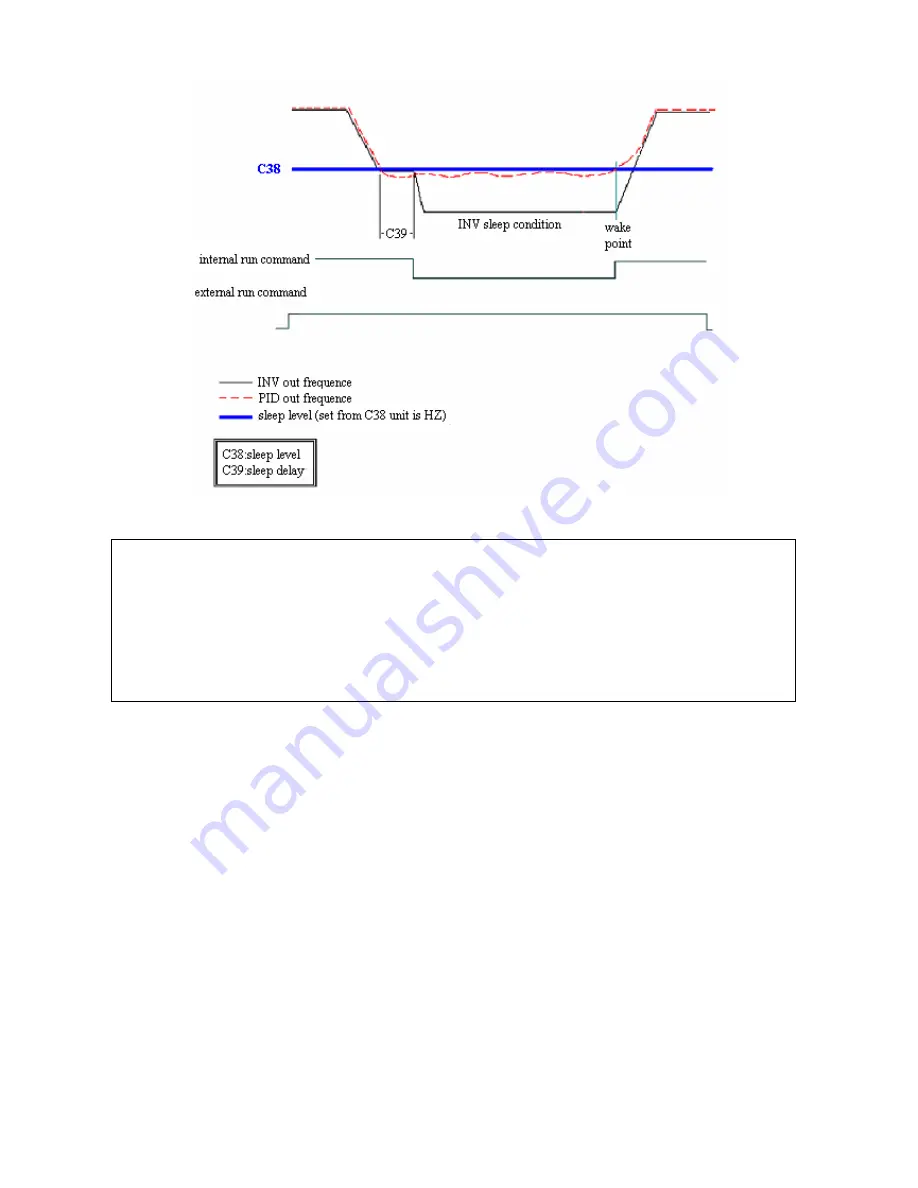
Chapter 4 Software index
4-31
Timing diagram is as following:
C40 Frequency Up/Down control using MFIT :
000: When using Up/Down command, the set frequency by this function will be
stored
after
the inverter stops.
UP/DOWN function is not available in stop mode.
001: When using Up/Down command, the set frequency will be reset to 0Hz
after
the inverter stops.
002: When using Up/Down command, the set frequency will be stored
after
the
inverter stops. UP/DOWN function is available in stop mode.
1)
C40=000: when the RUN signal is ON, the inverter will accelerate to
the
F28
setting
then
continue to
run at the set command speed. When UP/DOWN terminal is activated, the inverter
begins to accelerate/decelerate until the signal is released then.
It
run at the reached speed.
When the RUN signal is OFF, the inverter
decelerates
to stop
(
or coasts to stop
)
according to
the setting of F09. The
last output
frequency
when
the RUN signal
is
OFF, will be stored in F28.
UP/DOWN Key is unavailable in stop. The stored frequency can not be changed by Up/Down
Terminal, but can
be
changed by
the content of F28 by keypad.
2)
C40=001: the inverter will run from 0 Hz as
the
run signal is applied.
UP/DOWN operation method is same as C40=000. But on next RUN signal is ON, inverter
always starts up from 0Hz.
3)
C40=002: Same as when C
40
=001 but UP/DOWN is available while in stop mode.
Figure 4-17 Sleep/ Wake Mode